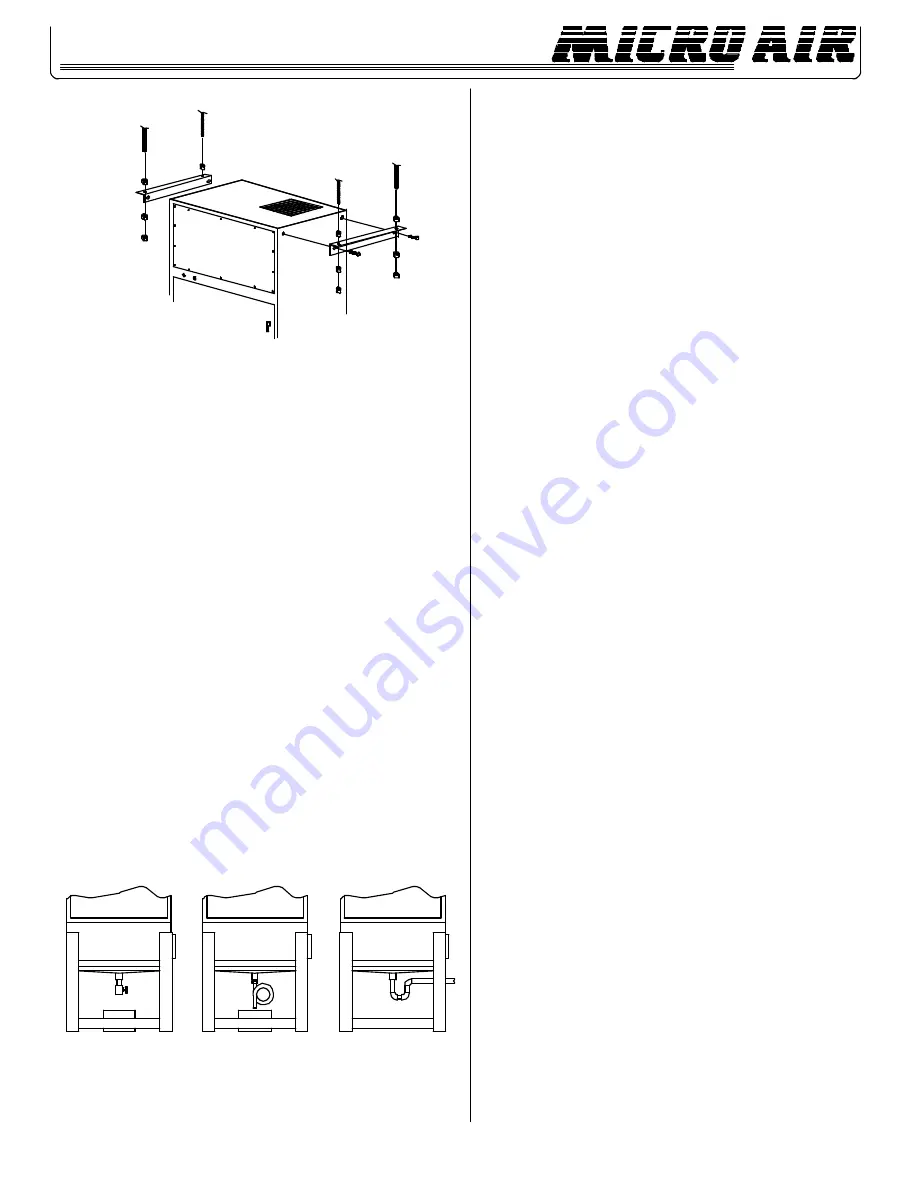
3.
Locate an installation site that will meet the requirements listed in Step 3 of
the wall mounting instruction.
4.
Firmly secure four lengths of 3/8” threaded rod to a firm structural support.
Space rods to match pattern made by holes in top of ceiling mount brackets.
5.
Thread one nut onto each rod.
CAUTION: The size and weight of the OM 500 requires two persons
or mechanical means to lift and hold during mounting.
6.
Raise the unit up to threaded rods and insert rods through ceiling mount
brackets. Thread a second nut onto each rod from below bracket.
7.
Level unit by tightening the nuts against the ceiling mount bracket.
8.
Thread a third nut onto each rod and tighten against the second nut to
prevent loosening of nuts due to vibration.
9.
Connect the unit to the oil mist source as explained in Step 6 of the wall
mounting instructions.
OIL DRAINAGE
NOTE: Should captured oil be disposed of, make sure to follow local codes.
Provision for draining oil from unit is provided for by a 1” NPT pipe coupling on the
bottom of the unit. Drainage can be piped to a central collection system or collected in
a bucket placed under the unit. In all cases a shut-off valve or drain trap is required to
prevent air bypass through the drain opening. One of the drain systems shown in
Fig.
4
should be used. Drain connection and lines are not provided.
NOTE:
Shutoff valve is installed in the drain system, the unit must be emptied regularly
to prevent oil from overflowing into the intake duct.
FIG. 3
ELECTRICAL CONNECTIONS
A.
SINGLE PHASE 120 VOLT
Be certain that the system ON/OFF switch is in the OFF position. Plug the power
cord into the nearest outlet rated for 120 volts.
B.
THREE PHASE 208-230/460 VOLT
1.
Conduit electrical connections should be made by a qualified electrician,
and must comply with local electrical codes.
CAUTION: Be sure that the designated circuit breaker is off until all
wiring has been completed.
NOTE:
It is recommended that a 1 HP motor starter/protector be used in
the supply circuit to this unit. See Wiring Diagram (
FIG. 6
).
2.
Remove the front motor compartment access cover.
3.
Remove the electrical wiring box cover.
4.
Make electrical connections to the input wires as shown in Wiring Diagram
(
FIG. 6
) for three phase wire connections.
NOTE:
The filter change indicator light circuit must be supplied with no
more than 270V. If a 460V, 3-wire source is used, a transformer replacement
kit (Part No. 30171-01) must be installed to provide proper voltage to the
indicator light.
5.
After wire connections are completed, affix conduit to side of unit via the 7/
8” diameter hole that is provided.
6.
Check blower for proper rotation direction. The blower should rotate
clockwise when viewed from the pulley end. If the blower rotates backwards,
interchange two of the motor connection wires.
PRE-OPERATION CHECKLIST
Before placing unit in service, check the following items:
•
Check blower drive belt for proper tension. (Belt should deflect approximately
1/2” when firm pressure is applied midway between the pulleys.)
•
Check that motor, blower, and drive pulleys are mounted securely.
•
Make sure that both corners of every pocket in the filter bag are supported
by the filter support rod and that the filter support rods are fully engaged in
their support brackets.
•
Air flow direction arrows on the oil impinger must point toward the blower.
•
Check that air intake and oil drain connections are air or oil tight.
•
Make sure that all access panels, removed during installation, are replaced,
and the filter access door is closed.
Unit is now ready to be placed in service.
AIR FLOW ADJUSTMENT
The OM 500 is equipped with variable diameter pulleys on the motor and blower to
allow the air flow to be adjusted to the installation requirements. The pulleys are set for
maximum air flow at the factory. The air flow rate can be reduced as follows:
1.
Remove motor compartment access cover. Be careful to avoid tearing gasket
material between the door and the cabinet.
2.
Remove belt from motor pulley.
3.
Loosen motor pulley adjustment set screw and screw adjustable shive out away
from fixed shive. Each turn will reduce the air flow by approximately 50 CFM.
Tighten set screw onto flat (see
FIG. 5
).
3
OM500
FIG. 4