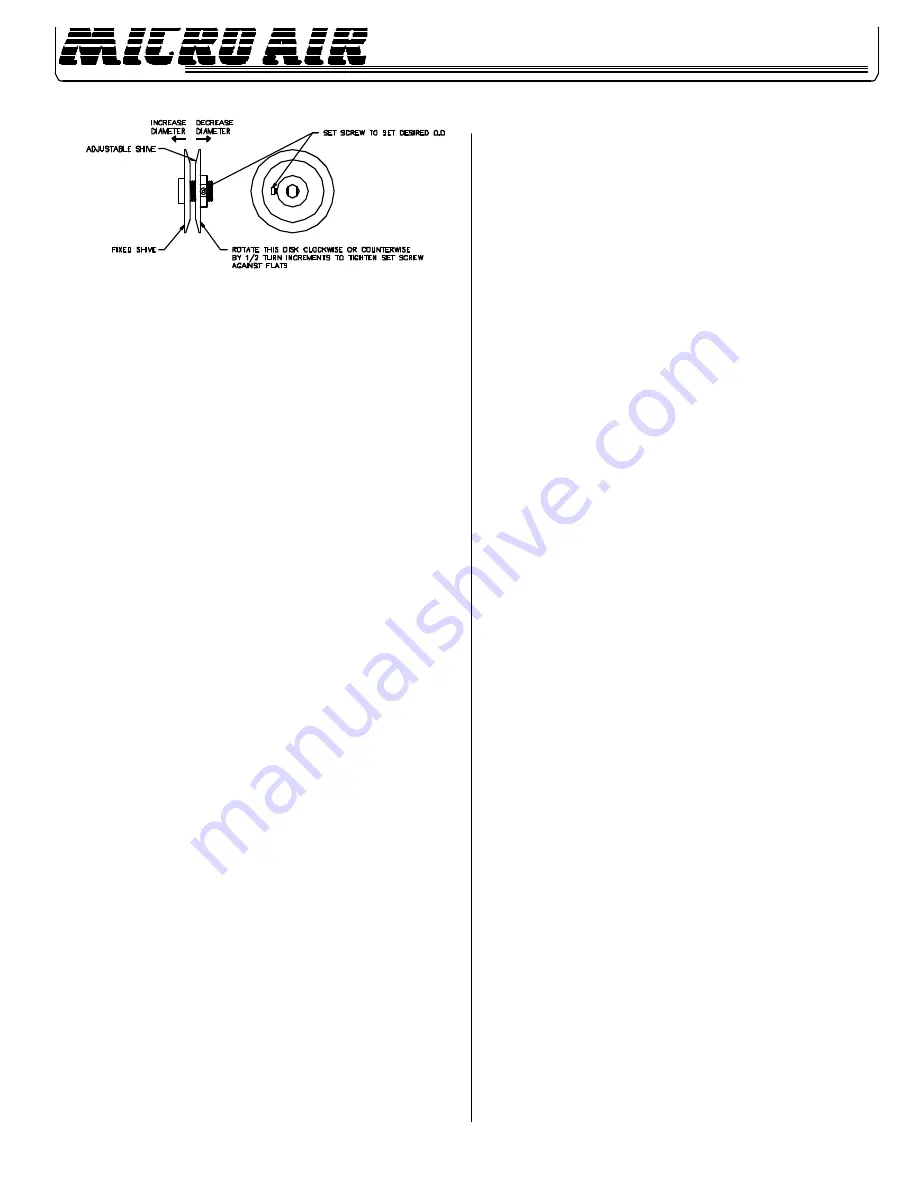
4.
Replace belt and check for belt tension. Proper tension should be approximately
1/2” deflection when the belt is squeezed together with normal pressure between
fingers.
5.
If tension is too loose, slide the motor away from the blower shaft via the slotted
holes located on the motor mount base.
6.
Replace motor compartment access cover.
7.
For multiple inlet application please refer to Micro Air
®
air flow balancing procedure
(Form L1141).
NOTE:
All filters and panels must be on the unit and door is closed for current
measurements of motor.
OPERATION
1.
The pressure switch is preset at the factory to indicate (light on) dirty filters, but
may need readjustment due to a desire for earlier or later filter changes, a different
combination of filters, or because the set point shifted during shipping. The
pressure switch is also orientation sensitive. To readjust the switch, remove the
hole plug in the side of the unit for access to the adjustment screw. Make sure
filters and pre-filters are installed in unit. Turn the unit on and place a piece of
cardboard over the intake covering about 80 to 85% of the intake area. On a 3-
inlet system, cover entirely two inlets and a little more than half of the area of the
third inlet. With a standard screwdriver, turn the adjustment screw clockwise
until the light goes off, or counterclockwise until the light comes on.
2.
For more time between filter changes (less air flow), cover slightly more of the
opening, and for less time between filter changes (more air flow), cover less of
the opening.
3.
No lubrication is required for the motor because it is a permanent pre-lube design.
Excessive dirt/oil should be periodically removed.
4.
Make sure oil is draining easily through drain pipe.
FIG. 5
CHANGING FILTERS
CAUTION: Always make sure that the unit is turned off before changing filters or
servicing the unit.
1.
The OM 500 is equipped with a filter change light, or an optional Magnehelic
Gauge, which indicates when a filter needs to be replaced. If the differential
pressure has been set properly, the light signals the need for examination of the
filters.
2.
When the light comes on, or the gauge reads high differential pressure, turn the
unit off and remove the impinger pre-filter from the unit. Wash the pre-filter in a
detergent solution to remove dirt and oil residue.
3.
Rinse the pre-filter thoroughly with water, shake dry and replace it into the unit
with airflow direction pointing to the blower.
4.
Turn on the unit. If the filter change light fails to go out, or the gauge continues to
read high differential pressure, after replacing the pre-filter, then the oil bag filter
may also need to be replaced.
5.
Visually inspect the bag filter. If the pockets are loaded with oil and dirt, then
remove the filter from the channel and insert a new filter.
6.
Start the unit. The filter change light should be off, or the gauge reads low differential
pressure, and the unit operating properly.
GENERAL MAINTENANCE
1.
Occasionally check the condition of the drive belt for tightness and wear.
2.
Check the blower bearings for unusual wear and the blower wheel for debris and
dirt. Clean when necessary.
3.
Check the wiring for loose connections or cracked insulation.
4.
No lubrication is required for the motor because it is a permanent pre-lube design.
Excessive dirt/oil should be periodically removed.
5.
Make sure that oil is draining easily through drain pipe.
4
OM500