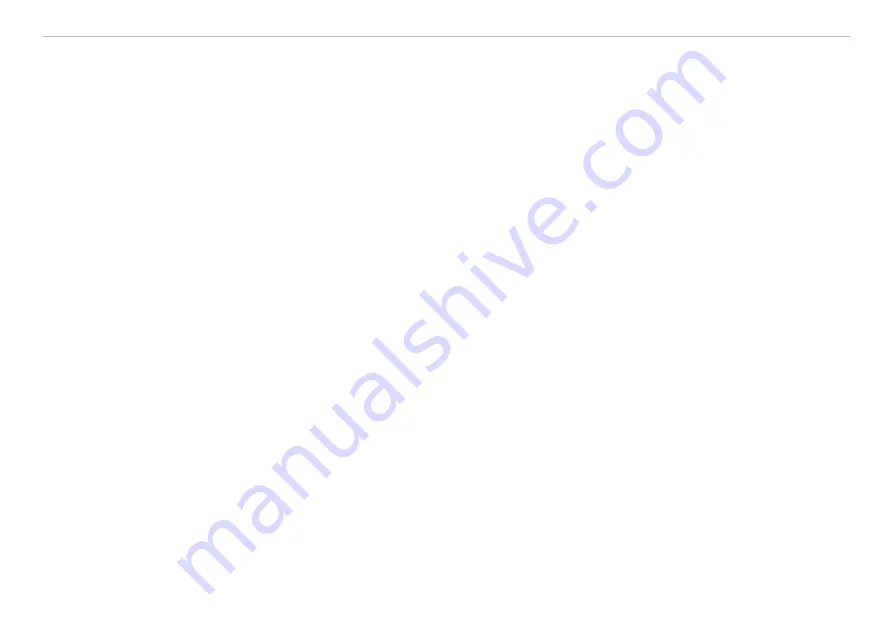
Page 11
Safety
optoNCDT 1900 / EtherCAT
1.5
Proper Environment
- Protection class:
IP67 (applies only when sensor cable is plugged in)
Lenses are excluded from the protection class. Contamination of the lenses causes impairment or failure of the function.
- Temperature range:
Operation:
0 ... 50 °C
Storage:
-20 ... 70 °C
- Humidity:
5 - 95% (non-condensing)
- Ambient pressure: Atmospheric pressure
i
The protection class is limited to water, no penetrating liquids or the like.
Summary of Contents for ILD1900-10
Page 8: ...optoNCDT 1900 EtherCAT ...
Page 110: ...Page 110 Appendix EtherCAT Documentation optoNCDT 1900 EtherCAT ...
Page 111: ......