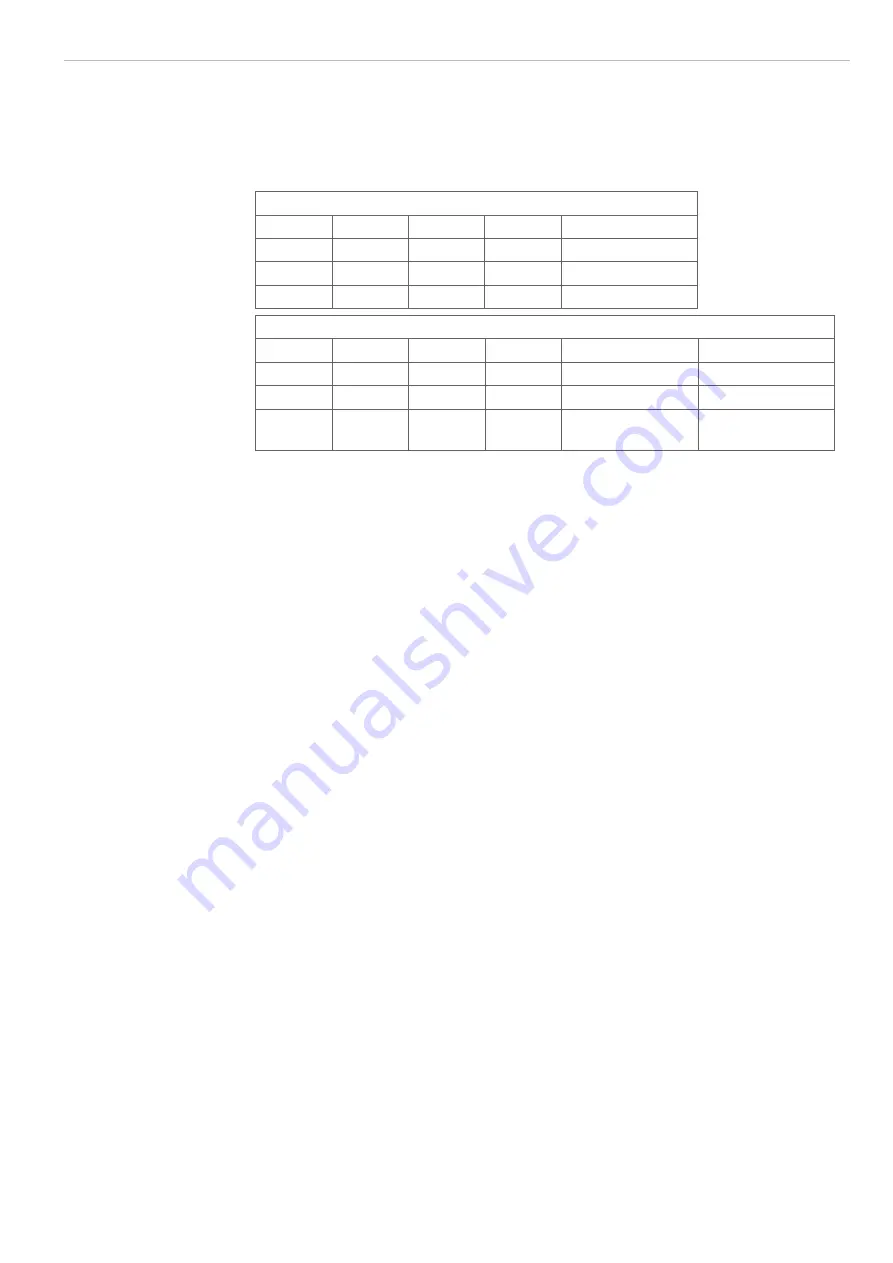
Page 47
Measure
optoCONTROL 2600
6.6.3.8 Read out min/max Values Followed by Reset
Name
RD MINMAX RESET
Description:
After the command response the min/max values are transmitted
in the range 0 ... 65519.
Then the min/max content is set to zero.
Command:
Byte 1
Byte 2
Byte 3
Byte 4
hex
„+“
„+“
„+“
0x0D
0x0D2B2B2B
„0“
„D“
„C“
„1“
0x3143444F
0x34
0x20
0x00
0x00
0x00002034
Response:
Byte 1
Byte 2
Byte 3
Byte 4
hex
Remark
„0“
„D“
„C“
„1“
0x3143444F
0x34
0xA0
0x04
0x00
0x0004A034
Without error
0x34
0xE0
0x03
0x00
0x0003E034
Error + 4 bytes
error code
Min [0...65519]:
Binär -
0x00008B3E
Max [0...65519]:
Binär -
0x00008B4B
Min/Max[mm] Min/Max[0...65519] * 40.824 / 65519 - 0.4204872
Summary of Contents for ODC 2600-40
Page 81: ......