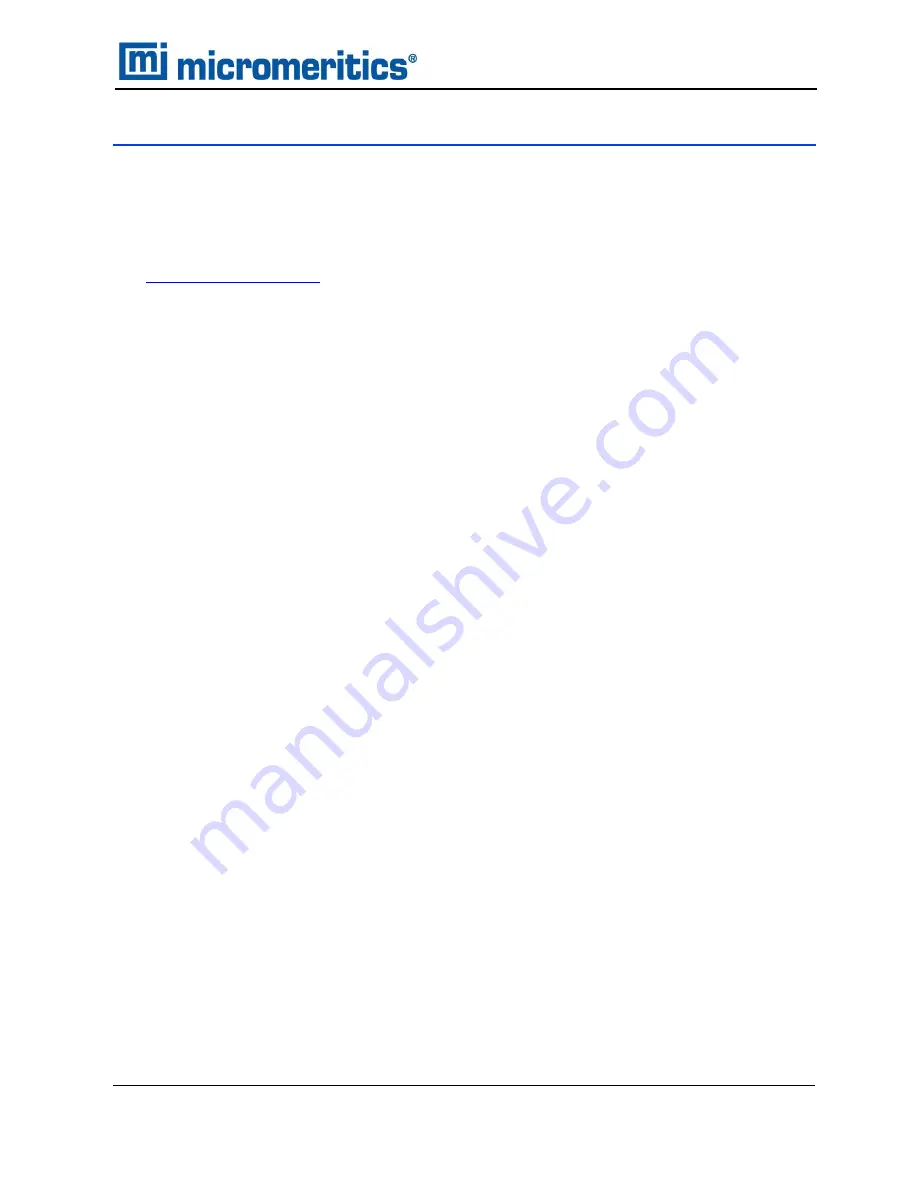
C
ONTACT
U
S
Micromeritics Instrument Corporation
4356 Communications Drive
Norcross, GA / USA / 30093-2901
Phone: 1-770-662-3636
Fax: 1-770-662-3696
Instrument Service or Repair
Phone: 1-770-662-3666
International — contact your local distributor or call 1-770-662-3666
Service.Helpdesk@Micromeritics.com
Micromeritics Learning Center
Phone: 1-770-662-3607
www.Micro.edu
Contact Us
VacPrep Operator Manual
061-42802-01 (Rev B) — Apr 2021
iv