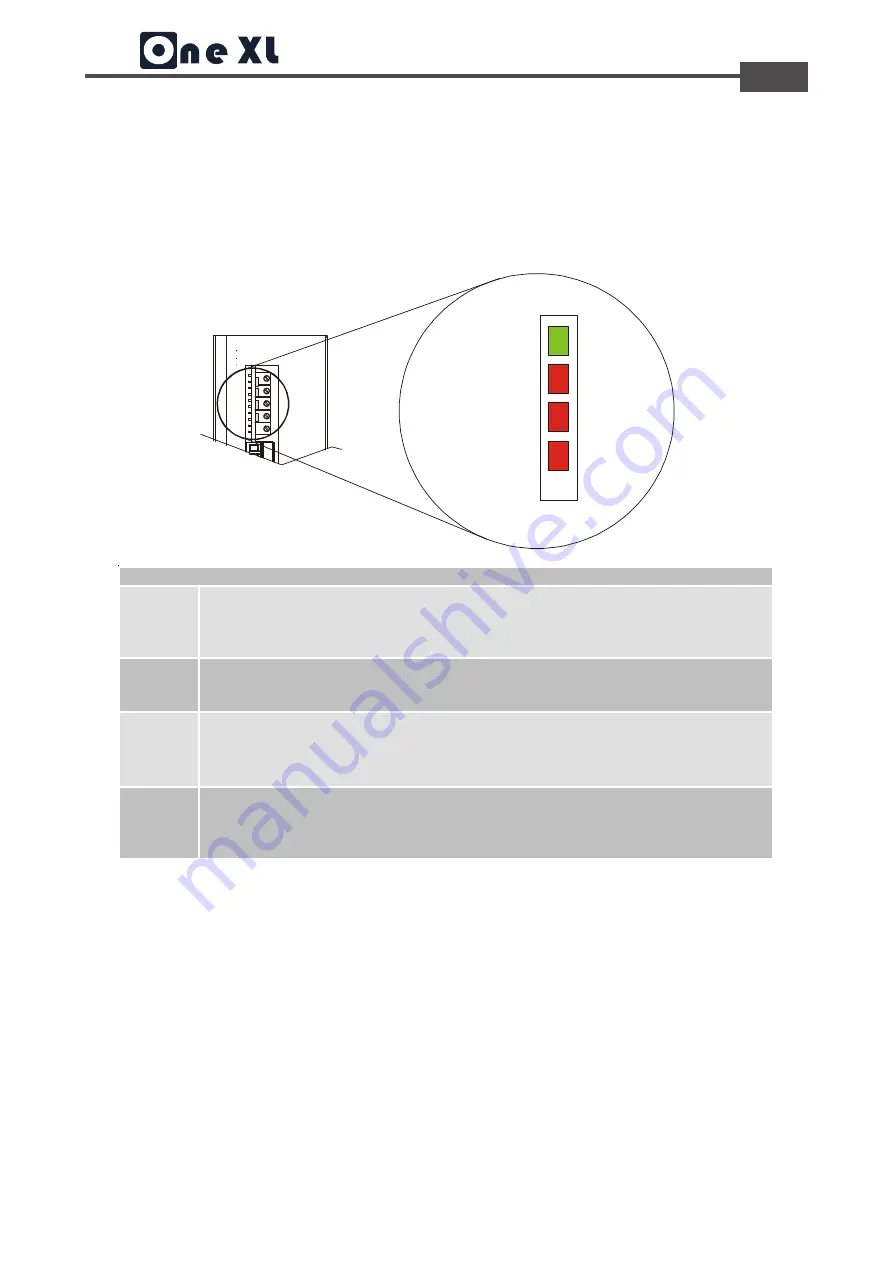
33
Service Manual
www.microphase.eu
Dc
Possible reason for the allarms of the drive
The protections are all displayed by four LEDs on the front of the drive. It also comes with a series of
protections designed to safeguard in case of malfunction, the drive and the motor.
4.8
Indicator Leds and protections
- When power supply is on the green OK LED doesn't come on.
Check the voltage bHV
and -GND with a tester.
- During deceleration of the motor, the LED green blinks.
Increase the capacity filter. (example
from 10.000uF to 20.000uF)
- LED lights red O.C.
Check the conne M and-M can short circuit between these two
wires, between one of these two wires and ground, or short circuit inside the motor.
- LED lights red ixt.
Excessive mechanical load
- LED lights red PTC.
Ambient temperature too high, or the converter does not have a minimum
circulation of air cooling, ventilation or missing where expected from the size of the converter.
- With the green LED the motor will not start when you enable the drive with START
Check for the enable signal START. Also verify the presence of the speed signal between the
ter /-VEL
- Motor goes out of control when enabled.
- Encoder signals incorrectly connected (ENC A and ENC B signals swapped, or encoder power
supply missing, or tachogenerator signals swapped)
OK
OK
IxT
PTC
OC
IxT
PTC
O.C
FUNCTION
OK
GREEN
Normally ON. Indicating the proper operation of all functions. It turns OFF in case of
any anomaly "except protection intervention IxT". The faults that affect this LED are:
Over/Under input voltage. Over temperature (PTC).
Short Circuit (O.C), outputs shorted to each other or to ground.
IxT
RED
Normally OFF.
This indicator is lit if the converter exceeding the limit calibration of
the rated current of the motor. When the current drawn back under the nominal pre-
set, the alarm will auto resets and the LED turns off by itself.
PTC
RED
Normally OFF.
This indicator is lit when the internal temperature of the drive
reaches 75°C . Remove power and wait for the drive to cool before re-applying
power. The operation causes the blocking of the drive and the storage of the alarm.
NOTE: A fan, heat sink or air conditioner may be needed to remedy the problem.
O.C
RED
Normally OFF. Indicates that between the motor terminals and/or ground, has been
a short circuit. The operation causes the blocking of the drive and the storage of the
alarm. Remove power supply and examine the motor connecting leads for shorts,
before re-powering the converter to reset the alarm.