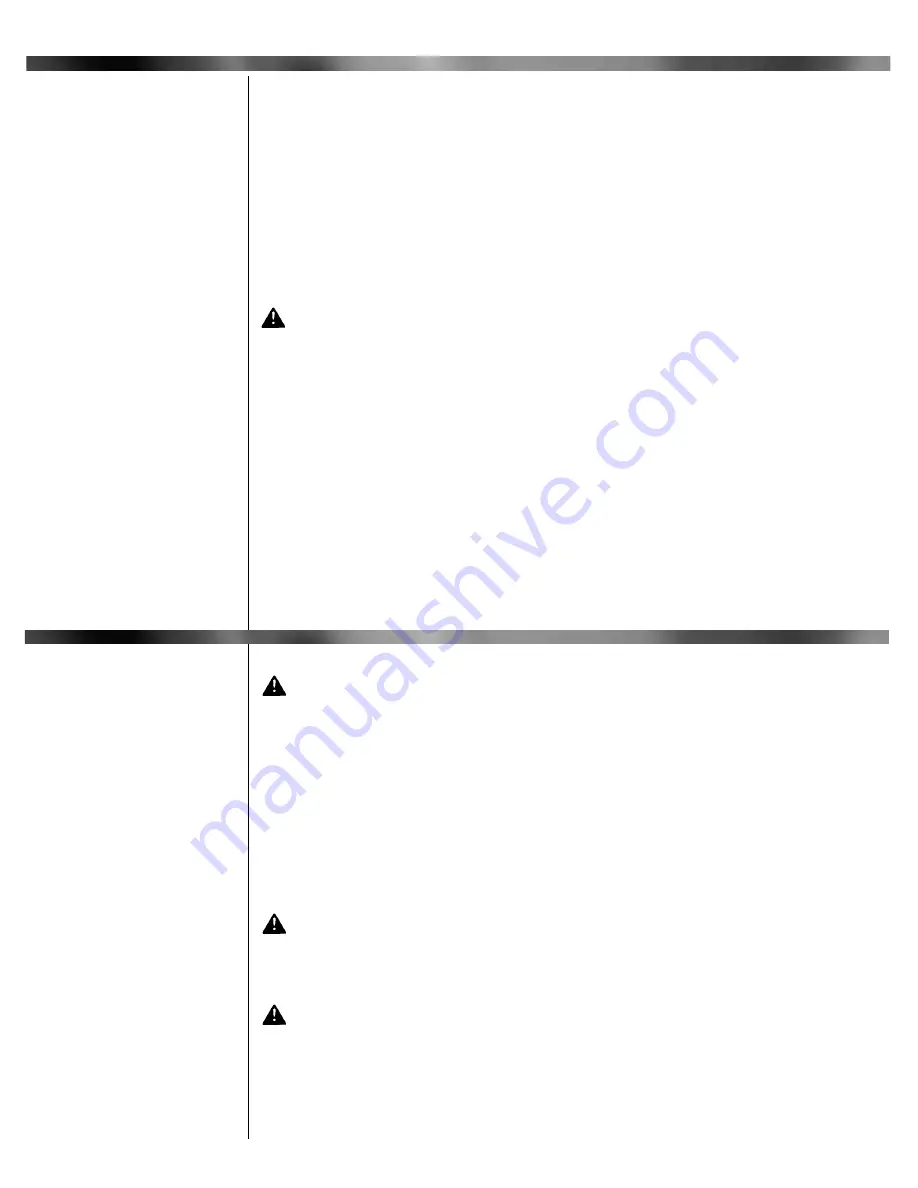
The 24 volt Combination Valve serves four functions:
1.
Main Manual Gas Shut-off,
2.
Manifold
gas pressure regulation,
3.
Automatic electric main gas valve; single seated on Model 400B-02,
double seated (redundant) on Model 400B-02P, and
4.
Pilotstat safety control. A pilot adjustment
screw and filter are also included.
The pilot adjustment screw is located on the inlet end of the valve body. Remove plug for
access and turn clockwise to reduce flow.
The main gas regulator, which has an outlet pressure setting range of 2.0" to 4.0" W.C. NAT-
URAL (8.0" to 11.0" W.C. PROPANE) is factory set for a manifold gas pressure of 2.0" W.C. NAT-
URAL (8.0" W.C. PROPANE). If pressure adjustment is required for setting capacity, remove regu-
lator cap for access to slotted adjustment screw. Turning of adjustment screw counterclockwise
reduces pressure; clockwise increases pressure. Do not adjust past point where no change in
pressure is noted.
Note:
Pressure setting can only be made with burner running and gas on. Manifold gas pressure
tap is located in spud holder (See Figure 6 or 7).
CAUTION: If gas supply pressure is below its specified range during adjust-
ment, an overfire condition could result when pressure returns to normal, par-
ticularly if the regulator adjustment screw is bottomed out.
ALWAYS confirm that
at least the minimum rated gas pressure is being supplied to the burner during regulator
adjustments, and NEVER bottom out regulator screw.
If the pressure regulator fails to maintain a constant manifold gas pressure within ±0.1" W.C.,
and it is confirmed that the inlet gas pressure to the Combination Valve is a steady 14.0" W.C.
maximum during standby, and a steady 5.0" W.C. minimum with the flame on, the regulator portion
of the valve is defective and the entire valve must be replaced.
The pilotstat safety control may be suspect, if frequent
pilot outages
occur. Refer to Section
IX, 2 thru 5, for the method of isolating the problem.
If, on a call for heat, the main burner fails to operate even though the pilot is burning and the
motor is running, failure of the electric valve operator(s) may be indicated. Refer to the
Trouble
Chart
for further information.
10
Consumer Instructions
CAUTION: If the Combination Valve has been moved or replaced, soap bub-
ble test for leaks with the burner running.
If leakage through the valve occurs, as evidenced by an abnormally large yellow (sooty) flame
on standby, the entire valve should be replaced.
Keep the area around the burner clear and free of combustible materials, gasoline and other
flammable liquids or vapors. Do not obstruct burner air inlet slots or ventilation grilles for combus-
tion air.
The motor features permanently lubricated ball bearings and requires no routine oiling mainte-
nance.
IMPORTANT:
Check the burner flame seasonally. A proper NATURAL gas flame will appear blue
at the burner face with orange and yellow tips. A proper PROPANE gas flame will appear blue at
the burner face with yellow tips. If the flame is too rich, it will appear billowy and yellow with hazy
tips. If too lean, it will appear short and all blue. If the flame does not appear proper,
CONTACT A
QUALIFIED SERVICE TECHNICIAN FOR CLEANING AND/OR READJUSTMENT.
WARNING: If any flame is observed other than pilot when the burner is on
standby, or valve operator is heard to come on before the motor reaches oper-
ating speed, immediately turn off the manual gas control and burner power. A
dangerous condition has developed and must be corrected.
CONTACT A QUALI-
FIED SERVICE TECHNICIAN FOR CLEANING READJUSTMENT AND/OR REPAIR.
WARNING: If PROPANE gas is used and the burner is located in a base-
ment, crawl space or confining space, contact your gas supplier about
installing a GAS LEAK warning device. PROPANE gas is heavier than air and
can settle in low areas or confined spaces. This would create a danger of
explosion or fire. If you suspect a gas leak, follow instructions on front cover
of this manual.
XI Combination
Gas Valve
Maintenance