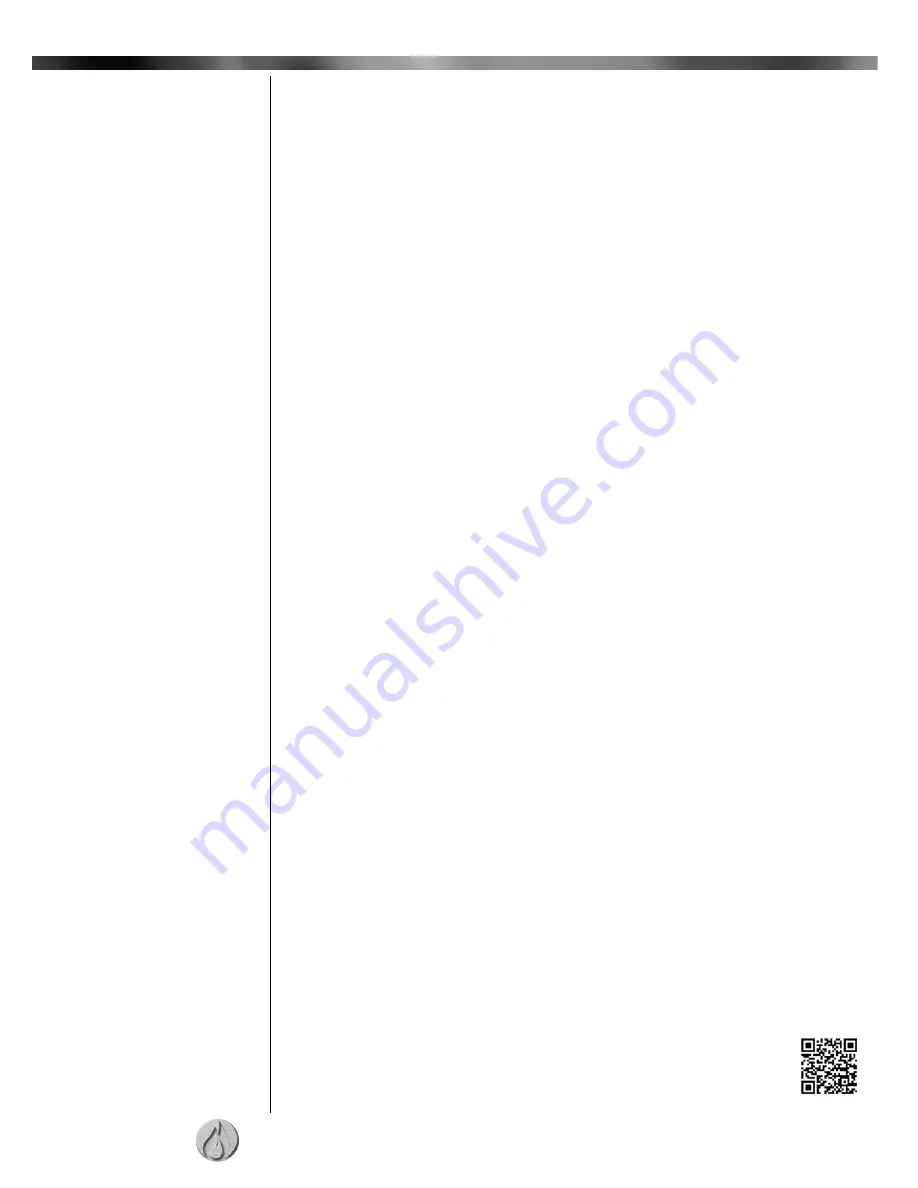
12
Midco International Inc.
4140 West Victoria Street * Chicago, Illinois 60646
tel 773.604.8700 fax 773.604.4070 web www.midco-intl.com email sales@midco-intl.com
2. Check for 24V* between valve TH (PWR) terminal and valve body:
a. With voltage, reset Electronic Control and listen for audible CLICK as first
valve operator opens. No CLICK, replace valve.
3. Check for ignition spark (spark length approximately 1/8"). Since this is a
capacitor discharge system, observe closely when visually checking the spark as
it is faint and thread-like and may be overlooked in bright light.
a. Between Electronic Control high voltage terminal and strip terminal GND. No
spark, defective Electronic Control.
b. Between Electronic Control high voltage terminal and Spark Electrode Wire
(insert head of #8x3/4" or longer round head screw into terminal wire). No
spark, broken wire or cracked insulator, or "spark gap" too wide (see Section
IX).
c. Between electrode tip and top of ground rod (see Figure 7). If electrode tip is
not visible but spark can be heard continue with test II.C.4.
d. If spark is not heard, remove drawer assembly (see Section IX) and ground it
solidly to burner metal. Repeat test c. above.
4. TURN MANUAL GAS COCK KNOB ON. Connect manometer to the manifold gas
pressure tap and, during trial for ignition, check the gas pressure:
a. Pressure should be between 1.5" and 3.5" W.C. NATURAL (10.0 W.C."
PROPANE), and steady. Verify per Section VII that the spud orifice size and
manifold pressure are correct.
b. Zero, erratic, low or high pressure: confirm that the inlet pressure to the
combination valve is between 5.0" and 14.0" W.C. for NATURAL (11.0" to
14.0" W.C. PROPANE), during standby and during trial for ignition.
c. If manifold pressure is zero, below 1.5" or above 3.5" W.C. NATURAL (10.0"
W.C. PROPANE) or erratic, replace combination valve.
III. FLAME ON ONLY DURING 6-SECOND TRIAL FOR IGNITION.
A. With motor running check burner line voltage terminals for 120V as follows:
1. Between strip terminals 1 and 2 - 120V; voltage OK.
2. Between strip terminals 1 and GND - 120V; ground OK.
3. Between strip terminals 2 and GND -"0"V; no backfeed OK.
B. Follow reset procedure as specified in step II.B.
1. Check flame rod position per Figure 7.
2. Check sensor wire for continuity.
3. Connect DC microammeter in series Electronic Control SENSE terminal and
sensor wire. With flame on, flame signal should be at least 2 microamps.
C. IMPORTANT: If changes are made in the Main Spud Orifice size, Manifold Gas
Pressure or Primary Air Adjustment, change the installation data tag accordingly.
IV. SHORT FLAME.
A. Low gas pressure.
B. Primary air adjustment open too far.
C. Main spud orifice too small.
V. LONG HAZY FLAME.
A. High gas pressure.
B. Primary air adjustment closed too far.
C. Dirty blower wheel.
D. Main spud orifice too large.
VI. GAS FAILS TO SHUT OFF.
A. Defective combination valve.
* Normal low voltage:
Motor running - 24V minimum.
Combination valve energized - 21V minimum.
Trouble Chart
Trouble Chart
Continued
1207
8470 72
Printed in USA