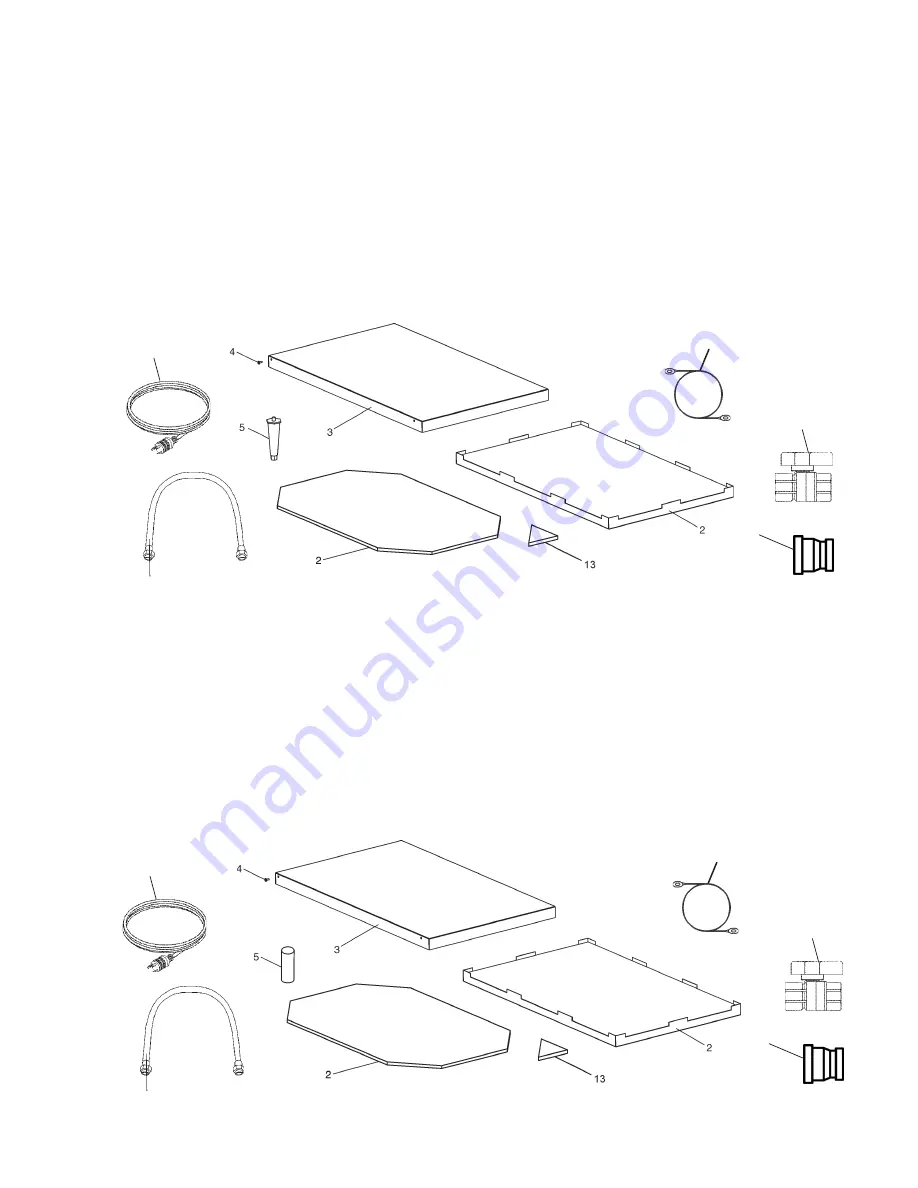
SECTION 2
INSTALLATION
9
Figure 2-1 (continued). PS528-Series Gas Oven Installation Parts
ITEM NO.
QTY
PART NO.
DESCRIPTION
1
2
62208
INSULATION BOTTOM TRAY
2
1
62206
BOTTOM TRAY WELDMENT
3
1
61650
TOP COVER
4
4
51387
SCREW MSSLT THREAD 8-32 × 1/2, 18-8
5
4
M3828
PIN, ALIGNMENT
7
1
22450-0228
GAS HOSE RESTRAINT CABLE
8
3
22361-0001
GAS HOSE
9
1
49975
CORD & PLUG NEMA L6-20P
10
1
23115-0009
MANUAL GAS VALVE, 3/4
″
× 1/2, COUPLER
11
1
31823
REDUCER, 3/4
″
– 1/2
″
12
2
59227
HEAT GUARD
13
4
62207
INSULATION
PARTS LIST FOR SERIES PS528 Gas OVEN
INSTALLATION KIT Triple Stack Oven P/N 63948
7
8
ITEM NO.
QTY
PART NO.
DESCRIPTION
1
2
62208
INSULATION BOTTOM TRAY
2
1
62206
BOTTOM TRAY WELDMENT
3
1
61650
TOP COVER
4
4
51387
SCREW MSSLT THREAD 8-32 × 1/2, 18-8
5
4
3101908
LEG 4
″
AD FT
7
1
22450-0228
GAS HOSE RESTRAINT CABLE
8
2
22361-0001
GAS HOSE
9
1
49975
CORD & PLUG NEMA L6-20P
10
1
23115-0009
MANUAL GAS VALVE, 3/4
″
× 1/2, COUPLER
11
1
31823
REDUCER, 3/4
″
– 1/2
″
12
1
59227
HEAT GUARD
13
4
62207
INSULATION
PARTS LIST FOR SERIES PS528 Gas OVEN
INSTALLATION KIT Double Stack Oven P/N 63947
7
8
9
9
11
10
11
10