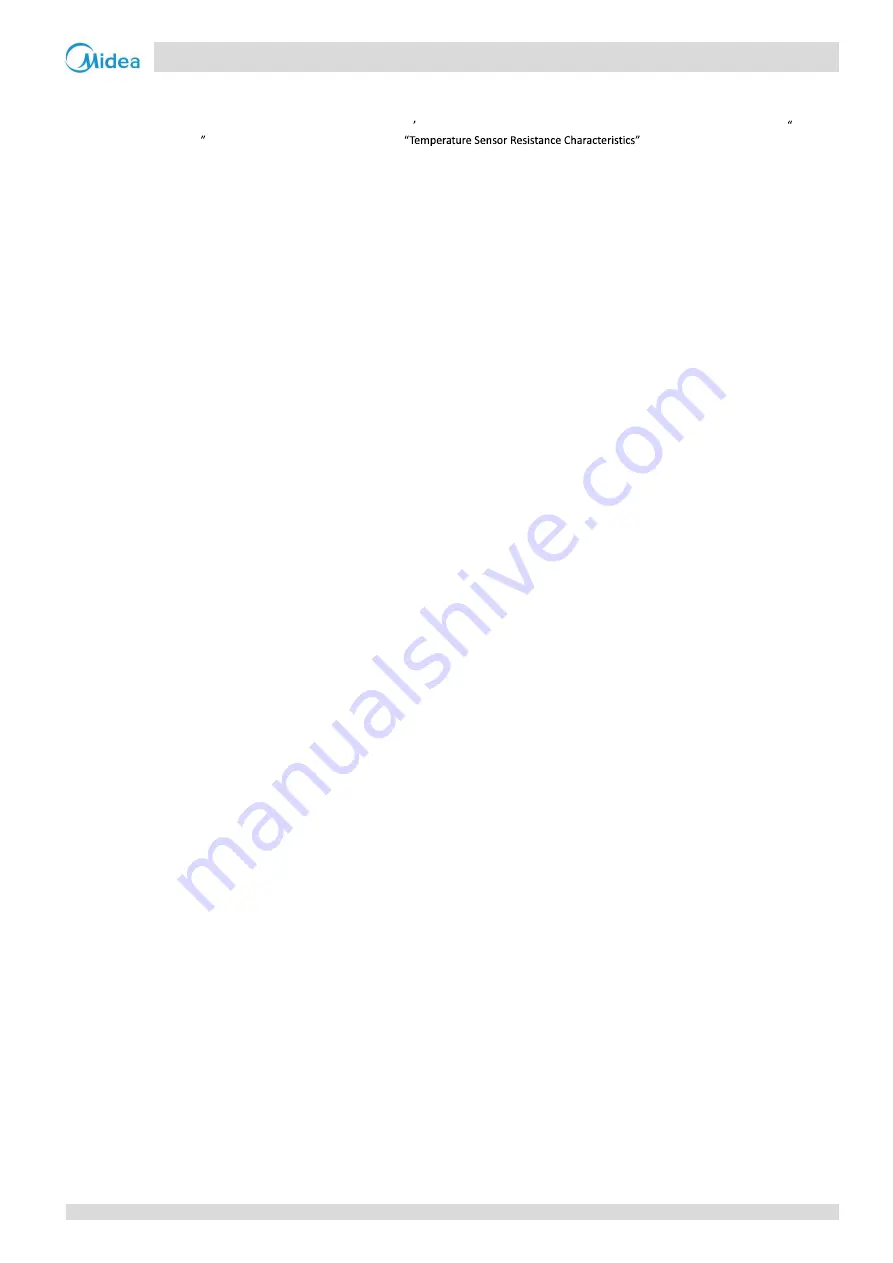
M thermal Mono
202008 65
main PCB (labeled 10 in Figure 4-2.1). Domestic hot water tank temperature sensor connection is port CN13 on hydronic system main PCB (labeled 13 in
Figure 4-2.1).
3. Set a multi-meter to buzzer mode and test any two terminals of sensor. If the resistance is too low, the buzzer sounds, which means the sensor has
short-circuited. If the resistance is not consistent with the sensor s resistance characteristics table, the sensor has failed. Refer to Part 2, 1 Layout of
Functional Components and to Table 5-5.1 or 5-5.2 in Part 5, 5.1
.
4.
High pressure switch connection is port CN31 on the outdoor unit refrigerant system main PCB (labeled 21 in Figure 4-2.2).
Measure the resistance among the three terminals of the pressure sensor. If the resistance is of the order of mega Ohms or infinite, the pressure sensor
has failed.
High pressure side blockage causes discharge temperature to be higher than normal, discharge pressure to be higher than normal and suction pressure to
be lower than normal.
5.
Check air side heat exchanger, fan and air outlets for dirt/blockages.
6.
Check the water side heat exchanger, water piping, circulator pumps and water flow switch for dirt/blockages.
Midea CAC Confidential