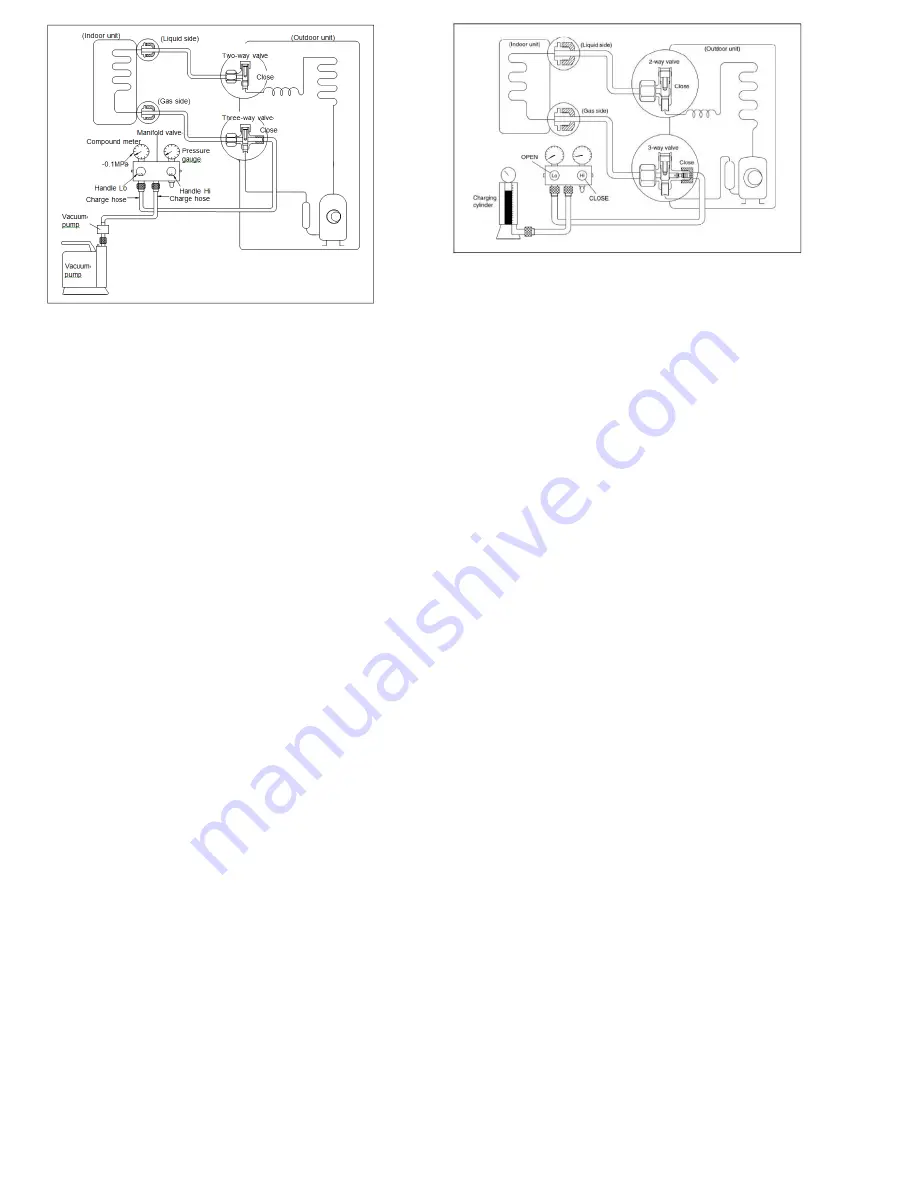
1. Completely tighten the flare nuts of the indoor
and outdoor units, confirm that both the 2-way
and 3-way valves are set to the closed
position.
2. Connect the charge hose with the push pin of
handle lo to the 3-way valves gas service
port..
3. Connect the charge hose of handle hi
connection to the vacuum pump.
4. Fully open the handle Lo of the manifold valve.
5. Operate the vacuum pump to evacuate.
6. Make evacuation for 30 minutes and check
whether the compound meter indicates -
0.1Mpa(14.5Psi). If the meter does not indicate -
0.1Mpa(14.5Psi) after pumping 30 minutes, it
should be pumped 20 minutes more. If the
pressure can’t achieve -0.1Mpa(14.5Psi) after
pumping 50 minutes, please check if there are
some leakage points. Fully close the handle Lo
valve of the manifold valve and stop the
operation of the vacuum pump. Confirm that the
gauge needle does not move (approximately 5
minutes after turning off the vacuum pump).
7. Turn the flare nut of the 3-way valves about
45° counterclockwise for 6 or 7seconds after
the gas coming out, then tighten the flare nut
again. Make sure the pressure display in the
pressure indicator is a little higher than the
atmosphere pressure. Then remove the
charge hose from the 3 way valve.
8. Fully open the 2 way valve and 3 way valve
and securely tighten the cap of the 3 way
valve.
2. Air purging by refrigerant
Procedure:
1). Confirm that both the 2-way and 3-way valves
are set to the closed position.
2). Connect the charge set and a charging cylinder
to the service port of the 3-way valve.
3). Air purging.
Open the valves on the charging cylinder and the
charge set. Purge the air by loosening the flare
nut on the 2-way valve approximately 45’ for 3
seconds then closing it for 1 minute; repeat 3
times.
After purging the air, use a torque wrench to tighten
the flare nut on the 2-way valve.
4). Check the gas leakage.
Check the flare connections for gas leakage.
5). Discharge the refrigerant.
Close the valve on the charging cylinder and
discharge the refrigerant by loosening the flare
nut on the 2-way valve approximately 45’ until the
gauge indicates 0.3Mpa(43.5Psi) to 0.5
Mpa(72.5Psi)..
6). Disconnect the charge set and the charging
cylinder, and set the 2-way and 3-way valves to
the open position.
Be sure to use a hexagonal wrench to operate the
valve stems.
7). Mount the valve stems nuts and the service port
cap.
Be sure to use a torque wrench to tighten the
service port cap to a torque 18N·m.
Be sure to check the gas leakage.
3. Adding refrigerant if the pipe length
exceeds chargeless pipe length
Summary of Contents for M2OC-18HFN1-M
Page 19: ...8 Wiring Diagrams 8 1 Wiring diagram of 1 drive 2 outdoor M2OC 18HFN1 M M2OD 18HFN1 M...
Page 20: ...PCB board of M2OC 18HFN1 M M2OD 18HFN1 M...
Page 21: ...IPM board of M2OC 18HFN1 M...
Page 22: ...IPM board of M2OD 18HFN1 M...
Page 23: ...8 2 Wiring diagram of 1 drive 3 outdoor M3OD 27HRDN1 M M3OC 30HRFN1 M...
Page 24: ...PCB board of M3OC 30HRFN1 M...
Page 25: ...IPM board of M3OC 30HRFN1 M...
Page 26: ...PCB board of M3OD 27HRDN1 M...
Page 27: ...IPM board of M3OD 27HRDN1 M...
Page 28: ...8 3 Wiring diagram of 1 drive 4 outdoor M4OC 36HRFN1 M...
Page 29: ...PCB board of M4OC 36HRFN1 M...
Page 30: ...IPM board of M4OC 36HRFN1 M...
Page 31: ...PFC board of M4OC 36HRFN1 M...
Page 66: ...IPM for dual tri zone IPM for qua zone P N for dual tri zone...
Page 67: ...P N for qua zone...
Page 68: ...bridge rectifier for dual tri zone bridge rectifier for qua zone...
Page 69: ...Remark Measure the DC voltage between and port The normal value should be 190V 250V...
Page 71: ...Two ports of the inductance Inductance...
Page 72: ......
Page 77: ......
Page 79: ......
Page 81: ......
Page 83: ......
Page 96: ...6 EXV check Disconnect the connectors...
Page 98: ...Red Blue Red Yellow...
Page 99: ...Brown Orange Brown White...
Page 114: ...Screws of front panel Screws of right rear panel Screws of top cover...
Page 128: ......