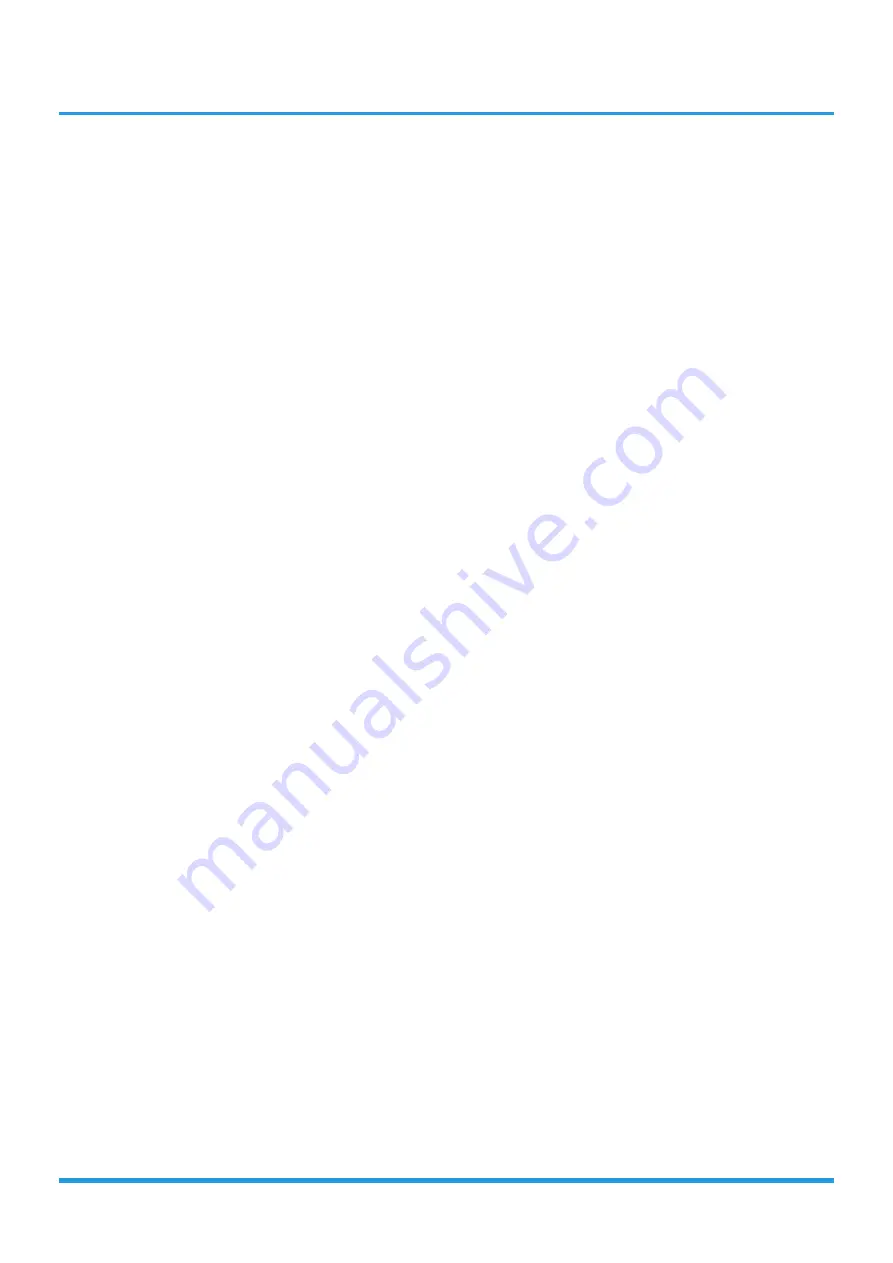
7. Vacuum Drying and Leakage Checking
7. Vacuum Drying and Leakage
Checking
7.1 Purpose of vacuum drying
•
Eliminating moisture in system to prevent the phe-
nomena of ice-blockage and copper oxidation
.
Ice-blockage shall cause abnormal operation of
system, while copper oxide shall damage
compressor.
•
Eliminating the non-condensable gas (air) in system
to prevent the components oxidizing, pressure fluc-
tuation and bad heat exchange during the operation
of system.
7.2 Selection of vacuum pump
•
The ultimate vacuum degree of vacuum pump shall
be -756mmHg or above.
•
Precision of vacuum pump shall reach 0.02mmHg or
above.
7.3 Operation procedure for vacuum drying
Due to different construction environment, two kinds of
vacuum drying ways could be chosen, namely ordinary
vacuum drying and special vacuum drying.
7.3.1
Ordinary vacuum drying
1.
When conduct first vacuum drying, connect pressure
gauge to the infusing mouth of gas pipe and liquid pipe,
and keep vacuum pump running for 1hour (vacuum
degree of vacuum pump shall be reached -755mmHg).
2. If the vacuum degree of vacuum pump could not reach
-755mmHg after 1 hour of drying, it indicates that there is
moisture or leakage in pipeline system and need to go on
with drying for half an hour.
3. If the vacuum degree of vacuum pump still could not
reach -755mmHg after 1.5 hours of drying, check whether
there is leakage source.
4 . Leakage test: After the vacuum degree reaches
-755mmHg, stop vacuum drying and keep the pressure for
1 hour. If the indicator of vacuum gauge does not go up,
it is qualified. If going up, it indicates that there is moisture
or leak source.
7.3.2
Special vacuum drying
The special vacuum drying method shall be adopted when:
1. Finding moisture during flushing refrigerant pipe.
2. Conducting construction on rainy day, because rain
water might penetrated into pipeline.
3. Construction period is long, and rain water might
penetrated into pipeline.
4. Rain water might penetrate into pipeline during
construction.
Procedures of special vacuum drying are as follows:
1. Vacuum drying for 1 hour.
2. Vacuum damage, filling nitrogen to reach 0.5Kgf/cm
2
.
Because nitrogen is dry gas, vacuum damage could
achieve the effect of vacuum drying, but this method
could not achieve drying thoroughly when there is too
much moisture. Therefore, special attention shall be drawn
to prevent the entering of water and the formation of
condensate water.
3. Vacuum drying again for half an hour.
If the pressure reached -755mmHg, start to pressure
leakage test. If it cannot reached the value, repeat vacuum
damage and vacuum drying again for 1 hour.
4. Leakage test: After the vacuum degree reaches
-755mmHg, stop vacuum drying and keep the pressure for
1 hour. If the indicator of vacuum gauge does not go up,
it is qualified. If going up, it indicates that there is moisture
or leak source.
Summary of Contents for MUEU-18HRFNX-QRD0W
Page 1: ...LIGHT COMMERCIAL INVERTER SERIES SM_LC GA _R410A_R32_3D INV_EU_NA_1811 SERVICE MANUAL...
Page 2: ......
Page 5: ......
Page 6: ...Contents 1 Precautions 2 2 Information servicing For flammable materials 3 Safety Precautions...
Page 12: ...Contents 1 Model Reference 2 2 External Appearance 3 Model Reference...
Page 15: ...Model Reference 4 2 2 Outdoor Unit Outdoor Unit...
Page 19: ...IDU Compact Cassette 4 2 Dimensional Drawings...
Page 21: ...IDU Compact Cassette 6 4 Service Place...
Page 44: ...Outdoor Unit 3 Panel Plate B30...
Page 45: ...Outdoor Unit 4 Panel Plate BA30...
Page 46: ...Outdoor Unit 5 Panel Plate CA30...
Page 47: ...Outdoor Unit 6 Panel Plate D30...
Page 48: ...Outdoor Unit 7 Panel Plate E30...
Page 49: ...Outdoor Unit 8 Panel Plate 590...
Page 50: ...Outdoor Unit 9 2 Service Place...
Page 62: ...Outdoor unit printed circuit board diagram 17122000002718...