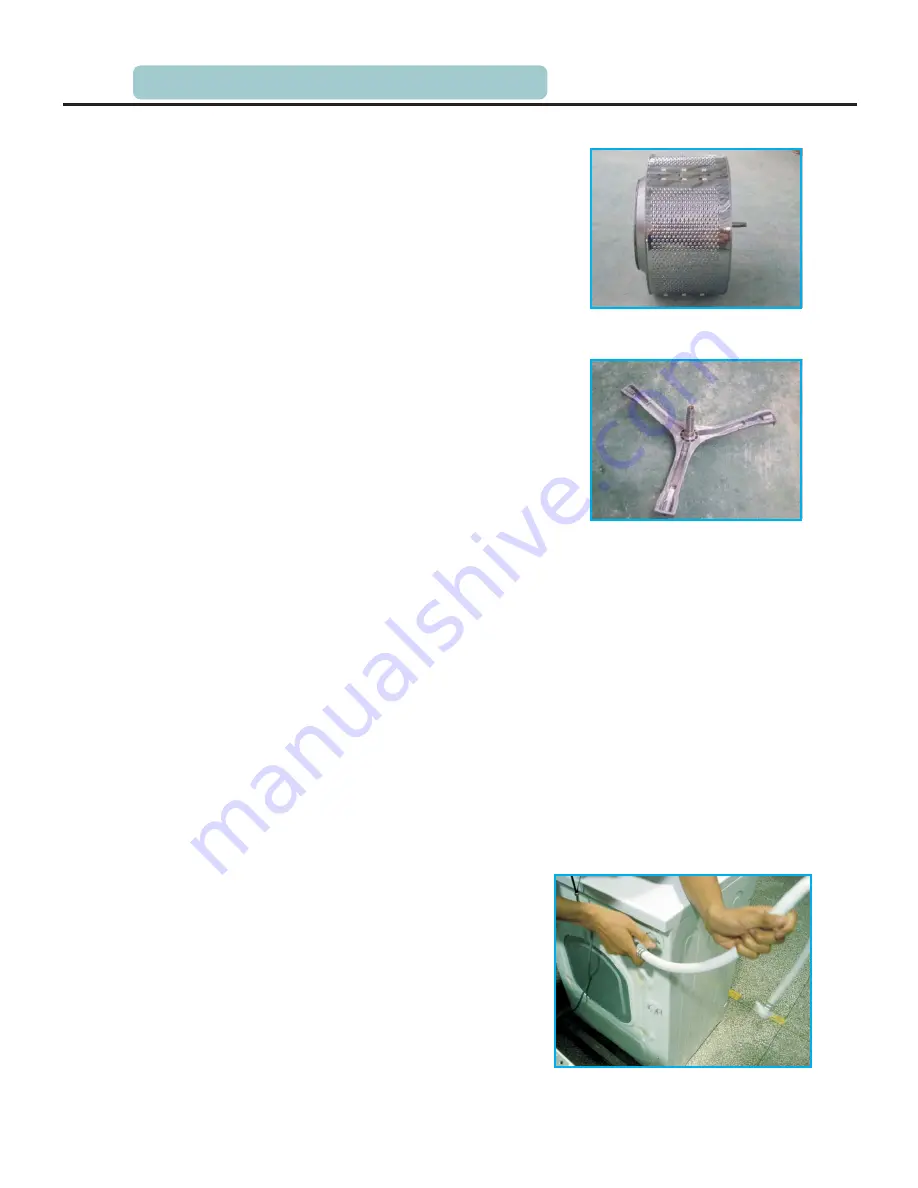
P.24
4.Overview of main parts
4.9.2 Drum kit
Drum kit consist of drum center, drum front, drum
back, lifter, spider kit (spider, shaft, shaft bush),
and spider bolt etc.
The structure and characteristic of drum:
Drum is made up of drum center using stainless
steel, drum front, drum back. As the class BA of
AISI 430 BA stainless steel, it is blighting.
After rolling the inside of drum front, the sharp
cutting edge rolled up to prevent scratching textiles
and arm during removing and adding textile.
The model shape repression of the meet between
drum back and spider enlarge the space putting
textile. The piercing and drawing reel ensure the
textile no injury during washing and spinning, and
the compact holes make sure the textile soak fully
in the drum.
Drum and drum front/back are connected by
advanced spinning curling process.
During the washing, three lifters hold up the clothes pressing against the affixed surface
of the drum. When clothes raised close to the top, centrifugal force is not enough to
overcome gravity, and therefore clothes fall and impinge washing liquid to improve
washing performance.
Spider kit
The spider is the aluminum die-casting. There is a bushing in the axis which is to reduce
the wear and tear of V-shaped edge of the oil seal. When installed bushings, the
powder-like debris produced by it cut shaft bushings should be removed, or they will
wear oil seal. To avoid wear and tear, grease should be applied the corresponding
position of the oil seal to ensure that it will play in the role of lubrication in the whole
life of washing machine and not dry or off. Spider kit is fastened on the drum with three
stainless steel bolts.
4.10 Inlet hose
Inlet hose connects household tap and washing
machine. The pipe of inlet hose has a high-pressure
capacity which nets the high strength polyester
fiber lines. Generally, household water pressure is
less than 1MPa, and practically the water pipes of
Midea washing machine could stand the pressure
of 2MPa in one minute not dehiscence, not
deformation, and bearing 4MPa pressure not burst.
As for inlet hose, there are many performance
requirements such as hot and cold alternate anti-shocking, anti-bending etc.
4.OVERVIEW OF MAIN COMPONENTS