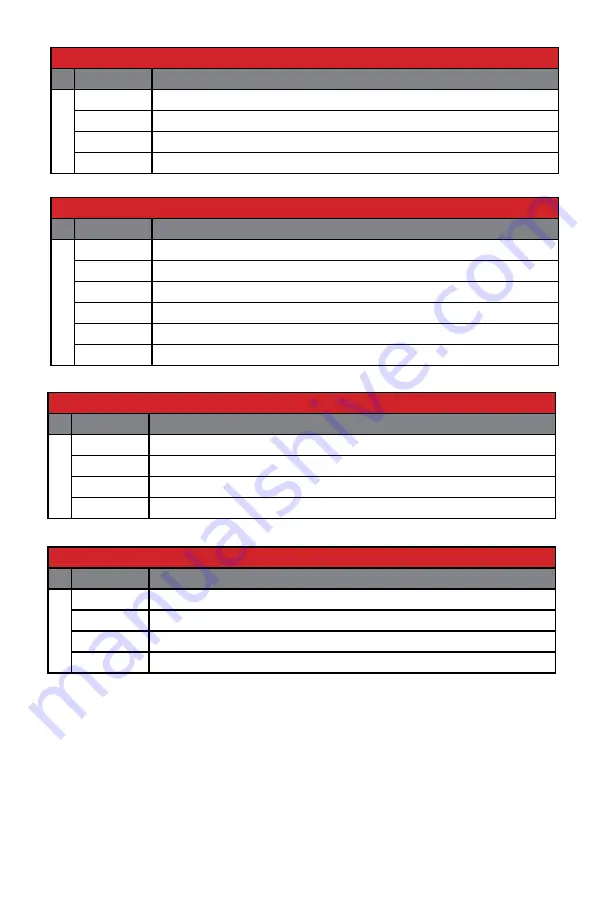
Migomag ACDC 200
Model No MOMACDC
39
Gas Lens Body
Stock Code
Description
H
45V24
Gas Lens Body 1.0mm Bore
45V25
Gas Lens Body 1.6mm Bore
45V26
Gas Lens Body 2.4mm Bore
45V27
Gas Lens Body 3.2mm Bore
Large Diameter Gas Lens Body
Stock Code
Description
K
45V116
Large Dia Gas Lens Body 1.6mm Bore
45V64
Large Dia Gas Lens Body 2.4mm Bore
45V63
Large Dia Gas Lens Body 4.0mm Bore
995795
Large Dia Gas Lens Body 3.2mm Bore
Lareg Diameter Gas Lens Cup
Stock Code
Description
L
57N75
Large Dia Gas Lens Cup 10mm Bore
57N74
Large Dia Gas Lens Cup 13mm Bore
57N88
Large Dia Gas Lens Cup 16mm Bore
57N87
Large Dia Gas Lens Cup 19mm Bore
Standard Gas Lens Cup
Stock Code
Description
I
54N18
Standard Gas Lens Cup 6mm Bore
54N17
Standard Gas Lens Cup 8mm Bore
54N16
Standard Gas Lens Cup 10mm Bore
54N15
Standard Gas Lens Cup 11mm Bore
54N14
Standard Gas Lens Cup 13mm Bore
54N19
Standard Gas Lens Cup 17mm Bore