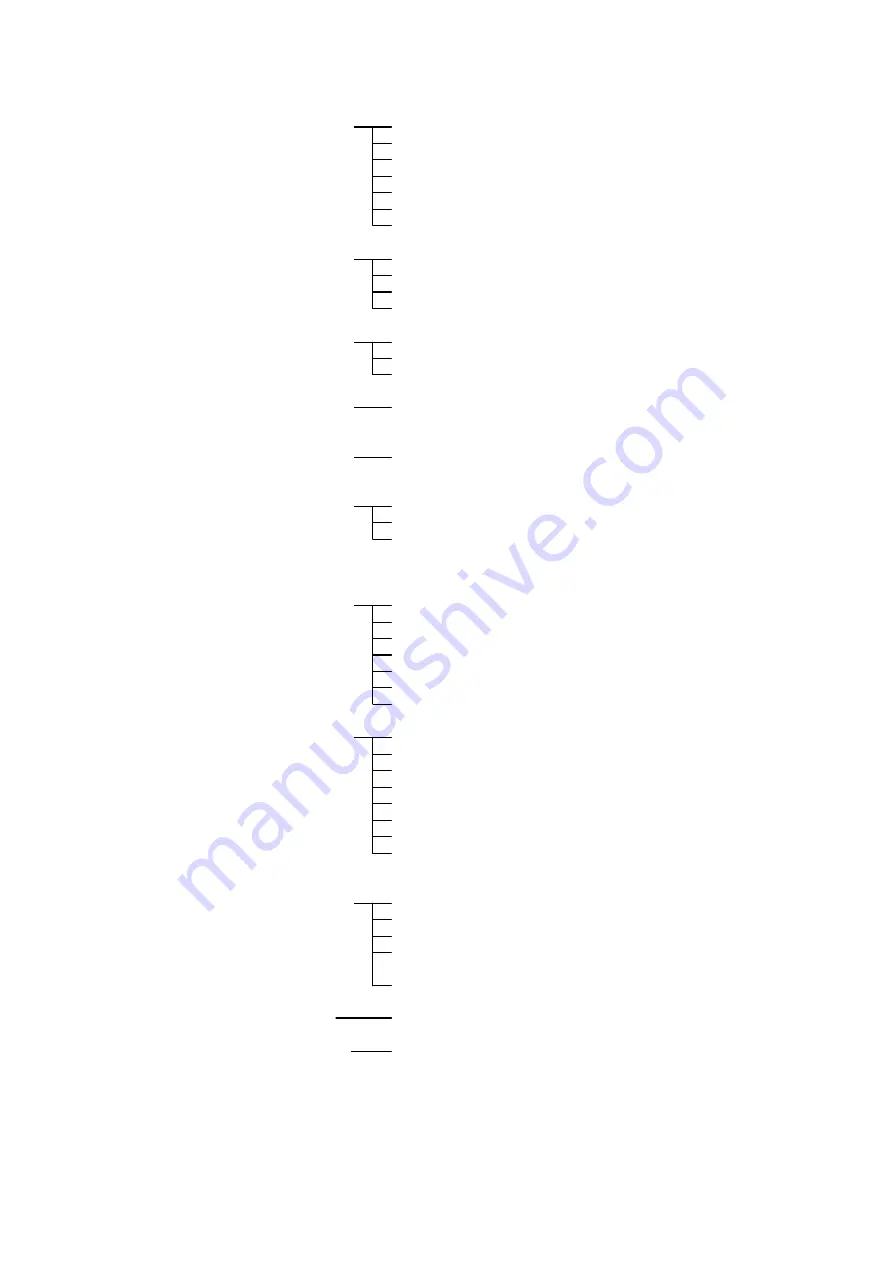
3. MACHINE ON THE WHOLE
28
Misfires accompanying white
smoke exhaust (unloaded):
Fuel consumption high (Dark
smoke exhaust.):
Sliding parts worn extremely or
piston stuck:
Engine stopped suddenly with
abnormal noise:
Lubrication oil diluted and
increases in volume:
Engine does not stop with fuel
supply discontinued (or over
runs):
Travel speed slow and vibration
weak:
Travels forward or reverse but
direction not selectable:
Does not travel forward nor
reverse:
Resistance of travel lever great.
Engine rpm does not rise
efficiently:
Piston, cylinder and ring worn.
Nozzle hole clogged.
Piston ring stuck.
Piston ring installed upside down.
Injection timing improper.
Valve open/close timing improper.
Injection pump joint loosened.
Leakage from fuel passage.
Air cleaner element clogged.
Defective fuel due to foreign matter entering.
Overloading.
Improper oil used.
Oil replacement neglected.
Air cleaner element broken or its cleaning neglected.
Piston and rod seizure and damage.
Injection pump plunger barrel worn.
Excessive oil.
Governor improperly assembled.
Injection pump rack disengaged.
Engine power output nsufficient or rpm setting improper for high
speed range.
Clutch slips.
V-belt slips.
Excessive oil in vibrator.
Internal defect in vibrator.
Aeration in traveling hydraulic oil.
Forward/reverse selector component defective.
Travel lever installation deficient.
Oil hose broken.
Aeration in oil of hydraulic system for traveling.
Improper oil level in hydraulic system (excessive or insufficient).
Selector valve clogged with dust.
Piston bearing broken in cylinder, leakage in USH packing, etc.
Connecting groove between gear pump input shaft and adapter
broken or worn.
V-belt disengaged or slipping.
Clutch slipping.
Vibrator locked.
Connecting groove between gear pump input shaft and adapter
broken or worn.
Piston bearing broken in cylinder, leakage in USH packing, etc.
Excessive oil in hydraulic system.
Isolation rubber damaged or failed.