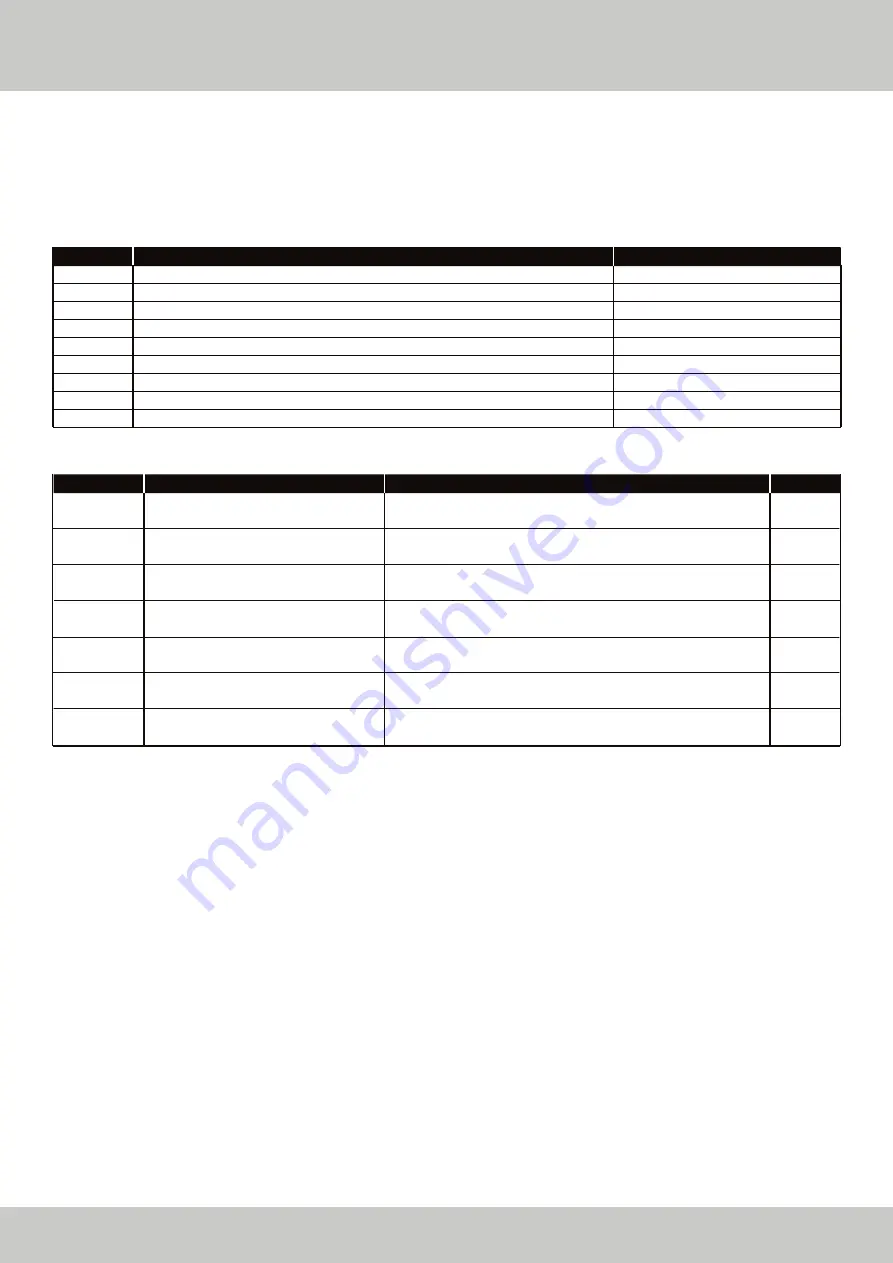
Software Version -the version of the software currently running
Operating Status -current operating state of the Extreme
TT1 Start Sensor (Tank) -current temperature in the tank
TT2 Stop Sensor -current temperature in the loading pipe
TT3 Loading Sensor -current temperature going in to the cylinder
TT4 Primary Sensor -current primary temperature at the cylinder
Boiler Output (Open Therm) -only used with Open Therm control
Loading Pump Percentage -current running of the pump
Fault Codes - the list of previous faults with most recent first
0 - 99
oF / nL / nR / hL / hR
0-99°C or -- if there is a fault
0-99°C or -- if there is a fault
0-99°C or -- if there is a fault
0-99°C or -- if there is a fault
0 - 99
0 - 99
See Below
▲
FIGURE 13.
DIAGNOSTIC MODE
SO
D0
D1
D2
D3
D4
D5
D6
E1-7
NUMBER
DIAGNOSIS
DISPLAYS
3
4
5
6
2
7
1
FAULT CODE
FAULT
ACTION
PRIORITY
01
02
03
04
05
06
07
TT1 Sensor Fault
TT2 Sensor Fault
TT3 Sensor Fault
TT4 Sensor Fault
Frost Protection Active
Anti-legionella Programme
Active for Longer than 2 Hours
Loading Programme Active for
Longer than 2 Hours
Check sensor connection at sensor and PCB.
Loading pump will run at normal speed using TT3.
Check sensor connection at sensor and PCB. Sensor
overridden by TT3, loading will continue.
Check sensor connection at sensor and PCB.
Loading process continues at 100%.
Check sensor connection at sensor and PCB.
Loading process begins after preset time.
Loading pump is controlled at a set speed, primary
demand outputs are activated.
Primary temperature has been insufficient for 2
hours, increase the temperature to required setting.
Primary temperature has been insufficient for 2
hours, increase the temperature to required setting.
▲
FIGURE 14.
FAULT CODES
OPERATION
TECHNICAL DOCUMENTATION
17
FAULT DIAGNOSIS
It is possible to interrogate the Rapide Extreme controller to determine sensor readings and fault history. To do
this you must press and hold the button on the controller until “SO” appears, this will put the controller in to
diagnosis mode, pressing the button again briefly will allow you to cycle through the sensor readings followed
by a fault history.
HIGH LIMIT PROTECTION
The Rapide Extreme utilies a manual reset high limit stat, in addition to the safety relief valves incorporated on
the unit and unvented kit if applicable. The stat will trip at a temperature of 85°C and will shut down the supply
to the two port valve. This prevents any further increase in water temperature from the primary water. To reset,
the cover of the stat must be removed and the reset button depressed, the cover can then be returned and
the unit will begin to operate again.