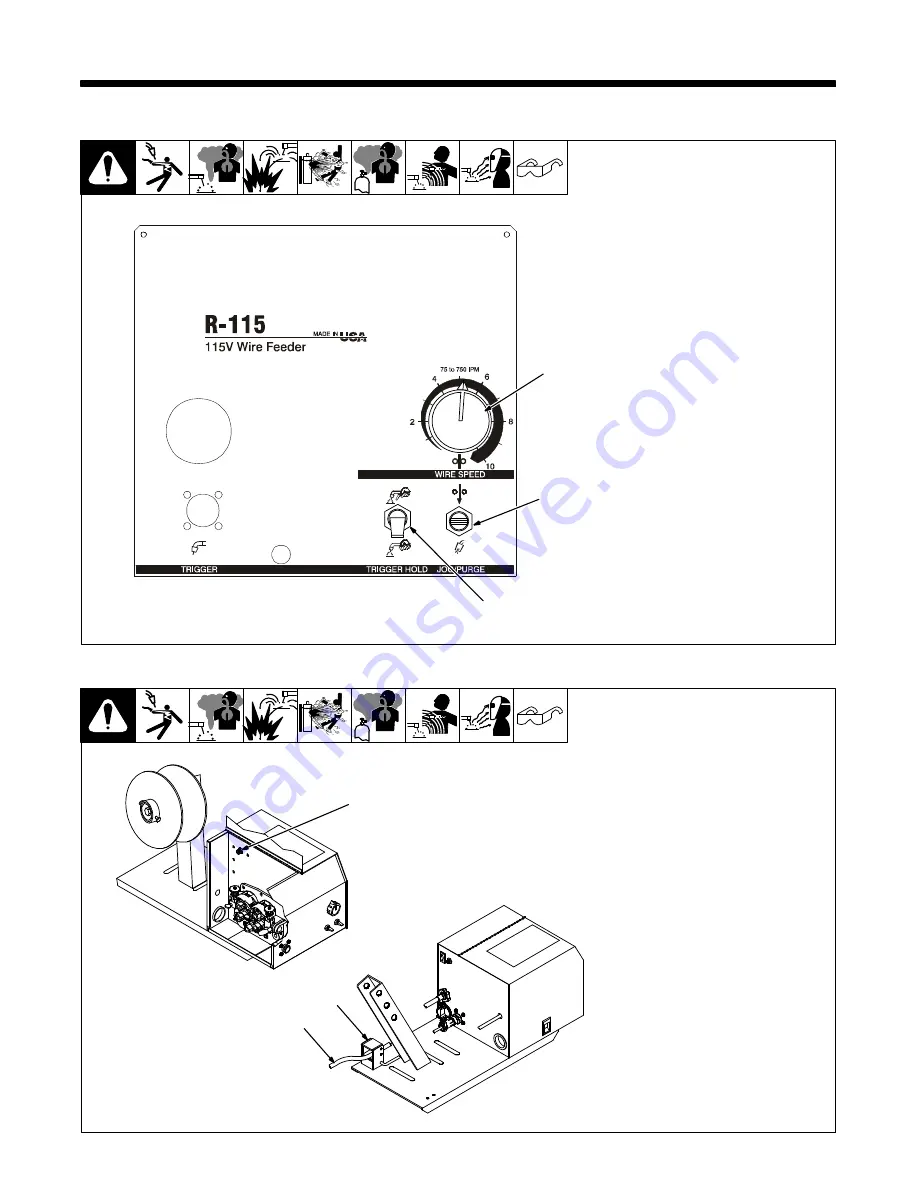
OM-193471 Page 24
SECTION 6 − OPERATION
6-1.
Front Panel Controls
1
Wire Speed Control
2
Jog/Purge Switch
Use Jog position to momentarily
feed welding wire at speed set on
Wire Speed control without
energizing welding circuit or
shielding gas valve.
Use Purge position to momentarily
energize gas valve to purge air from
gun or adjust gas regulator.
3
Trigger Hold Switch
Push up to weld without holding gun
trigger throughout the weld cycle.
To start weld cycle, press and
release gun trigger within three
seconds after an arc has been
struck. To end weld, press and
release gun trigger.
Power switch is on rear panel (see
Section 5-3)
192 510-B
1
2
3
6-2.
Optional Side Panel Controls
Ref. 802 310-B / Ref. 802 309-B
1
Optional Run-In Speed
Control
The Run-In Speed Control provides
a means of selecting the rate at
which welding wire will feed after
preflow and before arc initiation.
After arc initiation, the wire feed
speed is governed by the Wire
Speed Control. Rotating the Run-In
Speed Control clockwise will
increase run-in wire feed speed.
Close side door.
2
Reed Relay Switch
3
Weld Cable
Weld cable must be routed through
reed relay switch present on units
with Run-In Speed Control option.
1
2
3