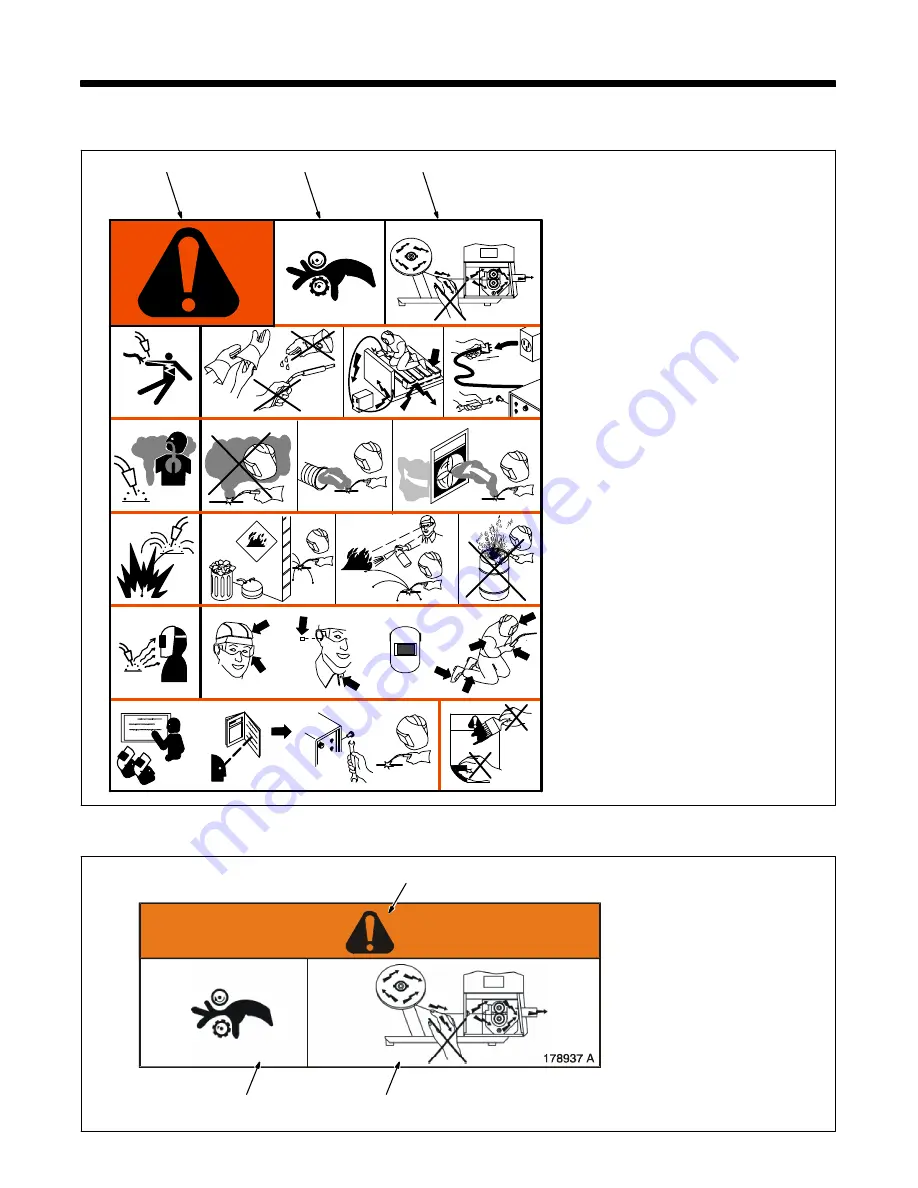
OM-216 655 Page 5
SECTION 2 − DEFINITIONS
1
1.1
1.2
1.3
3
3.1
3.2
3.3
4
4.1
+
2
2.1
2.2
+
+
5
6
+
2.3
S-178 936
A. Warning! Watch Out! There are possible
hazards as shown by the symbols.
B. Drive rolls can injure fingers.
C. Welding wire and drive parts are at
welding voltage during operation − keep
hands and metal objects clear.
1
Electric shock can kill.
1.1 Wear dry insulating gloves. Do not touch
electrode with bare hand. Do not wear
wet or damaged gloves.
1.2 Protect yourself from electric shock by
insulating yourself from work and ground.
1.3 Disconnect input plug or power before
working on machine.
2
Breathing welding fumes can be
hazardous to your health.
2.1 Keep your head out of the fumes.
2.2 Use forced ventilation or local exhaust to
remove the fumes.
2.3 Use ventilating fan to remove fumes.
3
Welding sparks can cause explosion or
fire.
3.1 Keep flammables away from welding.
Don’t weld near flammables.
3.2 Welding sparks can cause fires. Have a
fire extinguisher nearby and have a
watch person ready to use it.
3.3 Do not weld on drums or any closed
containers.
4
Arc rays can burn eyes and injure skin.
4.1 Wear hat and safety glasses. Use ear
protection and button shirt collar. Use
welding helmet with correct shade of
filter. Wear complete body protection.
5
Become trained and read the instructions
before working on the machine or
welding.
6
Do not remove or paint over (cover) the
label.
2-1.
Warning Label Definitions
A
B
C
2-2.
Electric Shock And Pinch Hazard
1
Warning! Watch Out! There
are possible hazards as
shown by the symbols.
2
Drive rolls can injure fingers
3
Welding wire and drive parts
are at welding voltage during
operation − keep hands and
metal objects away.
1
2
3
Summary of Contents for ST 44 Series Wire Feeder
Page 19: ...OM 216 655 Page 15 SECTION 6 ELECTRICAL DIAGRAM 956 142 484 ...
Page 24: ...Notes ...
Page 25: ...Notes ...
Page 26: ...Notes ...