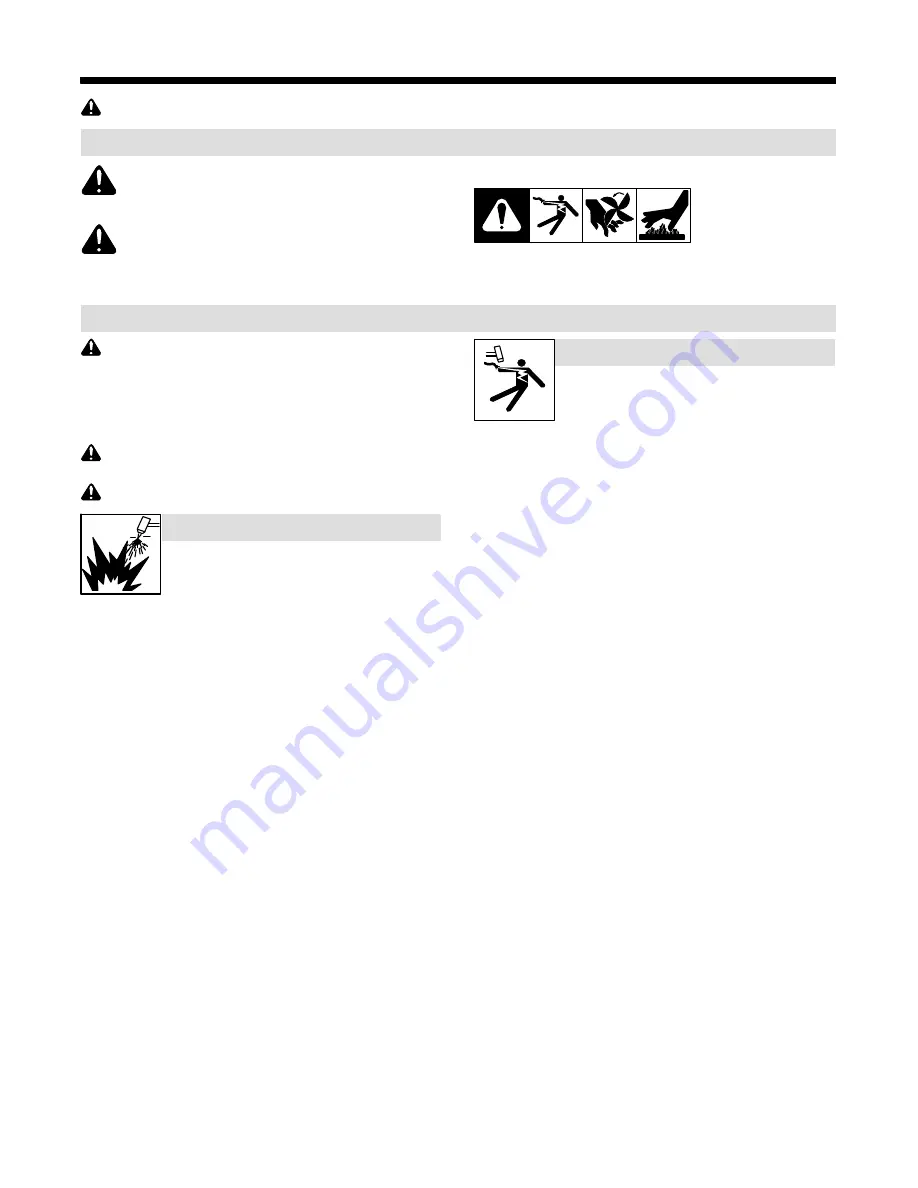
OM-264 267 Page 1
SECTION 1
−
SAFETY PRECAUTIONS - READ BEFORE USING
pom_2013
−
09
Protect yourself and others from injury —
read, follow, and save these important safety precautions and operating instructions.
1-1. Symbol Usage
DANGER!
−
Indicates a hazardous situation which, if
not avoided, will result in death or serious injury. The
possible hazards are shown in the adjoining symbols
or explained in the text.
Indicates a hazardous situation which, if not avoided,
could result in death or serious injury. The possible
hazards are shown in the adjoining symbols or ex-
plained in the text.
NOTICE
−
Indicates statements not related to personal injury.
.
Indicates special instructions.
This group of symbols means Warning! Watch Out! ELECTRIC
SHOCK, MOVING PARTS, and HOT PARTS hazards. Consult sym-
bols and related instructions below for necessary actions to avoid the
hazards.
1-2. Plasma Arc Cutting Hazards
The symbols shown below are used throughout this manual
to call attention to and identify possible hazards. When you
see the symbol, watch out, and follow the related instructions
to avoid the hazard. The safety information given below is
only a summary of the more complete safety information
found in the Safety Standards listed in Section 1-5. Read and
follow all Safety Standards.
Only qualified persons should install, operate, maintain, and
repair this unit.
During operation, keep everybody, especially children, away.
Hot metal and sparks blow out from the cutting arc.
The flying sparks and hot metal, hot workpiece, and
hot equipment can cause fires and burns. Check
and be sure the area is safe before doing any cutting.
CUTTING can cause fire or explosion.
D
Remove all flammables within 35 ft (10.7 m) of the cutting arc. If this
is not possible, tightly cover them with approved covers.
D
Do not cut where flying sparks can strike flammable material.
D
Protect yourself and others from flying sparks and hot metal.
D
Be alert that sparks and hot materials from cutting can easily go
through small cracks and openings to adjacent areas.
D
Watch for fire, and keep a fire extinguisher nearby.
D
Be aware that cutting on a ceiling, floor, bulkhead, or partition can
cause fire on the hidden side.
D
Do not cut on containers that have held combustibles, or on closed
containers such as tanks, drums, or pipes unless they are properly
prepared according to AWS F4.1 and AWS A6.0 (see Safety Stan-
dards).
D
Connect work cable to the work as close to the cutting area as prac-
tical to prevent cutting current from traveling long, possibly unknown
paths and causing electric shock, sparks, and fire hazards.
D
Do not use plasma cutter to thaw frozen pipes.
D
Never cut containers with potentially flammable materials inside
−
they must be emptied and properly cleaned first.
D
Do not cut where the atmosphere may contain flammable dust, gas,
or liquid vapors (such as gasoline).
D
Do not cut pressurized cylinders, pipes, or vessels.
D
Wear body protection made from durable, flame
−
resistant material
(leather, heavy cotton, wool). Body protection includes oil-free
clothing such as leather gloves, heavy shirt, cuffless trousers, high
shoes, and a cap.
D
Do not locate unit on or over combustible surfaces.
D
Remove any combustibles, such as a butane lighter or matches,
from your person before doing any cutting.
D
After completion of work, inspect area to ensure it is free of sparks,
glowing embers, and flames.
D
Use only correct fuses or circuit breakers. Do not oversize or by-
pass them.
D
Follow requirements in OSHA 1910.252 (a) (2) (iv) and NFPA 51B
for hot work and have a fire watcher and extinguisher nearby.
Touching live electrical parts can cause fatal shocks
or severe burns. The torch and work circuit are
electrically live whenever the output is on. The input
power circuit and machine internal circuits are also
live when power is on. Plasma arc cutting requires
higher voltages than welding to start and maintain the arc (200 to 400
volts dc are common), but may also use torches designed with safety
interlock systems which turn off the machine when the shield cup is
loosened or if tip touches electrode inside the nozzle. Incorrectly
installed or improperly grounded equipment is a hazard.
ELECTRIC SHOCK can kill.
D
Do not touch live electrical parts.
D
Wear dry, hole-free insulating gloves and body protection.
D
Insulate yourself from work and ground using dry insulating mats or
covers big enough to prevent any physical contact with the work or
ground.
D
Do not touch torch parts if in contact with the work or ground.
D
Turn off power before checking, cleaning, or changing torch parts.
D
Disconnect input power before installing or servicing this equip-
ment. Lockout/tagout input power according to OSHA CFR
1910.147 (see Safety Standards).
D
Properly install, ground, and operate this equipment according to its
Owner’s Manual and national, state, and local codes.
D
Check and be sure that input power cord ground wire is properly
connected to ground terminal in disconnect box or that cord plug is
connected to a properly grounded receptacle outlet
−
always verify
the supply ground.
D
When making input connections, attach proper grounding conduc-
tor first.
D
Keep cords dry, free of oil and grease, and protected from hot metal
and sparks.
D
Frequently inspect input power cord and ground conductor for dam-
age or bare wiring – replace immediately if damaged – bare wiring
can kill.
D
Turn off all equipment when not in use.
D
Do not use worn, damaged, undersized, or repaired cables.
D
Do not wrap torch cable around your body.
D
Ground the workpiece to a good electrical (earth) ground if required
by codes.
D
Use only well-maintained equipment. Repair or replace damaged
parts at once.
D
Wear a safety harness if working above floor level.
D
Keep all panels and covers securely in place.
D
Do not bypass or try to defeat the safety interlock systems.
D
Use only torch(es) specified in Owner’s Manual.
D
Keep away from torch tip and pilot arc when trigger is pressed.
D
Clamp work cable with good metal-to-metal contact to workpiece
(not piece that will fall away) or worktable as near the cut as
practical.
D
Insulate work clamp when not connected to workpiece to prevent
contact with any metal object.