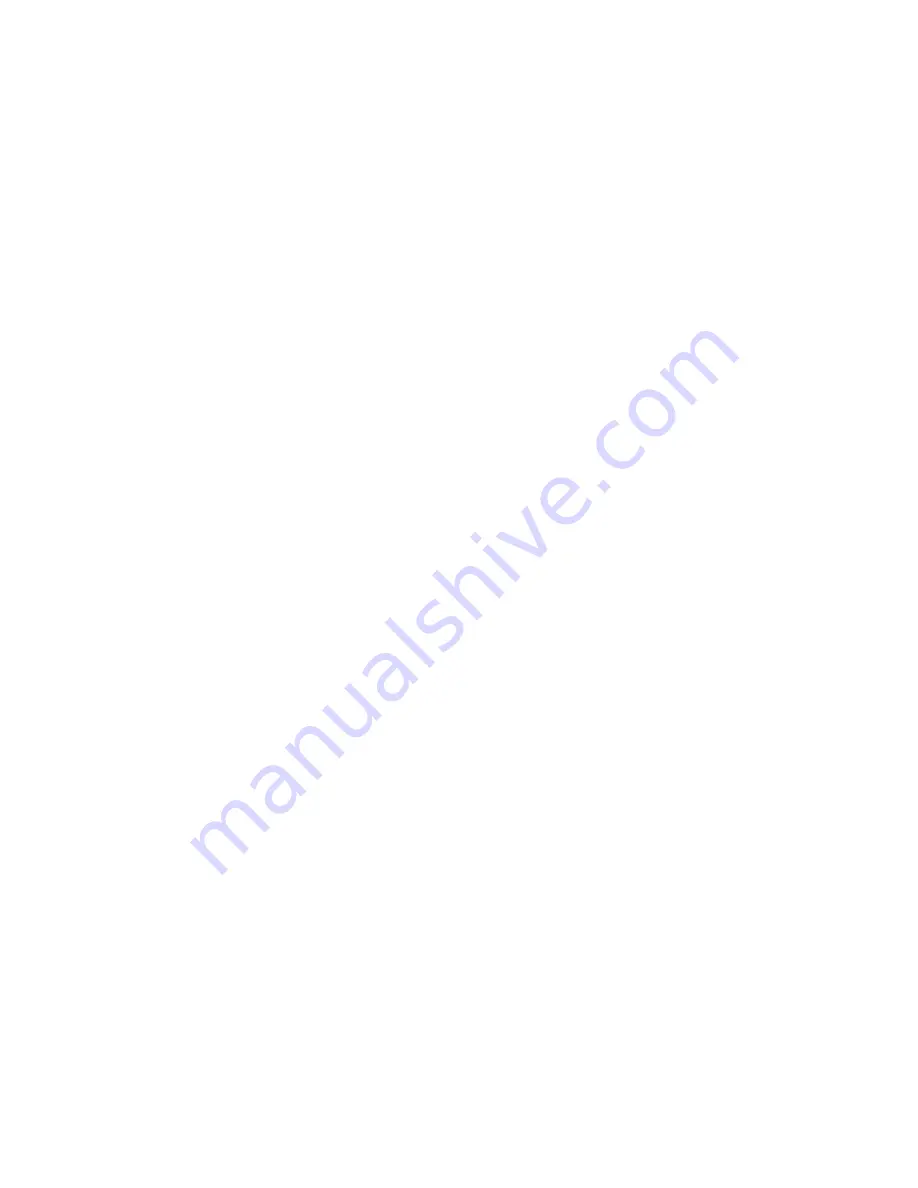
36
Test the Emergency Stop Circuit
Having
followed the steps outlined above for resetting the machine and starting
the spindle, then
Press the red EMERGENCY STOP button.
Spindle rotation should stop. The emergency stop button is the most important
safety switch on the machine. It stops and then de-energizes the spindle motor.
(At the same time, it stops and de-energizes the axis servo motors, although they
are not running for this test.)
When the red emergency stop button is pushed, the spindle should brake to a
rapid stop. If the spindle does not stop at all, or if it coasts to a stop, then the
emergency stop circuit is not operating correctly. Call qualified service personnel
to fix the problem. The machine should not be operated until the emergency stop
circuit is operating correctly.
Repeat the same tests using all emergency stop buttons including conveyor,
remote hand controller, etc.
Test the enclosure safety circuit
If the machine is still in emergency stop mode from the previous test, then twist the red
EMERGENCY STOP button clockwise to release it. Press the ENABLE button to re-
energize the axis motors and the spindle motor. Follow the directions in the previous
sequence for starting the spindle for manual use.
Now hold in the SETUP button and open the door to the machining enclosure (if
equipped). The spindle should brake to a rapid stop. If the spindle does not stop at all,
or if it coasts to a stop, then the enclosure safety circuit is not operating correctly. Call
qualified service personnel (as described in chapter 1) to fix the problem. The machine
should not be operated until the enclosure safety circuit is operating correctly.
Summary of Contents for ML Series
Page 2: ......
Page 4: ......
Page 6: ......
Page 20: ......
Page 23: ...CHAPTER 2 SPECIFICATION ML14 26 Series Machine Layout 17 ...
Page 24: ...ML35 40 Series Machine Layouts ML35 Series ML40 Series 18 ...
Page 33: ...CHAPTER 3 SITE PREPARATION 27 ML22 ML26 Lifting device drawing ...
Page 34: ......
Page 74: ......
Page 76: ......
Page 78: ......
Page 80: ......
Page 82: ......
Page 83: ......