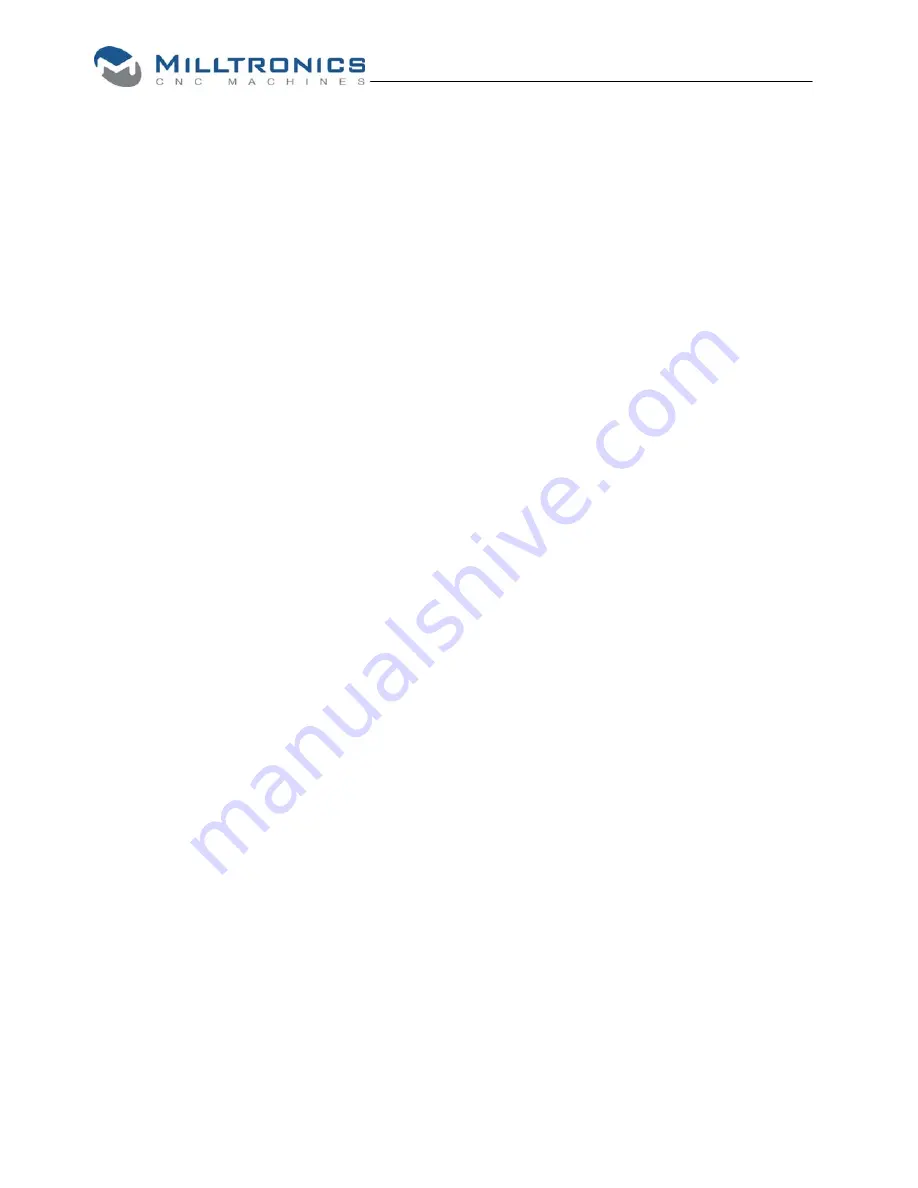
C
HAPTER
7 – 7200 CNC O
PERATION
C-Axis and Live Tooling Operation (option)
Spindle Selection Commands G24, G25
o
G24 - Select main spindle
o
G25 - Select live tooling spindle
After power up, a spindle must be selected before executing any other spindle
commands. Use G24 or a G25 in MDI or via a program to select a spindle.
When in G24 mode the feed-rate override, front panel buttons, spindle M-codes,
program spindle speeds, spindle feed back etc. refer to the main spindle. The gear
range is displayed on the status window.
When in G25 mode the feed-rate override, front panel buttons, spindle M-codes,
program spindle speeds, spindle feed back etc. refer to the live tooling spindle.
There is only one gear on the live tooling spindle, and while G25 is active the gear
range is displayed as gear 8 on the status window.
C-Axis
The C-axis can be homed, jogged and hand-wheeled. You must use the remote hand-
wheel to move the C-axis in handwheel mode. C-axis moves always go the shortest
distance around.
Although it is possible to run both spindles at the same time, normally there is no
application that would use this feature. However there are times during index
operations that that both spindles are required to run at the same time.
When indexing tools the live tooling spindle runs at ~300rpm.
Example:
G24 (main spindle)
M42 (gear 2)
G96 S200 (constant surface speed)
G50 S2000
M3 (turn on the main spindle)
T0404 M6 (index to tool 4)
After tool 4 is active the main spindle will still be active, will still be in G96, and will
be in gear 2.
With live tooling running, the main spindle may need to position to an angle.
Example:
G25 (live tooling spindle)
G97 S2000 (rpm mode)
M3 (turn on the live tooling spindle)
C270 (move the main spindle to 270 degrees)
After C moves to 270 degrees the live tool will still be active.
57
Summary of Contents for ML Series
Page 2: ......
Page 4: ......
Page 6: ......
Page 20: ......
Page 23: ...CHAPTER 2 SPECIFICATION ML14 26 Series Machine Layout 17 ...
Page 24: ...ML35 40 Series Machine Layouts ML35 Series ML40 Series 18 ...
Page 33: ...CHAPTER 3 SITE PREPARATION 27 ML22 ML26 Lifting device drawing ...
Page 34: ......
Page 74: ......
Page 76: ......
Page 78: ......
Page 80: ......
Page 82: ......
Page 83: ......