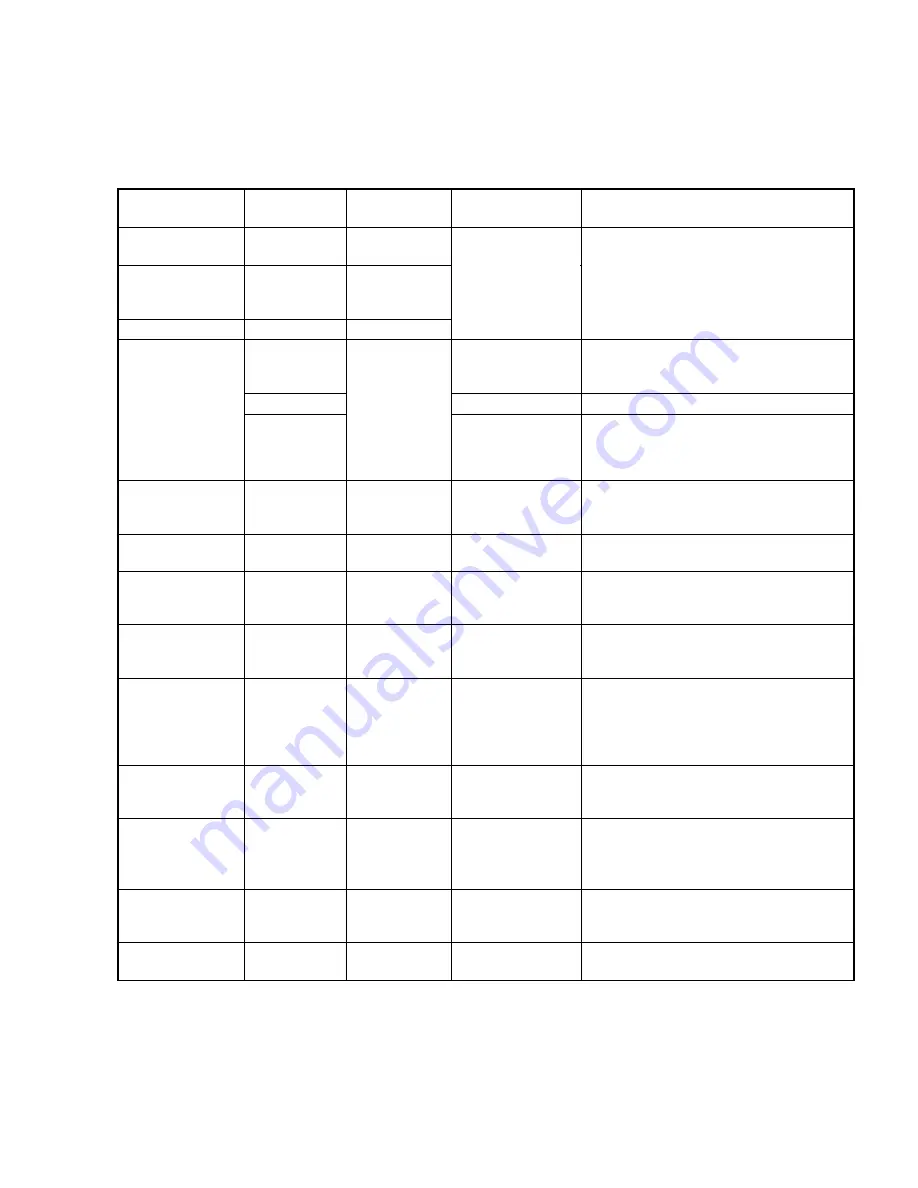
Chapter 3. Routine Maintenance
PELLERIN MILNOR CORPORATION
3.1.3.
How to Remove Contamination
Table 9: Contamination Types, Cleaning Agents, and Procedures
Material or
Component
Usual
Contamination
Example
Cleaning Agent
More Data
machine housing
dust, dirt
—
compressed air or
shop vacuum
Air—no more than 30 psi (207 kpa). Do not
push dust in mechanisms.
fins and vents on
electrical
components
dust
motors, inverters,
braking resistors
electric box interior
dust
all electric boxes
shop vacuum, soft
bristle brush, canned
air for electrical
components
Do not push dust in mechanisms.
electrical
connections
corrosion,
varnish
spade connector,
molex connector,
plug-in relay
spray solvent for
electrical components
Disconnect then connect it again. Use solvent if
the bad connection continues.
dust
none
Use a clean, soft, dry cloth.
electronic sensors
dirt
photoeye lens,
reflector, laser,
proximity switch,
temperature
probe
warm water with
soap, then water flush
Use clean, soft cloths.
stainless steel
chemical spill
shell, supply
injector
water
Use a hose to flush the chemical supply from the
surface fully. Do not get water on electrical
components or mechanisms.
300 series stainless
steel
chemical
corrosive attack
shell interior,
cylinder
pickling and
passivation
Speak to your dealer or Milnor.This is not
routine maintenance.
painted metal,
unpainted aluminum
dust, dirt, grease
frame members
warm water with
soap, then water to
flush
Use clean cloths. Do not get water in electrical
components.
rubber
dirt, oil, grease
drive belts, hoses
warm water with
soap, then water to
flush
Use clean cloths. Flush fully. Oil or soap must
not stay on drive belts. Make sure that drive
belts are serviceable.
clear plastic, acrylic
discoloration
(yellowing)
compressed air
filter bowl, visual
flow meter
warm water with
soap, then water to
flush, then acrylic
cleaner. Do not use
ammonia.
Use only the necessary cleaning agents. Wash
and rinse with clean, soft cloths. Follow
instructions on acrylic cleaner.
glass
discoloration
(yellowing)
door glass, site
glass
ammonia and water
solution and water
rinse then acetone
Use clean, soft cloths. Use only the necessary
cleaning agents. If necessary, soak in cleaner.
soft air filter, lint
filter,
dust, lint
on inverter
electric box door,
in air line filter
bowl, in dryers
shop vacuum
Replace the used with a new filter when the
vacuum cannot remove contamination.
rigid strainers,
screens for water,
steam
mineral particles
in water line,
y-strainer
water
Use a rigid bristle brush. Flush with a flow of
water.
rigid strainers,
screens for oil
metal shavings
in hydraulic line
carburetor cleaner or
equivalent solvent
Soak. Use a rigid bristle brush.
3.1.4.
Lubricant Identification and Procedures
Table 10
identifies the lubricant for each lubricant code given in the maintenance summary. Get
these or equivalent lubricants from from your local lubricant supplier.
24
Summary of Contents for 30022V8Z
Page 2: ......
Page 4: ......
Page 5: ...English 1 1 ...
Page 6: ......
Page 37: ...Türk 2 33 ...
Page 38: ......
Page 68: ......
Page 69: ...Español 3 65 ...
Page 70: ......
Page 101: ...Français 4 97 ...
Page 102: ......
Page 136: ......
Page 137: ...Dansk 5 133 ...
Page 138: ......
Page 169: ...Deutsch 6 165 ...
Page 170: ......