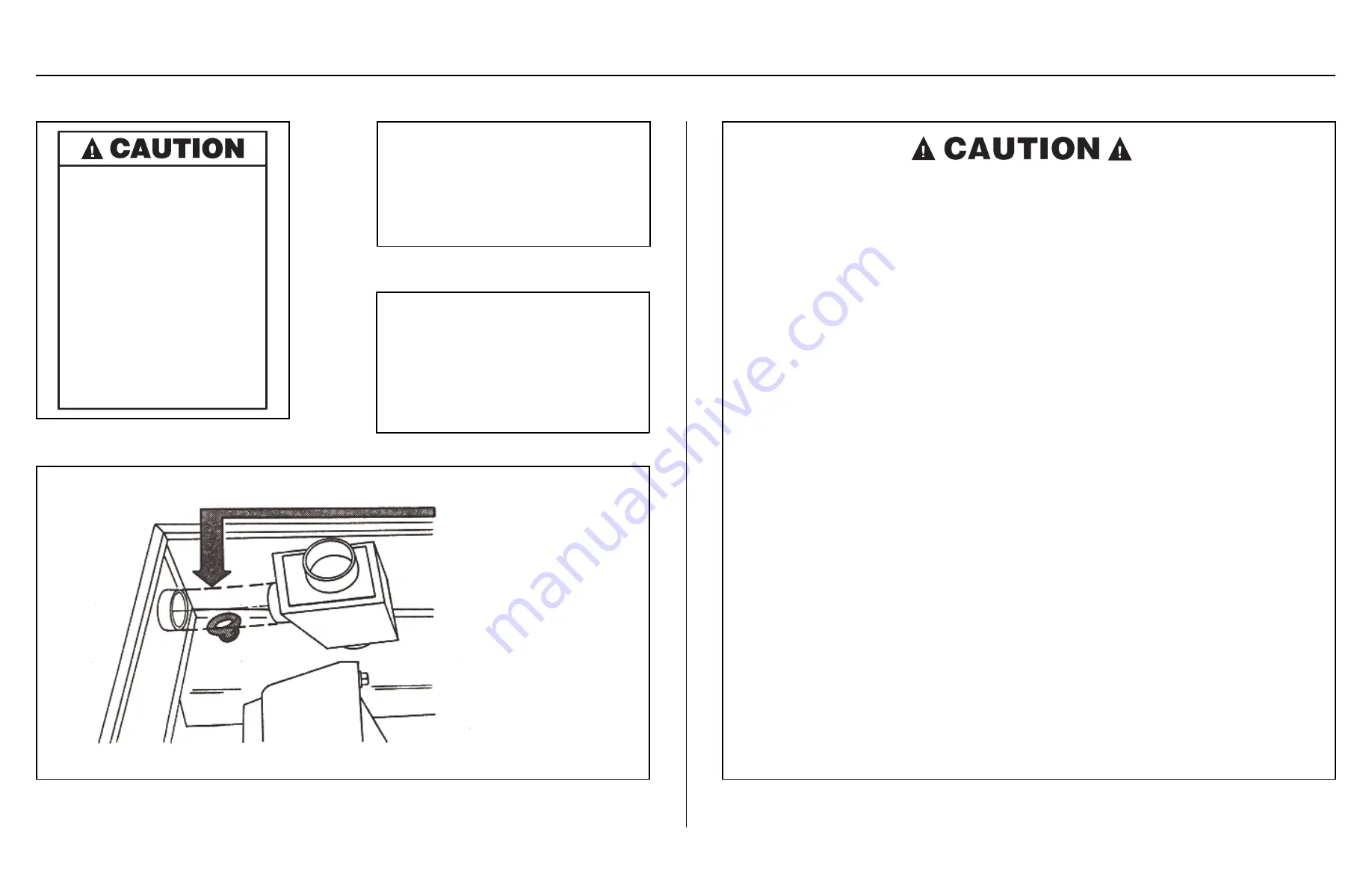
USE ONLY YOUR
FINGERS TO DEPRESS
THE KEYS.
NEVER USE SHARP
OBJECTS.
WHEN USED PROPERLY
THIS KEYPAD WILL
WITHSTAND HEAVY
INDUSTRIAL USE.
DAMAGE MAY OCCUR IF
KEYS ARE DEPRESSED
BY A SCREWDRIVER,
PEN, ETC.
Î
FIGURE 14
(MSIN0201BE)
Î
All Machines
WARNING
DO
NOT
TAMPER
WITH
INDIVIDUAL
CONNECTIONS
ON
THIS
"WIRE-WRAPPED" CONTROLLER, OTHERWISE THE WIRE WRAPS MAY BE
LOOSENED WHEREUPON ELECTRICAL CONTINUITY COULD BECOME
INTERMITTENT CAUSING THE CONTROL TO MALFUNCTION.
DO NOT MODIFY ANY OF THESE CIRCUITS.
DO NOT CUT OR ADD ANY WIRES IN THIS SYSTEM. TAMPERING WITH THIS
WIRING WITHOUT WRITTEN PRIOR PERMISSION WILL VOID THE WARRANTY.
REQUEST INSTRUCTIONS FROM THE FACTORY SHOULD IT BE DESIRED TO
MODIFY ANY OF THE CIRCUITS.
Î
FIGURE 15
(MSIN0201BE)
Î
All Machines
AIR CONNECTION
MINIMUM 85 PSI (Generally)
MAXIMUM 110 PSI (Check nameplate on machine)
THE BRAKE INTERLOCK PRESSURE SWITCH WILL NOT PERMIT THE
MACHINE TO EXTRACT IF THE AIR PRESSURE IS TOO LOW. THE
MACHINE WILL ROTATE AT DRAIN SPEED INSTEAD.
If this happens, check your air compressor. If your gauge shows more than
85 PSI the gauge is probably faulty. Some air compressors are set with
too great a pressure differential between the lowest pressure obtainable
and the highest pressure obtainable. Hence, if your compressor is set to
go on at 60 PSI and off at 110 PSI, the machine will extract quite
satisfactorily whenever the air pressure is above 85 PSI, but will not enter
extraction at all when the pressure is below 85 PSI.
Î
FIGURE 16
(MSIN0201BE)
Î
All Machines
THIS HOSE FROM THE
STAPH AIRTROL
ASSEMBLY TO THE
CLEAN SIDE VENT
SCREEN WAS
REMOVED FOR
SHIPPING PURPOSES
TO PERMIT
ATTACHMENT OF
LOADING SLING TO
SHIPPING EYE BOLT.
REINSTALL AS SHOWN
BEFORE OPERATING
MACHINE.
Î
FIGURE 17
(MSIN0201BE)
Î
Staph-Guard
®
Machines
WHEN MAKING ELECTRICAL
POWER CONNECTIONS:
BEFORE SHIPPING, ALL MOTORS ARE PROPERLY PHASED FOR
CORRECT
ROTATION.
IT
IS
POSSIBLE
TO
REVERSE
THE
DIRECTION
OF
ROTATION
IN
A
3
PHASE
MACHINE
BY
INTERCHANGING THE INCOMING POWER LEADS. THEREFORE, THE
ROTATION OF A 3 PHASE MACHINE MUST BE OBSERVED AND
CORRECTED WHEN THE MACHINE IS FIRST INSTALLED. IF IT IS
NECESSARY TO REVERSE THE ROTATION, SIMPLY SWAP THE
INCOMING POWER LINES TO THE MACHINE (NEVER MOVE L3 IF L3
IS A STINGER LEG) - NEVER ATTEMPT TO RECONNECT MOTORS
OR THE MOTOR CONTROL DEVICES.
NOTE:
1. Connections must be made by a competent electrician.
2. Before making power connections, read the instructions
on all related tags.
3. "Stinger leg", if any, must be connected to terminal L3 only.
4. Only use Bussman Fusetron FRN (up to 250V), FRS (up to
600V) or similar lag fuses. The nameplate fuse sizes must
not be applied to standard fuses.
5. See nameplate for fuse and wire size. If wire runs more than
50 feet, increase by one wire size per each additional 50 feet.
Î
FIGURE 18
(MSIN0201BE)
Î
All Hydro-Cushion
®
Machines
43
Summary of Contents for 42044SR2
Page 2: ......
Page 4: ......
Page 8: ......
Page 9: ...Installation 1 5 ...
Page 37: ...Î FIGURE 8 MSIN0301AE Î Vibration Switch Î FIGURE 9 MSIN0301AE Î 60 Staph Guard 33 ...
Page 51: ...586DA4 BUecU CicdU CSXU QdYS B5EC5 D1 9 CD1 1D9 1 4 5B1D9 C9 1 15 1F _V 47 ...
Page 53: ...Dimensional Drawings 2 49 ...
Page 54: ......
Page 55: ...51 ...
Page 56: ...52 ...
Page 57: ...53 ...
Page 58: ...54 ...
Page 59: ...55 ...
Page 60: ...56 ...
Page 61: ...57 ...
Page 62: ...58 ...
Page 63: ...59 ...
Page 64: ......
Page 65: ...61 ...
Page 66: ...62 ...
Page 67: ...63 ...
Page 68: ...64 ...