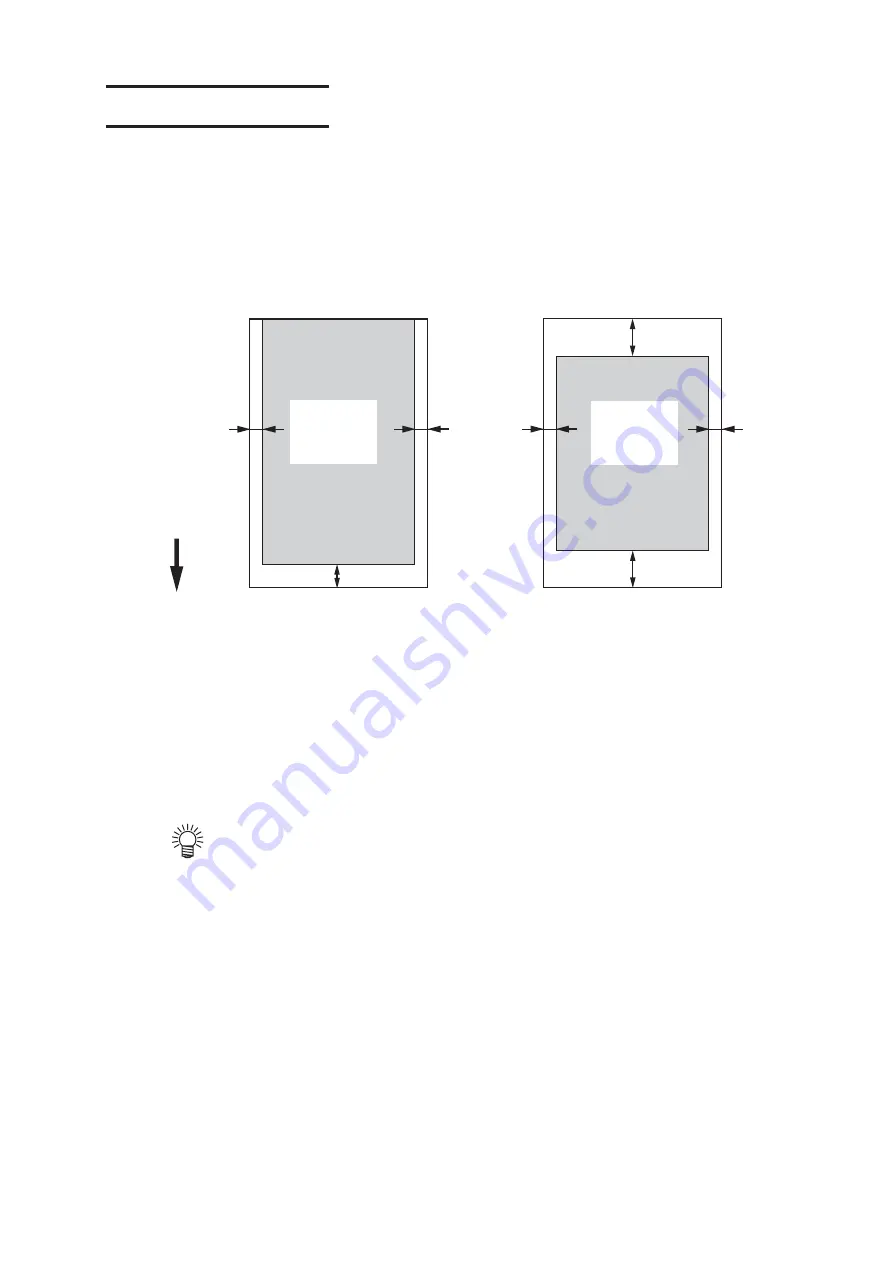
- 4.12 -
Effective Plotting Area
The device has an area which cannot perform printing, due to mechanical reasons.
This area is called “ dead space”.
0 mm
Roll
medium
110 mm
15 mm 15 mm
15 mm
15 mm
Cut sheet
medium
Medium
feeding
direction
25 mm
65 mm
Effective
printing
area
Effective
printing
area
Changing the effective printing area...
Initial value of dead space for right and left of medium is 15 m each.
The effective plotting area can be changed by changing the dead space.
Dead space is set with [Margin] in FUNCTION mode.
Summary of Contents for JV3 S SERIES
Page 2: ......
Page 62: ... 2 30 ...
Page 84: ... 4 14 ...
Page 108: ... 5 24 ...
Page 118: ... 6 10 ...
Page 124: ... A 6 ...
Page 129: ......
Page 130: ...PrintedinJapan MIMAKI ENGINEERING Co Ltd 2004 ...