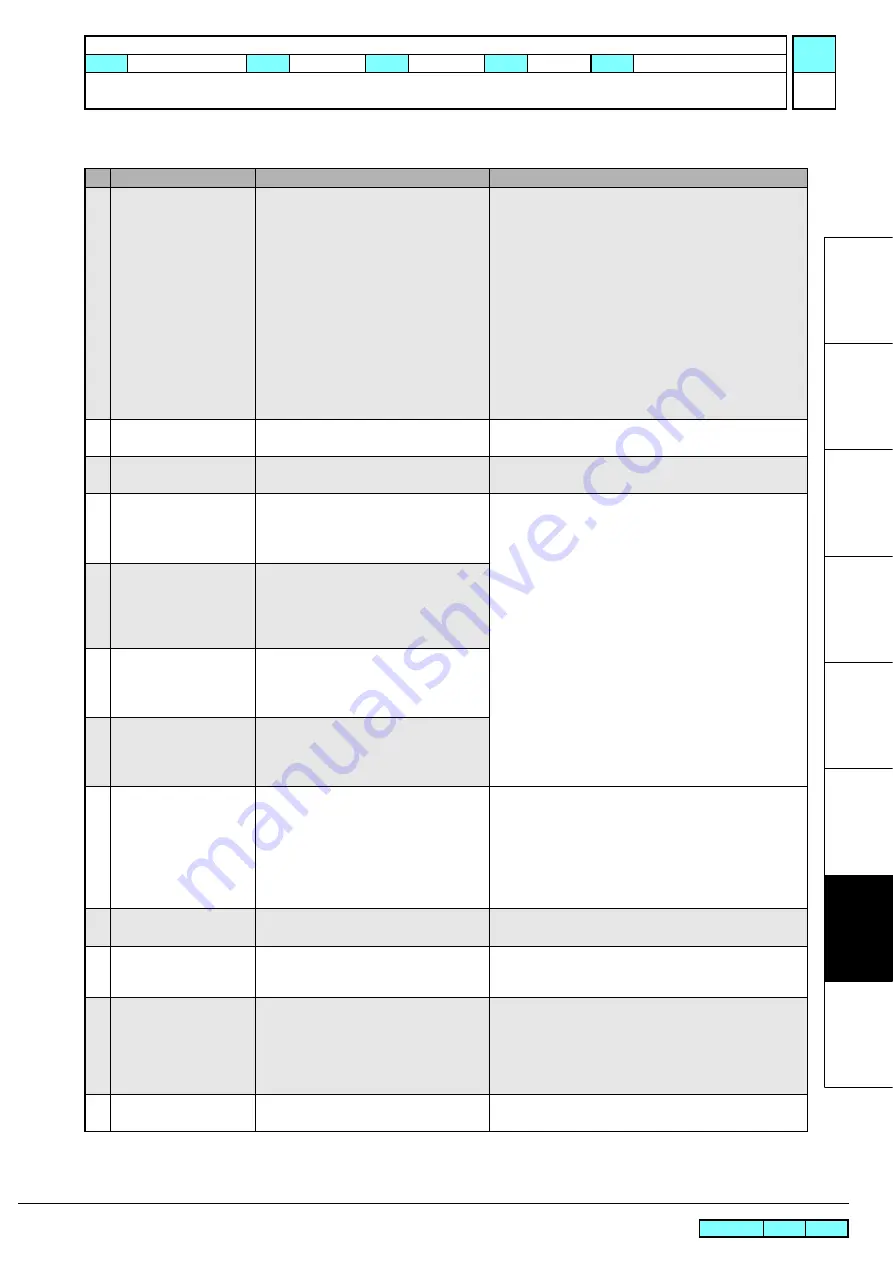
© 2014 MIMAKI ENGINEERING CO.,LTD.
7.1.2
P.6
7.1.2 List of Error Messages
1
2
3
4
5
6
7
8
60
ERROR 63c
INK REMAIN ZERO
Ink amount of the cartridge is empty.
(Non of printing, after execution of ink use-
up cleaning.)
(When the message is still displayed even after a new Ink
Cartridge or an empty Ink Cartridge is charged;)
1.
Perform and confirm [#TEST][SENSOR][CartridgeSen-
sor].
(The number correspond to the cartridge number.)
Check the peripheral and the assembly of near end sensor.
2. Check the connection of theD contact PCB Assy. and near
end sensor.
3. Replace the cartridge.
4. Replace the ID contact PCB Assy. and near end sensor with
new one.
5. Replace the CART IO PCB with a new one.
6. Replace the MAIN PCB with a new one.
(Refer to
3.3.1)
61
ERROR 650
NCU CONECT
NCU cable Assy. (E107983) is not connected
to the NCU unit.
1. Connect the NCU cable Assy. (E107983) to the NCU
unit.
62
ERROR 651
NCU SENCER LEVEL
Light quantity decreases because deterioration
of the source of light LED, dirt and wound.
1. Replace the NCU unit.
63
ERROR 652
NCU NZK CHK (HW)
H/W can not sample the Ink ejection pattern of
the NCU unit.
Many nozzle missing or trajectories have
occurred.
1. Check the nozzle condition, and when there is much
nozzle missing and trajectory, perform cleaning and
revive it.
64
ERROR 653
NCU NZK CHK (MARK)
Ink ejection pattern of the NCU unit is ana-
lyzed, and then recognized abnormal ink ejec-
tion which not reach criteria of the pattern.
The normal determination can not be made by
Many nozzle missing or trajectories.
65
ERROR 654
NCU CENTER POS
Detection of central position of the NCU unit
fails.
The normal determination can not be made by
Many nozzle missing or trajectories.
66
ERROR 655
NCU FLUSH POS
Detection of optimum position for the sensor of
the NCU unit fails.
The normal determination can not be made by
Many nozzle missing or trajectories.
67
ERROR 656
NCU SN ADJUST
Light quantity adjustment to get optimum
sensitivity fails.
①
The normal determination can not be made
by Many nozzle missing or trajectories.
②
Light quantity decreases because deteriora-
tion of the source of light LED, dirt and
wound.
1. Check the nozzle condition, and when there is much
nozzle missing and trajectory, perform cleaning and
revive it.
2. Replace the NCU unit, when error occur even if
nozzle is recovered.
68
ERROR 657
Check NCU waste ink
Waste ink tray of NCU is full.
1. Replace the waste ink tray of NCU unit.
69
ERROR 702
THERMI CONNECT
Defective of the thermistor connection
(disconnection or short)
1. Check each thermistor connection.
2. Replace the COM32 IO PCB with a new one.
(Refer to
3.3.1)
70
ERROR 710
HEATER TEMP ERROR
Heater dose not turn off.
Error is displayed in 80 degrees Celsius or
more.
1. Check the heater temperature.
2. Check the connection of the heater (PRE, PRT, POST).
3. Replace the cooling fan.
4. Replace the AC PCB.
5. Replace the COM32IO PCB.
(Refer to 6.4.2)
71
ERROR 901
INVALID OPERATION
Function cannot carry out by some errors.
1. Return to a local screen and confirm the error situation.
List of Error Messages (6/7)
No.
LCD
Cause
List of Countermeasures
R.1.0
MAINTENANCE MANUAL > Troubleshooting > Details on Errors and Malfunctions > List of Error Messages
Model
JV300-130/160
Issued 2014.05.30 Revised
F/W ver
1.10
Remark
1.0
Rev.
Summary of Contents for JV300-130 A
Page 243: ......
Page 244: ...D500946 10 30052014 MIMAKI ENGINEERING CO LTD 2014 KF FW 1 1 ...