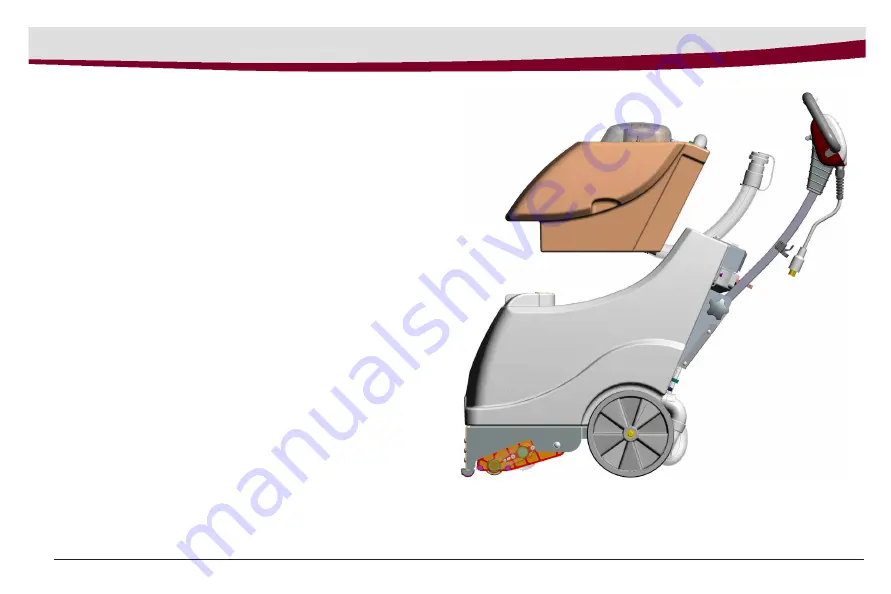
18
© 2015 Minuteman International, Inc.
X17 ECO CFS Carpet Extractor #988751UM Rev. * 04/15
Machine Overview
Removable Recovery Tank
To remove tank:
1. Unclip dump hose from solution tank.
2. Pull recovery tank straight up.
To replace tank:
1. Feed dump hose through opening in solution tank
2. Lower tank into place. Recovery vacuum inlet will rest on
vacuum connection tube (See pg 10, items L & M)
3. Clip dump hose to solution tank.