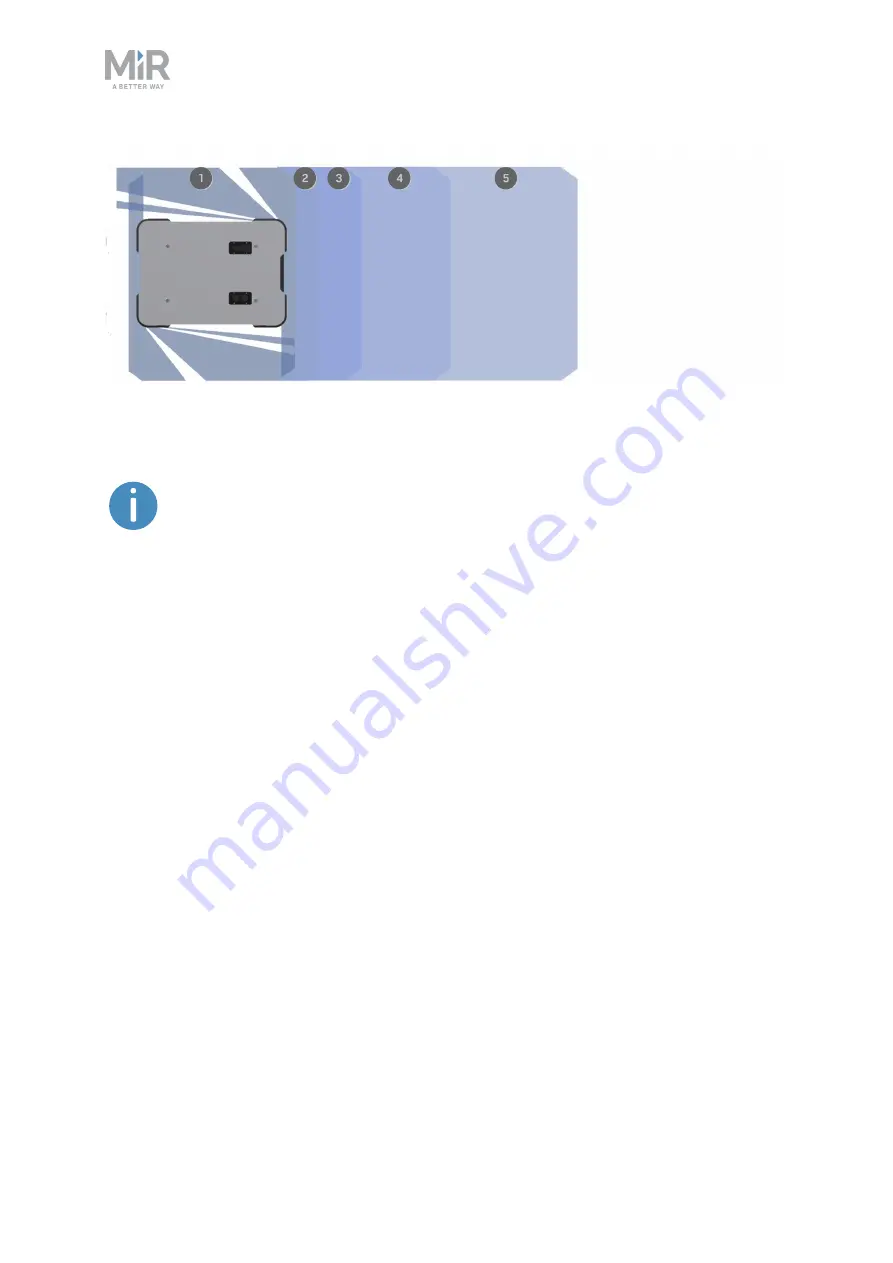
10. Safety system
MiR250 Shelf Carrier User Guide (en) 03/2021 - v.1.4 ©Copyright 2021: Mobile Industrial Robots A/S.
111
Figure 10.8. The illustration shows the blind spots introduced in the Protective fields when the robot is carrying
a shelf and the changes in the Protective fields' ranges.
The same changes apply to the backward driving Protective field set.
By default, the shelf specific Protective field sets are designed for shelves with dimensions
and specific asynchronous leg positions supported by MiR—see
. This design minimizes the blind spots at the most critical areas. If you are using
shelves that are not supported by MiR's design guidelines, the Protective field sets must be
changed and the safety system recertified—see
Personnel detection on page 104
Motion monitoring when picking up or placing shelves
When the safety PLC registers that the carrier pins are about to be raised or lowered, it is
assumed that the robot is either picking up or placing a shelf. It changes into a state where
the safety PLC only allows very slow driving. This prevents the robot from driving too fast in
case the pins do not insert correctly into the shelf or that the shelf is placed inaccurately.
Should the robot move too fast while lowering or raising the carrier pins, a Protective stop is
triggered, and you must press the Resume button to bring the robot back to an operational
state.
If the shelf is incorrectly placed, once the robot begins to move, the legs will obstruct the
active Protective field and trigger a Protective stop. It is not possible to lift the shelf to a
position where the legs are not detectable by the laser scanners.