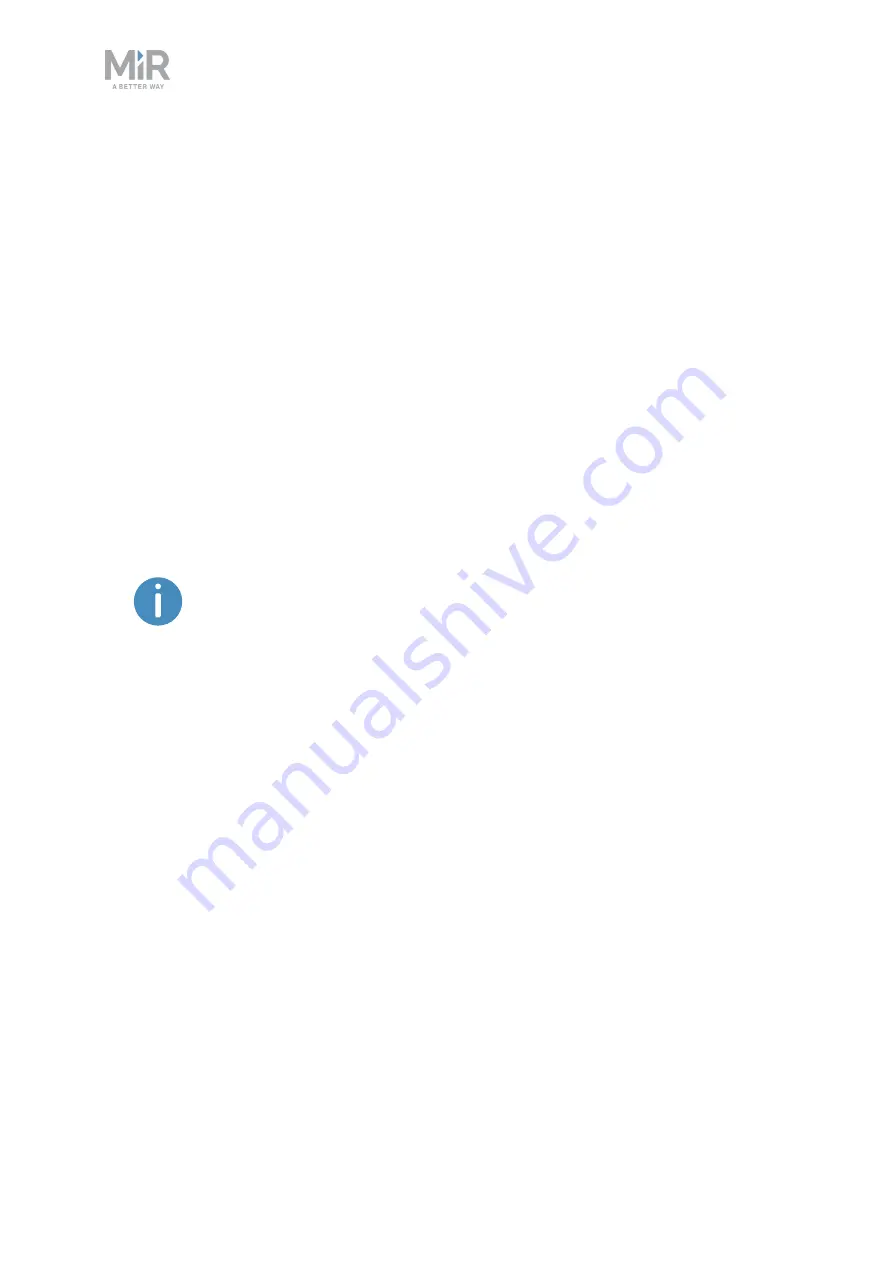
10. Safety system
MiR250 Shelf Carrier User Guide (en) 03/2021 - v.1.4 ©Copyright 2021: Mobile Industrial Robots A/S.
112
Safety contactors
There are two safety contactors inside the top module. These contactors are used to cut the
power to the carrier pin lifting mechanism. The safety PLC controls the contactors to ensure
that power is only delivered to the lifting mechanism when it is safe for the carrier pins to
change positions. There is also a feedback circuit through the safety contactors which the
safety PLC monitors to make sure that the contactors are working correctly.
10.7 Safety stop
There are two pairs of contactors used to stop MiR250 Shelf Carrier: the STO (Safe Torque
Off) contactors and the SS1 (Safe Stop 1) contactors. These are controlled by the safety PLC
and are used when the robot goes into Protective or Emergency stop. The following
processes occur to stop the robot safely:
1.
The safety PLC first turns off the STO contactors so power is cut from the motors.
To ensure that the STO contactors switch states as expected, there is a
feedback circuit that connects to the safety PLC to verify that the
contactors switch to the correct state. When the robot is starting up, the
feedback circuit and STO contactors are checked before allowing the robot
to be operated.
2.
The safety PLC turns off the SS1 contactors to activate the dynamic brake function in the
motors.
3.
The safety PLC monitors data from the motor encoders to determine whether the robot
has stopped within the expected amount of time.
4.
Once the robot has stopped, the mechanical brakes are engaged to keep the robot in
place, similar to the parking brake in a car.
The mechanical brakes are only intended to engage when the robot has stopped. Only when
the dynamic brake function does not stop the robot within the expected amount of time are
the mechanical brakes engaged to stop the robot while it is in motion. This is considered an
emergency situation where the dynamic brakes have failed, and an error is reported in the
robot interface. This can occur, for example, if the robot drives on surfaces that are not
within specifications or the load on the robot does not fulfill the payload specifications—see
Payload distribution on page 229
.