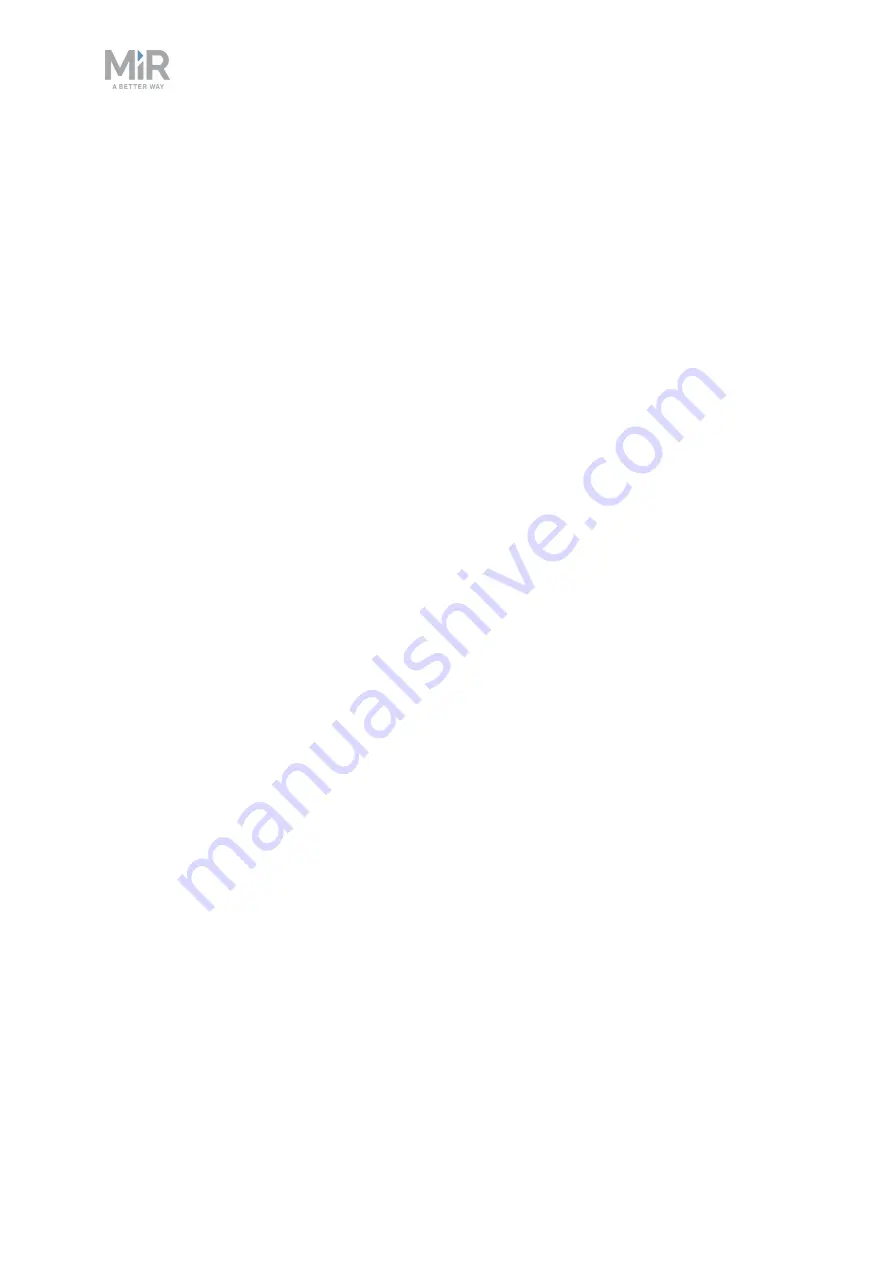
10. Safety system
MiR250 Shelf Carrier User Guide (en) 03/2021 - v.1.4 ©Copyright 2021: Mobile Industrial Robots A/S.
99
10. Safety system
The robot's safety system is designed to mitigate significant hazards which could lead to
injury, for example, stopping the robot if a person is in its path.
MiR250 Shelf Carrier is equipped with a range of built-in safety-related functions. Each
safety function is designed according to the standard ISO 13849-1. The safety-related
functions are selected to support compliance with EN 1525 and ISO 3691-4.
10.1 System overview
The safety system is controlled mainly by the safety PLC. The PLC regulates inputs and
outputs from safety-related functions or interfaces involved with ensuring the safety of
personnel working nearby the robot.
If a safety function is triggered, the robot uses its STO (Safe Torque Off) contactors to bring
the robot to a category 0 stop (stopping by “immediate removal of power to the machine
actuators" according to IEC 60204-1) followed by a controlled brake using an SS1 (Safe Stop
1) function. This is known as bringing the robot into Emergency stop or Protective stop,
depending on the function—see
.
Types of stop
There are four different stopped states:
•
Operational stop
•
Protective stop
•
Emergency stop
•
Manual stop
The last three types of stop are monitored by the safety PLC.
Operational stop
The robot is in Operational stop when it is stopped through the robot interface either
through a mission action or by pausing the mission. The top module and all moving parts are
still connected to a power supply.