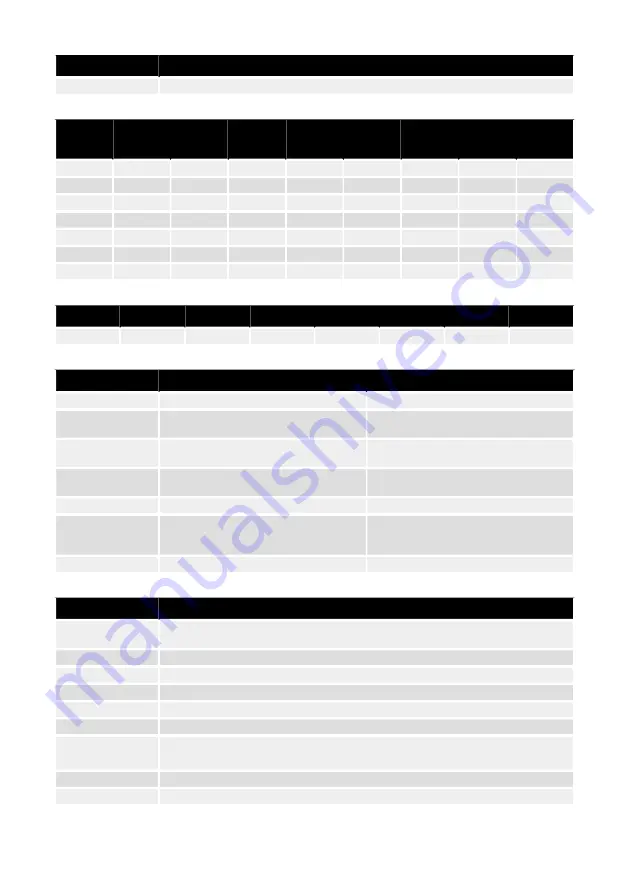
Description
Indicator
Possible tool wiring fault. Turns red when a possible fault in tool C+/C–/P+/P– wiring is detected.
D36
Speed set-point display
BIT 1
D2
BIT 2
D3
BIT 3
D17
BIT 4
D18
BIT 5
D19
BIT 6
D20
BIT 7
D21
BIT 8
D22
RPM
ON
OFF
OFF
OFF
OFF
OFF
OFF
-
≥ 4,000
ON
ON
OFF
OFF
OFF
OFF
OFF
-
≥ 5,000
ON
ON
ON
OFF
OFF
OFF
OFF
-
≥ 6,000
ON
ON
ON
ON
OFF
OFF
OFF
-
≥ 7,000
ON
ON
ON
ON
ON
OFF
OFF
-
≥ 8,000
ON
ON
ON
ON
ON
ON
OFF
-
≥ 9,000
ON
ON
ON
ON
ON
ON
ON
-
≥ 10,000
Modbus RTU slave address display
BIT 1
BIT 2
BIT 3
BIT 4
BIT 5
BIT 6
BIT 7
BIT 8
D2
D3
D17
D18
D19
D20
D21
D22
Jumper description
Description
Default
Jumpers
Reserved for future use
Not set
JP1
If set, a terminating resistor of 270 Ω is connec-
ted across Modbus RTU pins A and B.
Not set
JP2
If set, a pull-down resistor of 10 kΩ is connec-
ted to Modbus RTU B-pin.
Not set
JP3
If set, a pull-up resistor of 10 kΩ is connected
to Modbus RTU A-pin.
Not set
JP4
If set, digital speed control feature is enabled.
Not set
JP12
If set, D2–D3, D17–D22 indicators will output
the current Modbus RTU slave address instead
of speed set-point.
Not set
JP13
Reset to factory settings.
Not set
JP15
Tool cable connector pinout
Description
Pin (colour, size)
Not in use
PE (green–yellow,
1.0 mm2)
Phase A
1 (brown, 1.00 mm²)
Phase B
2 (blue, 1.00 mm²)
Phase C
3 (black, 1.00 mm²)
C-
A (grey, 0.25 mm²)
C+
B (pink, 0.25 mm²)
P–
C (green, 0.25 mm²)
NTC–
C (yellow, 0.25 mm²)
NTC+
D (brown, 0.25 mm²)
P+
E (white, 0.25 mm²)
NOTE! NTC– and P– are connected together to the same PIN inside the connector.
8
en (original)