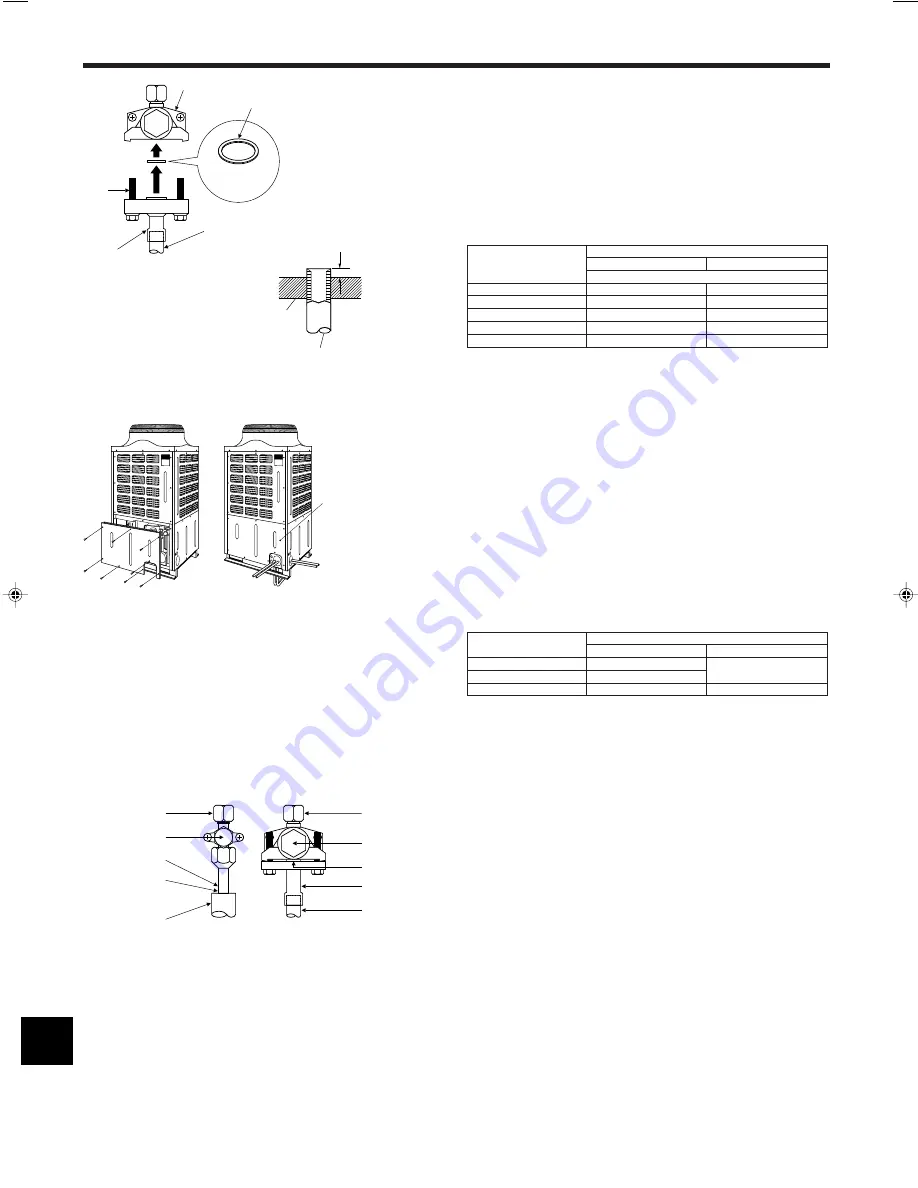
8
5. Installing the refrigerant piping
(3)Use the following procedure for connecting the gas-side piping. (Fig. 5-2)
1.Remove the flange and packing attached to the valve body. These were mounted
at the time of shipping from the factory to prevent refrigerant leakage.
* Never attempt to reuse this packing as refrigerant leakage will occur.
2.Braze the flange joint
2
provided to the outdoor unit using locally procured
brazing materials.
* Always perform this brazing before mounting the stop valve.
3.Always attach the new packing
3
, provided, for the connecting pipe with the
flange to the valve body before connecting the piping to the stop valve.
* The tightening torque for M10 bolts for the flange joint : 25.2 N·m ±15%.
(4)After connecting the installing bolts for the refrigerant piping, check for gas leak-
age in the locally installed piping and indoor units.
Table 3 (Fig. 5-3)
Copper pipe O.D.
A (mm)
(mm)
Flare tool for R410A
Flare tool for R22·R407C
Clutch type
ø6.35 (1/4")
1.0 - 1.5
0 - 0.5
ø9.52 (3/8")
1.0 - 1.5
0 - 0.5
ø12.7 (1/2")
1.0 - 1.5
0 - 0.5
ø15.88 (5/8")
1.0 - 1.5
0 - 0.5
ø19.05 (3/4")
1.0 - 1.5
0 - 0.5
5.3. Refrigerant piping (Fig. 5-4)
Remove the service panel
A
(eight screw).
(1) Perform refrigerant piping connections for the indoor/outdoor unit when the out-
door unit’s stop valve is completely closed.
(2) Vacuum-purge air from the indoor unit and the connection piping.
(3) After connecting the refrigerant pipes, check the connected pipes and the indoor
unit for gas leaks. (Refer to 5.4 Refrigerant pipe airtight testing method)
(4) Vacuumize the refrigerant lines through the service port of the liquid stop valve
and then open the stop valves completely (for both the liquid and gas stop valves).
This will completely connect the refrigerant lines of the indoor and outdoor units.
• If the stop valves are left closed and the unit is operated, the compressor and
control valves will be damaged.
• Use a leak detector or soapy water to check for gas leaks at the pipe connec-
tion sections of the outdoor unit.
• Do not use the refrigerant from the unit to purge air from the refrigerant lines.
• After the valve work is completed, tighten the valve caps to the correct torque.
Valve size
Tightening torque N·m (kgf·cm)
Valve cap
Service port cap
3/8 ø9.52
22-28 (220-280)
12-16
1/2 ø12.7
25-31 (250-310)
(120-160)
1 ø25.4
36-44 (360-440)
11.5-13.9 (115-139)
Failure to replace and tighten the caps may result in refrigerant leakage. In
addition, do not damage the insides of the valve caps as they act as a seal to
prevent refrigerant leakage.
(5) Use sealant to seal the ends of the thermal insulation around the pipe connection
sections to prevent water from entering the thermal insulation.
5.4. Refrigerant pipe airtight testing method (Fig. 5-5)
(1) Connect the testing tools.
• Make sure the stop valves
A
B
are closed and do not open them.
• Add pressure to the refrigerant lines through the service port
C
of the liquid
stop valve
D
.
(2) Do not add pressure to the specified pressure all at once; add pressure little by little.
1
Pressurize to 0.5 MPa (5 kgf/cm
2
G), wait five minutes, and make sure the
pressure does not decrease.
2
Pressurize to 1.5 MPa (15 kgf/cm
2
G), wait five minutes, and make sure the
pressure does not decrease.
3
Pressurize to 3.6 MPa (36 kgf/cm
2
G) and measure the surrounding tempera-
ture and refrigerant pressure.
(3) If the specified pressure holds for about one day and does not decrease, the pipes
have passed the test and there are no leaks.
• If the surrounding temperature changes by 1 °C, the pressure will change by
about 0.03 MPa (0.3 kgf/cm
2
G). Make the necessary corrections.
(4) If the pressure decreases in steps (2) or (3), there is a gas leak. Look for the
source of the gas leak.
A
Die
B
Copper pipe
A
A
B
Fig. 5-3
A
Service panel
B
Right-side piping (Knock-out)
C
Lower piping (Knock-out)
D
Front piping (Knock-out)
A
Stop valve <Liquid side>
B
Stop valve <Gas side>
C
Service port
D
Open/Close section
E
Local pipe
F
Sealed, same way for gas side
G
Pipe cover
H
Packing (Provided part)
I
Connecting pipe (Provided part)
J
Use non-oxidizing brazing material on flange joint.
K
Locally procured pipe connection
M10
Bolt
Fig. 5-4
Fig. 5-5
1
Main unit of valve
2
Flange connection
3
Packing
4
Always change to the new
packing provided.
5
Local piping
3
4
1
2
5
A
B
C
D
A
C
D
E
F
G
B
C
D
H
I
E
J
K
Fig. 5-2
Summary of Contents for 250 YHA-A
Page 15: ......