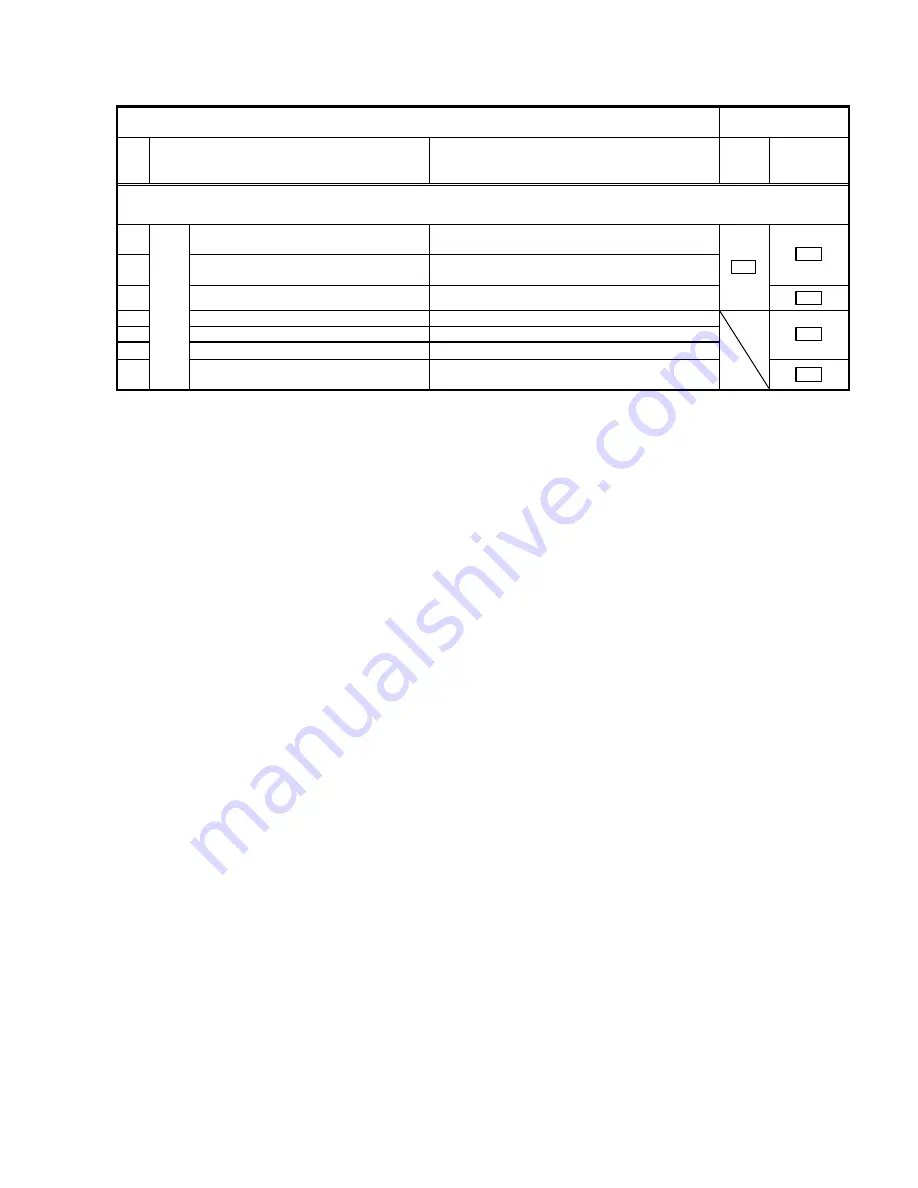
PCKN-OIL738
32
6.4.2.2 Relay with RS232C communication I/F
Item
Corresponding section of
general operation manual
No. Designation
Description
Indication
mode
Setting / forced
operation /
option mode
As the same as Table 6.3 described in item 6.4.2.1 about the No. 010
〜
860.
901
VT primary side [V]
Set the VT primary voltage of the voltage circuit
connected to the relay.
902
VT secondary side [V]
Set the VT secondary voltage of the voltage circuit
connected to the relay.
D-3
903
Relay password enable/disable option
Set relay password enable or disable for setting.
A-7
D-9
904
Max. record reset
Clear data of the max. record.
905
Fault record reset
Clear data of the fault record.
906
Self-diagnosis
(ALARM) reset
Clear data of the s
elf-diagnosis
record.
D-4
907
LED lamp test
Carry out forced illumination of all the LED lamps
on the front of the relay unit.
D-5