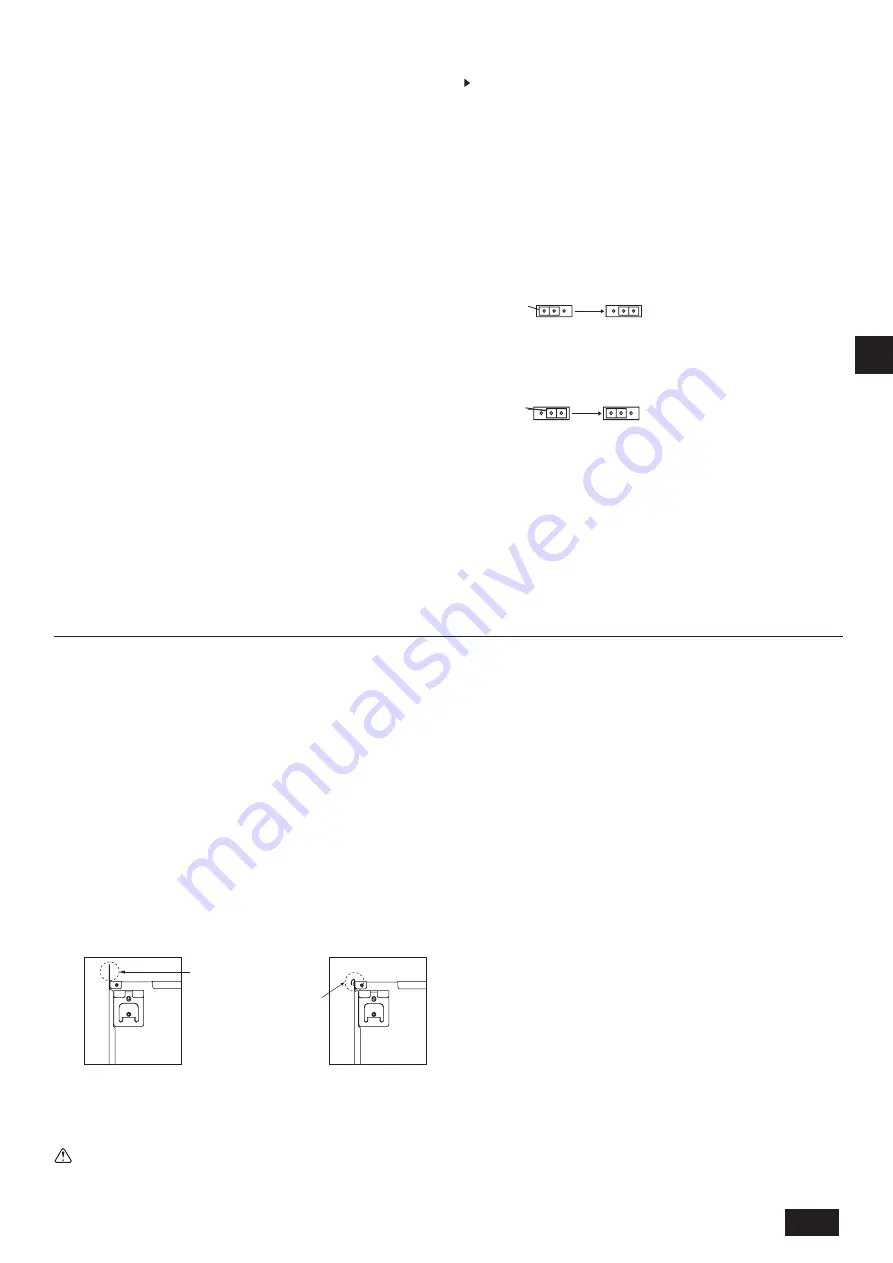
11
GB
D
F
E
I
NL
P
GR
RU
TR
CZ
SV
HG
PO
5. Attach the insulating material, and fix it with the band (accessory) to insulate
the drain port.
[Fig. 7.2.2] (P.4)
A
Indoor unit
B
Tie band (accessory)
C
Visible part
D
Insertion margin
E
Drain hose (accessory)
F
Drain pipe (O.D. ø32 mm [1-1/4 in] PVC TUBE, field supply)
G
Insulating material (field supply)
H
Tie band (accessory)
7.3. Confirming drain discharge
Make sure that the drain-up mechanism operates normally for discharge
and that there is no water leakage from the connections.
• Be sure to confirm the above in a period of heating operation.
• Be sure to confirm the above before ceiling work is done in the case of a new
construction.
1. Remove the water supply port cover on the same side as the indoor unit pip-
ing.
2. Fill water into the feed water pump using a feed water tank. In filling, be sure to
put the end of the pump or tank in a drain pan. (If the insertion is incomplete,
water may flow over the machine.)
3. Perform the test run in cooling mode, or connect the connector to the ON
side of SWE on the Indoor controller board. (The drain pump and the fan are
forced to operate without any remote controller operation.) Make sure using
a transparent hose that drain is discharged.
SWE
SWE
OFF
ON
OFF
ON
< OFF >
< ON >
Connector
4. After confirmation, cancel the test run mode, and turn off the main power.
If the
connector is connected to the ON side of SWE, disconnect it and connect it to
the OFF side, and attach the water supply port cover into its original position.
SWE
SWE
OFF
ON
OFF
ON
< ON >
< OFF >
Connector
[Fig. 7.3.1] (P.5)
A
Insert pump's end 2 to 4 cm [13/16 to 1-5/8 in].
B
Remove the water supply port.
C
About 2500 cc
D
Water
E
Filling port
F
Screw
[Fig. 7.3.2] (P.5)
<Indoor controller board>
8. Duct work
• In connecting duct, insert canvas duct between unit and duct.
• Use incombustible material for duct parts.
• Provide full insulation to inlet duct flange and outlet duct to prevent condensa-
tion.
• Be sure to change the position of air filter to the position where it can be serv-
iced.
[Fig. 8.0.1]
(P.5)
<A> In case of rear inlet
<B> In case of bottom inlet
A
Duct
B
Air inlet
C
Access door
D
Canvas duct
E
Ceiling surface
F
Air outlet
G
Leave distance enough to prevent short cycle
• Procedure for changing the rear inlet to the bottom inlet.
[Fig. 8.0.2]
(P.5)
A
Filter
B
Bottom plate
1. Remove air filter. (First remove filter lock screw.)
2. Remove the bottom plate.
3. Fit the bottom plate to the rear of the body.
[Fig. 8.0.3] (P.5)
(Position of lug-holes on the plate are different from those for rear inlet.)
When the plate is attached on
the rear side, it exceeds the
height of the rear body panel.
Replicate the plate along the slit
when there is not enough room
above for the entire unit.
Screw holes are hidden under
the insulation. Screw through
the insulation to screw the plate
down.
4. Fit filter to the underside of the body.
(Be careful of which side of the filter to fit.)
[Fig. 8.0.4] (P.5)
[Fig. 8.0.4]
(P.5)
C
Nail for the bottom inlet
D
Nail for the rear inlet
Caution:
•
Inlet duct of 850 mm [33-1/2 in] or more should be constructed.
To connect the air conditioner main body and the duct for potential
equalization.
•
To reduce the risk of injury from metal sheet edges, wear protective gloves.
•
To connect the air conditioner main body and the duct for potential
equalization.
•
The noise from the intake will increase dramatically if intake is fitted
directly beneath the main body. Intake should therefore be installed as
far away from the main body as possible.
Particular care is required when using it with bottom inlet specifications.
• Install sufficient thermal insulation to prevent condensation forming on
outlet duct flanges and outlet ducts.
• Keep the distance between the inlet grille and the fan over 850 mm [33-1/2
in].
If it is less than 850 mm [33-1/2 in], install a safety guard not to touch the
fan.
•
To avoid electrical noise interference, do not run transmission lines at
the bottom of the unit.