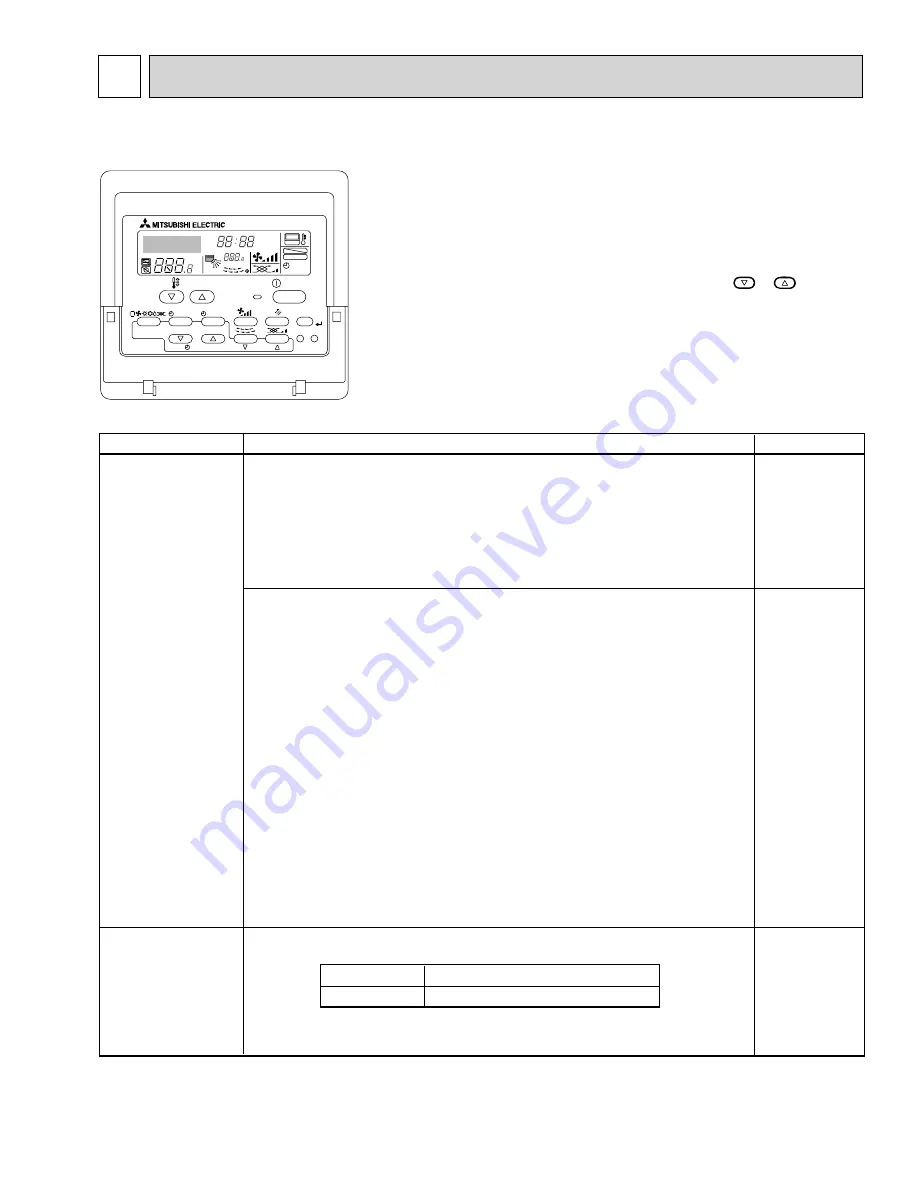
15
MICROPROCESSOR CONTROL
9
PAR-21MAA
ON/OFF
FILTER
CHECK
OPERATION
CLEAR
TEST
TEMP.
MENU
BACK
DAY
MONITOR/SET
CLOCK
ON/OFF
ûFûC
°F °C
ERROR CODE
AFTER
TIMER
TIME SUN MON TUE WED THU FRI SAT
ON
OFF
Hr
AFTER
FILTER
FUNCTION
ONLY1Hr.
WEEKLY
SIMPLE
AUTO OFF
INDOOR UNIT CONTROL
9-1. COOL OPERATION
Control modes
Control details
1-1. Thermoregulating function (Function to prevent restarting for 3 minutes)
• Room temperature
desired tempe 2°F ···Thermo ON
• Room temperature
desired temperature ···Thermo OFF
1-2. Anti-freezing control
Detected condition : When the liquid pipe temp. (TH22) is 32°F or less in 16
minutes from compressor's start up, anti-freezing control
starts and the thermo OFF.
Released condition : The timer which prevents reactivating is set for 3 minutes,
and anti-freezing control is cancelled when any one of the
following conditions is satisfied.
Liquid pipe temp. (TH22) turns 50°F or above.
The condition of the thermo OFF has completed by
thermoregulating,
etc.
The operation modes became mode other than COOL.
The operation stopped.
By the remote controller setting (switch of 3 speeds)
2. Fan
1. Thermoregulating
function
Remarks
Type
Fan speed notch
[Low], [Med], [High]
3 speeds type
Continued to the next page
<How to operate>
1
Press POWER ON/OFF button.
2
Press the operation MODE button to display COOL.
3
Press the TEMP. button to set the desired temperature.
NOTE
: The set temperature changes 1°F(2°F) when the or button is
pressed once. Cooling 67 to 87°F
Variable range of the set temprature depends on the remote controller
which is applied.