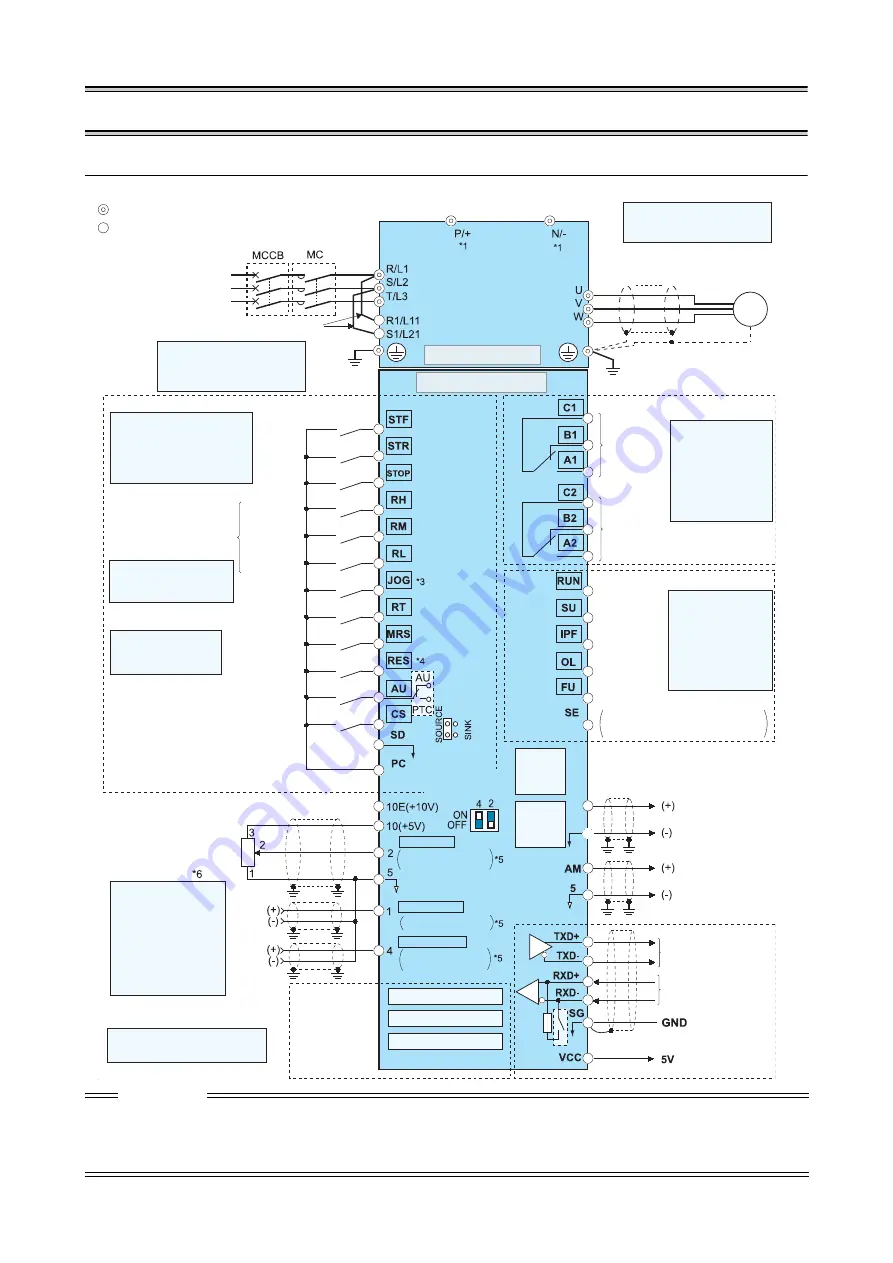
4
3 WIRING
3.1 Terminal connection diagram
CAUTION
To prevent a malfunction due to noise, keep the signal cables more than 10cm away from the power cables. Also separate the main
circuit wire of the input side and the output side.
After wiring, wire offcuts must not be left in the inverter. Wire offcuts can cause an alarm, failure or malfunction. Always keep the
inverter clean. When drilling mounting holes in an enclosure etc., take care not to allow chips and other foreign matter to enter the
inverter.
Set the voltage/current input switch correctly. Different setting may cause a fault, failure or malfunction.
FM
SD
Source logic
Main circuit terminal
Control circuit terminal
Jumper
*2
Earth
*1 Do not connect any options
to P/+ and N/
−
.
Motor
*2 To supply power to the
control circuit separately,
remove the jumper across
R1/L11 and S1/L21.
3-phase AC
power supply
Main circuit
Control circuit
Terminal functions vary with
the input terminal
assignment.
(
Pr. 178 to Pr. 189
)
Control input signals (No voltage input allowed)
Forward
rotation
start
Reverse
rotation
start
Start self-
holding
selection
High
speed
Middle
speed
Low
speed
Multi-speed selection
Jog mode
Second function selection
Output stop
Reset
Current input selection
Selection of automatic restart after
instantaneous power failure
Contact input common (Sink*)
*3 JOG terminal can be used
as pulse train input
terminal. Use
Pr. 29
1 to
select JOG/pulse.
24 V DC power supply/max. 100 mA load current
Contact input common (Source*)
*(Common for external power supply transistor)
Frequency setting signal (Analog)
Auxiliary
input
Terminal 4
input
(Current
input)
0–5V DC
0– ±10V DC
4–20mA DC
0 to 10V DC
0 to 20mA DC
0 to ±5V DC
0 to 5V DC
0 to 10V DC
PU
connector
Connector for
plug-in option
connection
Option connector 1
Terminating
resistor
*5 Terminal input specifica
tions can be changed by
analog input specifications
switchover
(Pr. 73, Pr. 267).
Set the voltage/current
input switch in the OFF
position to select voltage
input (0 to 5V/0 to10V) and
ON to select current input
(4 to 20mA).
*6 It is recommended to use 1k
Ω
, 2W
potentiometer when the frequency
setting signal is changed frequently.
Relay output 1
(Fault output)
Relay output 2
Running
Instantaneous
power failure
Up to frequency
Overload
Terminal functions
vary with the output
terminal assignment
(
Pr. 195, Pr. 196
)
Terminal functions
vary with the output
terminal assignment
(
Pr. 190 to Pr. 194
)
Frequency detection
Open collector output common
Sink/source common
Pulse output
Analog signal output
(0 to 10VDC)
RS-485 terminals
Data transmission
Data reception
(Permissible load
current 100mA)
Frequency setting
potentiometer
1k
Ω
,
1/2W
M
3~
*4 AU terminal can be
used as PTC input
terminal.
*5 Voltage/
current
input switch
Option connector 2
Option connector 3
Relay output
USB
connector
Open collector output