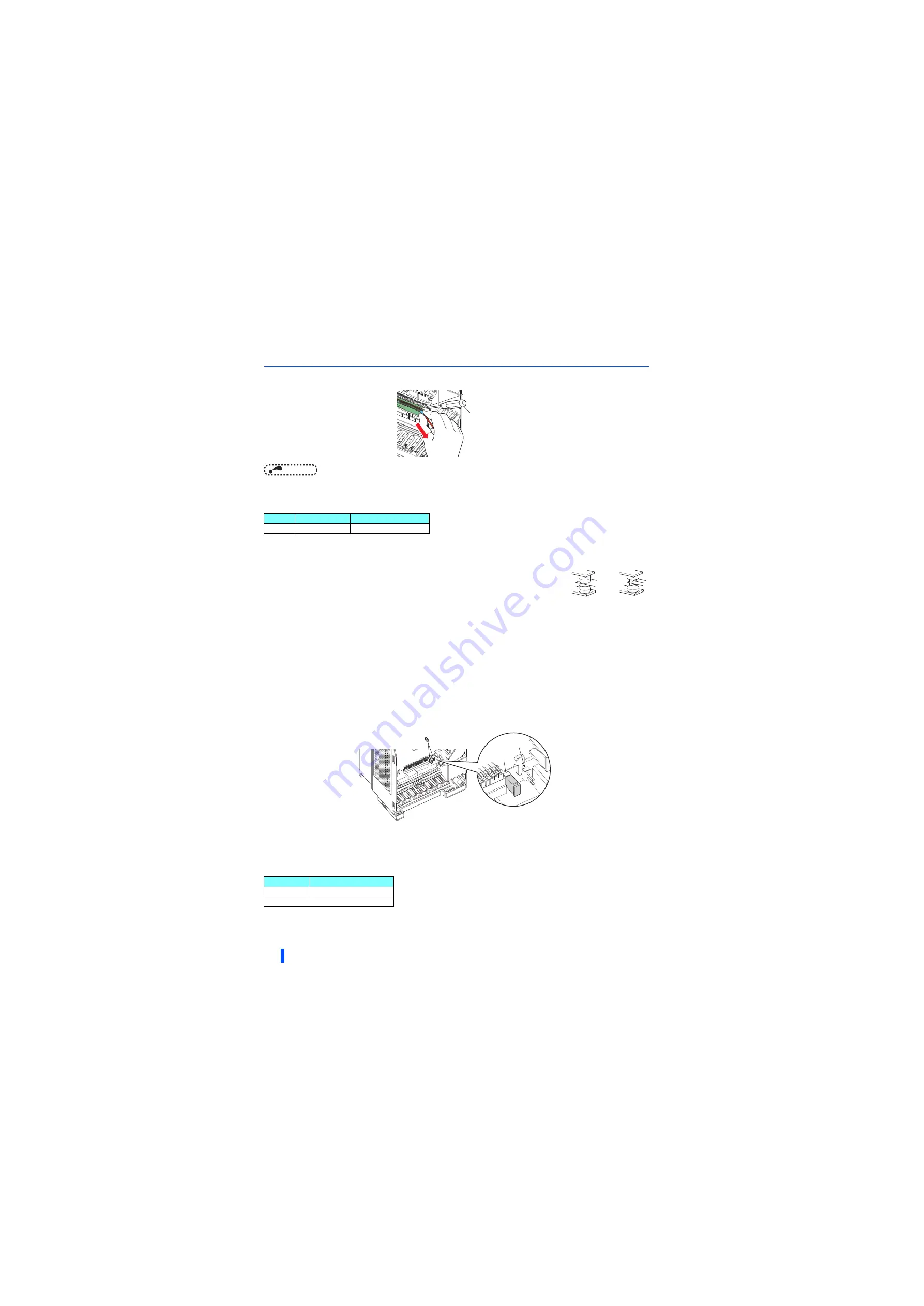
12
Control circuit terminal
• Wire removal
Pull the wire while pushing the open/close button all the way down firmly with a flathead screwdriver.
NOTE
• When using stranded wires without a blade terminal, twist enough to avoid short circuit with a nearby terminals or wires.
• During wiring, pulling out the wire forcefully without pushing the open/close button all the way down may damage the terminal block.
• Use a small flathead screwdriver (tip thickness: 0.4 mm, tip width: 2.5 mm).
If a flathead screwdriver with a narrow tip is used, terminal block may be damaged.
Commercially available products (as of February 2016).
• Place the flathead screwdriver vertical to the open/close button. In case the blade tip slips, it may cause an inverter damage or injury.
Wiring precautions
• It is recommended to use a cable of 0.3 to 0.75 mm
2
for connection to the control circuit terminals.
• The wiring length should be 30 m (200 m for terminal FM) at the maximum.
• Use two or more parallel micro-signal contacts or twin contacts to prevent contact faults when using contact inputs since
the control circuit input signals are micro-currents.
• To suppress EMI, use shielded or twisted cables for the control circuit terminals and run them away from the main and
power circuits (including the 200 V relay sequence circuit). For the cables connected to the control circuit terminals,
connect their shields to the common terminal of the connected control circuit terminal. When connecting an external
power supply to terminal PC, however, connect the shield of the power supply cable to the negative side of the external power supply. Do not directly earth
(ground) the shield to the enclosure, etc.
• Always apply a voltage to the fault output terminals (A1, B1, C1, A2, B2, C2) via a relay coil, lamp, etc.
• When using an external power supply for transistor output, note the following points to prevent a malfunction caused by undesirable current.
Do not connect any terminal SD on the inverter and the 0 V terminal of the external power supply (when the sink logic is selected).
Do not connect terminal PC on the inverter and the +24 V terminal of the external power supply (when the source logic is selected).
Do not install an external power source in parallel with the internal 24 VDC power source (connected to terminals PC and SD) to use them together.
Refer to Chapter 2 of the Instruction Manual (Detailed) for the detail.
Control logic (sink/source) change
Change the control logic of input signals as necessary.
To change the control logic, change the jumper connector position on the control circuit board.
Connect the jumper connector to the connector pin of the desired control logic.
The control logic of input signals is initially set to the sink logic (SINK).
(The output signals may be used in either the sink or source logic independently of the jumper connector position.)
When supplying 24 V external power to the control circuit
Connect a 24 V external power supply across ter24 and SD. Connecting a 24 V external power supply enables I/O terminal ON/OFF operation, operation
panel displays, control functions, and communication during communication operation even during power-OFF of inverter's main circuit power supply.
During the 24 V external power supply operation, "EV" blinks on the operation panel.
Applied 24 V external power specification
Name
Model
Manufacturer
Screwdriver
SZF 0- 0,4 x 2,5
Phoenix Contact Co., Ltd.
Item
Rated specification
Input voltage
23 to 25.5 VDC
Input current
1.4 A or less
Flathead screwdriver
Open/close button
Micro signal contacts
Twin contacts
For sink logic
SOURCE
SINK
Jumper connector