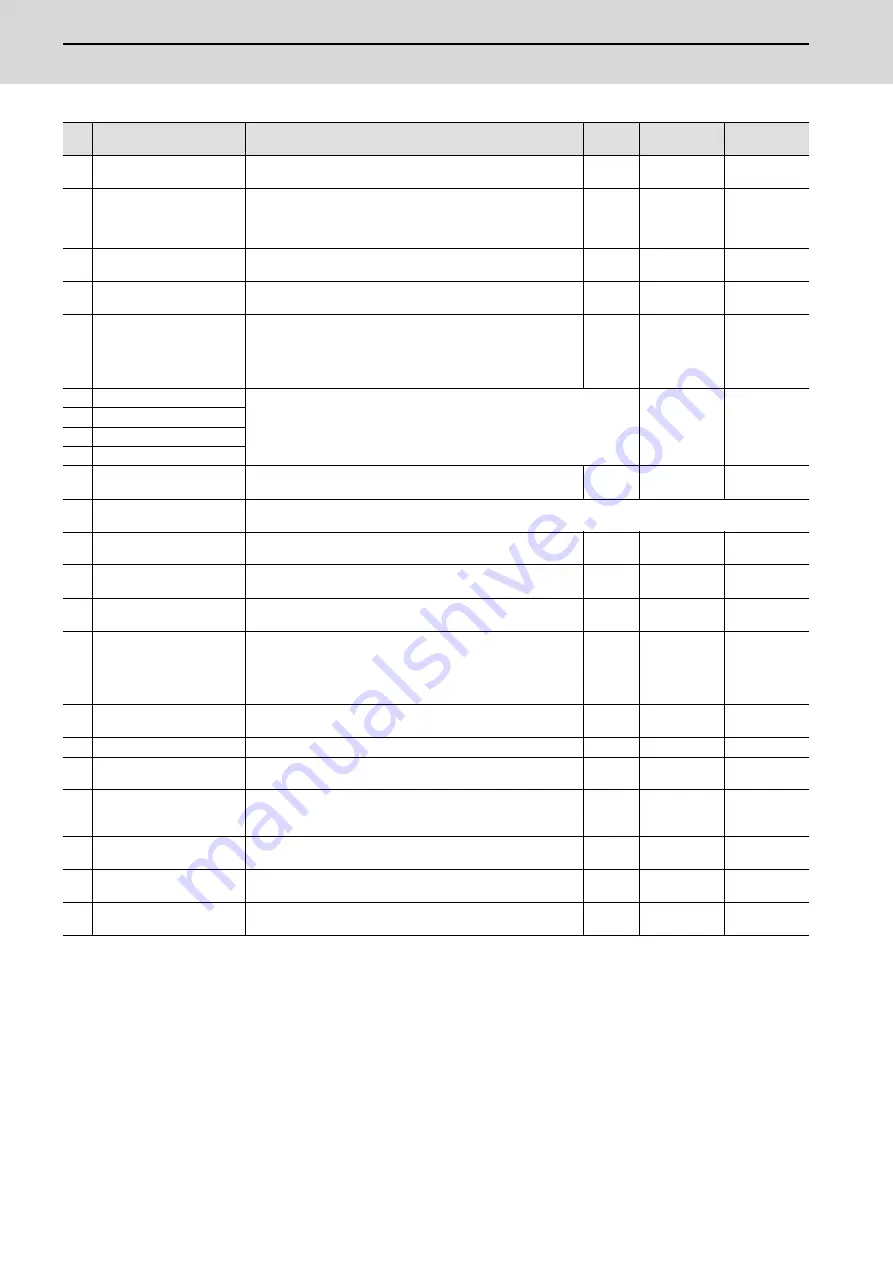
MDS-E/EH Series Instruction Manual
7 Troubleshooting
378
IB-1501229-F
(Note 1) Definitions of terms in the table are as follows.
Main side encoder: Encoder connected to CN2
Sub side encoder: Encoder connected to CN3
(Note 2) Resetting methods
NR: Reset with the NC RESET button. This alarm can also be reset with the PR and AR resetting conditions.
PR: Reset by turning the NC power ON again. This alarm can also be reset with the AR resetting conditions.
When the control axis is removed, this alarm can be reset with the NC RESET button. (Excluding alarms 32 and 37.)
AR: Reset by turning the NC and servo drive unit power ON again.
No.
Name
Details
Reset
method
Servo
stop method
Spindle
stop method
41 Feedback error 3
Either a missed feedback pulse in the motor side encoder or an
error in the Z-phase was detected in the full closed loop system.
PR
Dynamic stop Coast to a stop
42 Feedback error 1
Either a missed feedback pulse in the position detection or an
error in the Z-phase was detected. Or the distance-coded refer-
ence check error exceeded the allowable value when the dis-
tance-coded reference scale was used.
PR
Dynamic stop Coast to a stop
43 Feedback error 2
An excessive difference in feedback was detected between the
machine side encoder and the motor side encoder.
PR
Dynamic stop Coast to a stop
45 Fan stop
An overheat of the power module was detected during the cool-
ing fan stopping.
PR
Dynamic stop Coast to a stop
46 Motor overheat /
Thermal error
Either the motor or the motor side encoder detected an over-
heat.
Or, the thermistor signal receiving circuit of the linear motor or
direct-drive motor was disconnected.
Or, the thermistor signal receiving circuit was short-circuited.
NR
Deceleration
stop
Deceleration
stop
48 Main side encoder: Error 5 An error was detected by the encoder connected to the main side.
The error details are different according to the connected encoder.
Refer to "Encoder alarm".
Dynamic stop Coast to a stop
49 Main side encoder: Error 6
4A Main side encoder: Error 7
4B Main side encoder: Error 8
4C Current error at initial mag-
netic pole estimate
Current detection failed at the initial magnetic pole estimation.
NR
Dynamic stop Coast to a stop
4D Dual signal error
An error was detected in the signal related to the dual signal.
Refer to "Dual signal error (4D)" for details.
4E NC command mode error
An error was detected in the control mode send from the NC.
NR
Deceleration
stop
Deceleration
stop
4F Instantaneous power inter-
rupt
The control power supply has been shut down for 50ms or more.
NR
Deceleration
stop
Deceleration
stop
50 Overload 1
Overload detection level became 100% or more. The motor or
the drive unit is overloaded.
NR
Deceleration
stop
Deceleration
stop
51 Overload 2
In a servo system, current command of 95% or more of the unit’s
max. current was given continuously for 1 second or longer. In
a spindle system, current command of 95% or more of the mo-
tor’s max. current was given continuously for 1 second or lon-
ger.
NR
Deceleration
stop
Deceleration
stop
52 Excessive error 1
A position tracking error during servo ON was excessive.
NR
Deceleration
stop
Deceleration
stop
53 Excessive error 2
A position tracking error during servo OFF was excessive.
NR
Dynamic stop
-
54 Excessive error 3
There was no motor current feedback when the alarm "Exces-
sive error 1" was detected.
NR
Dynamic stop Coast to a stop
56 Commanded speed error
The encoder has detected that the commanded speed exceed-
ed 1.15 times of the rapid traverse rate (rapid), or the motor ro-
tation speed exceeded the maximum speed.
NR
-
Deceleration
stop
58 Collision detection 1: G0
A disturbance torque exceeded the allowable value in rapid tra-
verse modal (G0).
NR
Max cap dec
stop
-
59 Collision detection 1: G1
A disturbance torque exceeded the allowable value in the cut-
ting feed modal (G1).
NR
Max cap dec
stop
-
5A Collision detection 2
A current command with the maximum drive unit current value
was detected.
NR
Max cap dec
stop
-
Summary of Contents for MDS-E
Page 1: ......
Page 3: ......
Page 15: ......
Page 17: ......
Page 19: ......
Page 21: ......
Page 31: ......
Page 32: ...1 IB 1501229 F 1 Installation ...
Page 76: ...45 IB 1501229 F 2 Wiring and Connection ...
Page 132: ...101 IB 1501229 F 3 Safety Function ...
Page 142: ...111 IB 1501229 F 4 Setup ...
Page 277: ...MDS E EH Series Instruction Manual 4 Setup 246 IB 1501229 F ...
Page 278: ...247 IB 1501229 F 5 Servo Adjustment ...
Page 351: ...MDS E EH Series Instruction Manual 5 Servo Adjustment 320 IB 1501229 F ...
Page 352: ...321 IB 1501229 F 6 Spindle Adjustment ...
Page 404: ...373 IB 1501229 F 7 Troubleshooting ...
Page 455: ...MDS E EH Series Instruction Manual 7 Troubleshooting 424 IB 1501229 F ...
Page 456: ...425 IB 1501229 F 8 Maintenance ...
Page 475: ...MDS E EH Series Instruction Manual 8 Maintenance 444 IB 1501229 F ...
Page 476: ...445 IB 1501229 F 9 Power Backup System ...
Page 494: ...463 IB 1501229 F 10 Appx 1 Cable and Connector Assembly ...
Page 504: ...473 IB 1501229 F 11 Appx 2 D A Output Specifications for Drive Unit ...
Page 514: ...483 IB 1501229 F 12 Appx 3 Protection Function ...
Page 523: ...MDS E EH Series Instruction Manual 12 Appx 3 Protection Function 492 IB 1501229 F ...
Page 524: ...493 IB 1501229 F 13 Appx 4 Compliance to EC Directives ...
Page 528: ...497 IB 1501229 F 14 Appx 5 EMC Installation Guidelines ...
Page 540: ...509 IB 1501229 F 15 Appx 6 Higher Harmonic Suppression Measure Guidelines ...
Page 550: ......
Page 554: ......