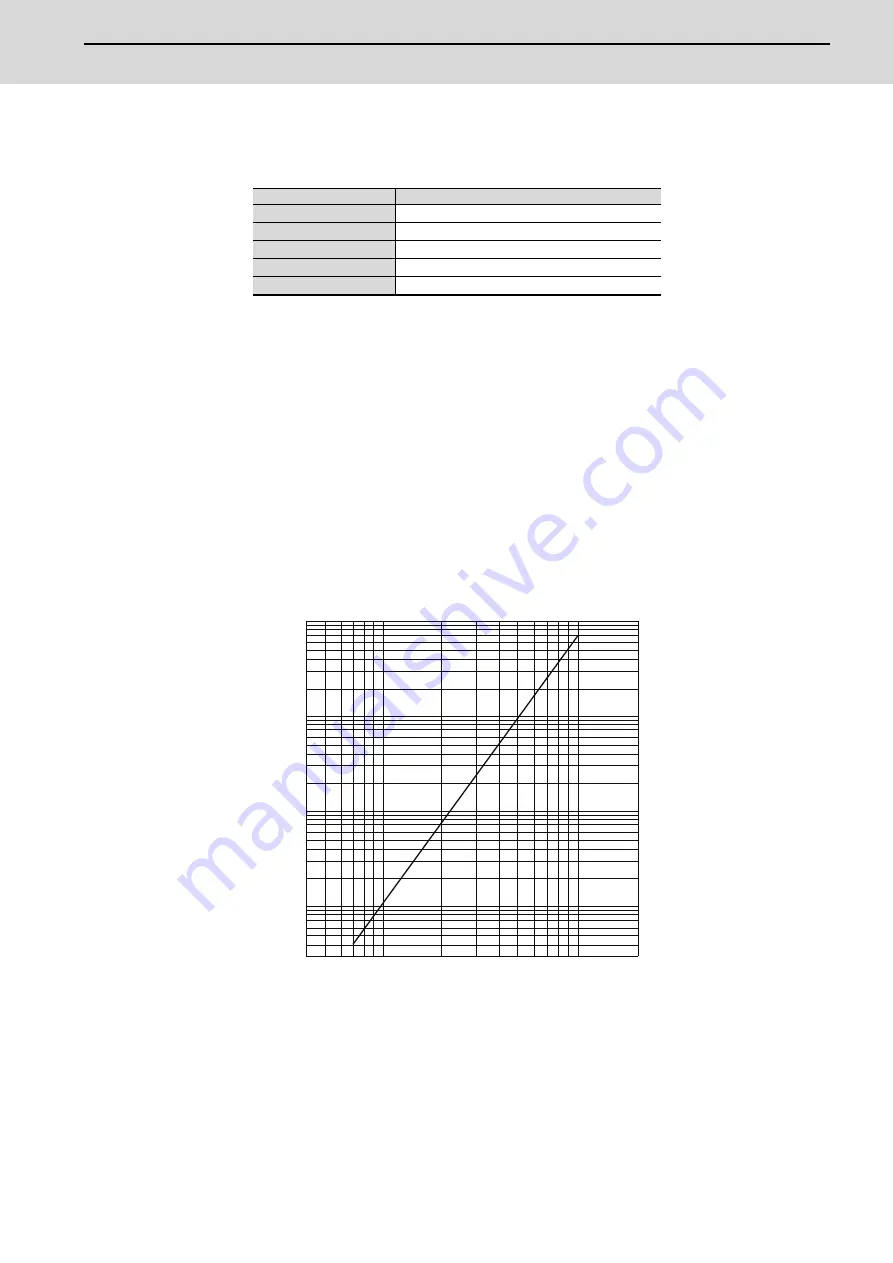
MDS-E/EH Series Instruction Manual
1 Installation
11
IB-1501229-F
1.1.9 Installation of Servo Motor
Mount the servo motor on a flange which has the following size or produces an equivalent or higher heat dissipation
effect:
(Note 1) These flange sizes are recommended dimensions when the flange material is an aluminum.
(Note 2) If enough flange size cannot be ensured, ensure the cooling performance by a cooling fan or operate the
motor in the state that the motor overheat alarm does not occur.
1.1.10 Cable Stress
[1] Sufficiently consider the cable clamping method so that bending stress and the stress from the cable's own weight
is not applied on the cable connection part.
[2] In applications where the servo motor moves, make sure that excessive stress is not applied on the cable.
If the encoder cable and servo motor wiring are stored in a cable bear and the servo motor moves, make sure that
the cable bending part is within the range of the optional encoder cable.
Fix the encoder cable and power cable enclosed with the servo motor.
[3] Make sure that the cable sheathes will not be cut by sharp cutting chips, worn or stepped on by workers or vehicles.
The bending life of the encoder cable is as shown below. Regard this with a slight allowance. If the servo motor/spindle
motor is installed on a machine that moves, make the bending radius as large as possible.
Flange size (mm)
Servo motor capacity
150×150×6
100W
250×250×6
200 to 400W
250×250×12
0.5 to 1.5kW
300×300×20
2.0 to 7.0kW
800×800×35
9.0 to 11.0kW
Encoder cable bending life
(Material of Mitsubishi optional encoder cable: A14B2343)
(Note) The values in this graph are calculated values and are not guaranteed.
4
7
10
20
40
70
100
200
1× 10
8
5× 10
7
2× 10
7
1× 10
7
5× 10
6
2× 10
6
1× 10
6
5× 10
5
2× 10
5
1× 10
5
5× 10
4
3× 10
4
Bending radius (mm)
No. of bends (times)
4
7
10
20
40
70
100
200
3 x 10
4
5 x 10
4
1 x 10
5
2 x 10
5
5 x 10
5
1 x 10
6
2 x 10
6
5 x 10
6
1 x 10
7
2 x 10
7
5 x 10
7
1 x 10
8
Summary of Contents for MDS-E
Page 1: ......
Page 3: ......
Page 15: ......
Page 17: ......
Page 19: ......
Page 21: ......
Page 31: ......
Page 32: ...1 IB 1501229 F 1 Installation ...
Page 76: ...45 IB 1501229 F 2 Wiring and Connection ...
Page 132: ...101 IB 1501229 F 3 Safety Function ...
Page 142: ...111 IB 1501229 F 4 Setup ...
Page 277: ...MDS E EH Series Instruction Manual 4 Setup 246 IB 1501229 F ...
Page 278: ...247 IB 1501229 F 5 Servo Adjustment ...
Page 351: ...MDS E EH Series Instruction Manual 5 Servo Adjustment 320 IB 1501229 F ...
Page 352: ...321 IB 1501229 F 6 Spindle Adjustment ...
Page 404: ...373 IB 1501229 F 7 Troubleshooting ...
Page 455: ...MDS E EH Series Instruction Manual 7 Troubleshooting 424 IB 1501229 F ...
Page 456: ...425 IB 1501229 F 8 Maintenance ...
Page 475: ...MDS E EH Series Instruction Manual 8 Maintenance 444 IB 1501229 F ...
Page 476: ...445 IB 1501229 F 9 Power Backup System ...
Page 494: ...463 IB 1501229 F 10 Appx 1 Cable and Connector Assembly ...
Page 504: ...473 IB 1501229 F 11 Appx 2 D A Output Specifications for Drive Unit ...
Page 514: ...483 IB 1501229 F 12 Appx 3 Protection Function ...
Page 523: ...MDS E EH Series Instruction Manual 12 Appx 3 Protection Function 492 IB 1501229 F ...
Page 524: ...493 IB 1501229 F 13 Appx 4 Compliance to EC Directives ...
Page 528: ...497 IB 1501229 F 14 Appx 5 EMC Installation Guidelines ...
Page 540: ...509 IB 1501229 F 15 Appx 6 Higher Harmonic Suppression Measure Guidelines ...
Page 550: ......
Page 554: ......