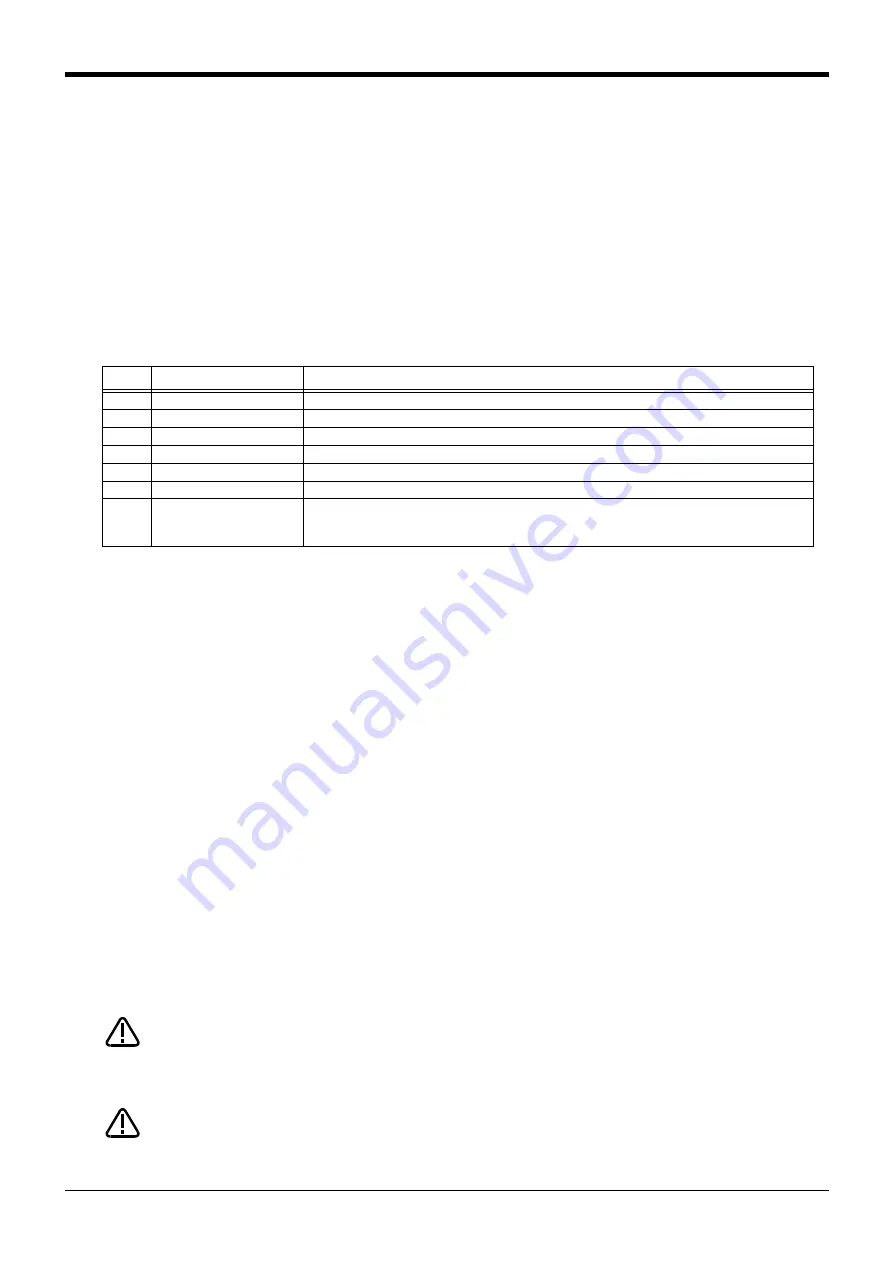
3 Controller
Emergency stop input and output etc. 3-50
3.6 Emergency stop input and output etc.
Do wiring of the external emergency stop, the special stop input, the door switch, and the enabling device from
the "special input/output" terminal connector.
Table 3-4 : Special input/output terminal
*At the time of the power supply OFF, the output point of contact is always open.
[Note] The contact capacity of each input/output terminal is DC24V/10mA - 500mA. Don't connect the
equipment except for this range. The use exceeding contact capacity causes failure.
Pin number assignment of each terminal and the circuit diagram are shown in
3.6.1 Connection of the external emergency stop
The external emergency stop input and door switch input and enabling device input are opened at shipment as
shown in
.
Connect the external emergency stop switch and door switch with the following procedure.
[Caution] Since the emergency stop circuit is made double circuits inside the controller, all the emergency stop
switches should use 2b-contact type. Remove the contact capacity sticker stuck on the connector
(EMGIN, EMGOUT, SKIP) and connect the emergency switch.
1) Prepare the "emergency stop switch", "enabling device" and "door switch".
2) Securely connect the external emergency stop's contacts across 3A-4A, 3B-4B, and the door switch's con
-
tacts across 8A-9A, 8B-9B, and the enabling device switch's contacts across 10A-11A, 10B-11B, on the
terminal block.
[Caution] When wiring the emergency stop switch (double emergency line type) and SKIP input signal, wire both
contacts to the two terminal blocks on the controller. If both contacts are wired to only one of the ter
-
minal blocks, errors cannot be cancelled using the door switch. The cable uses the shielded cable and
installs the ferrite core. Install the ferrite core in less than 30cm from the contact button.
Please be sure to check that each function operates normally for the prevention of
malfunction. Surely check that the operation of the emergency stop of the robot
controller, the emergency stop of the teaching pendant, the customer's emergency
stop, etc are normally.
Be sufficiently careful and wiring so that two or more emergency stop switches work
independently. Don't function only on AND conditions (Two or more emergency stop
switch status are all ON).
Note1) The level indicates the signal level.
L: Level signal → The designated function is validated when the signal is ON, and is invalidated when the sig
-
nal is OFF.
E: Edge signal → The designated function is validated when the signal changes from the OFF to ON state, and
the function maintains the original state even when the signal then turns OFF.
Note2) Four elements are set in the order of input signal start No., end No., output signal start No. and end No.
Note3) Up to eight points can be set successively in order of start output signal No. and end output signal No.
Item
Name
Function
Input
Emergency stop
Applies the emergency stop. Dual emergency line
Input
Special stop input
Applies the stop. (Refer to
Page 53, "3.6.2 Special stop input(SKIP)"
)
Input
Door switch
Servo-off. Dual line, normal close (
Page 55, "3.6.3 Door switch function"
)
Input
Enabling device
Servo-off. Dual line, normal close (
Page 55, "3.6.4 Enabling device function"
)
Output
Robot error output
Contactor is opening during error occurrence
Output
Mode output
MANUAL mode: contactor is closing, AUTO mode: contactor is opening
Output
Magnet contactor control
connector output for addi
-
tion axes
When an additional axis is used, the servo ON/OFF status of the additional axis can be synchronized
with the robot arm. (
Page 58, "3.8 Magnet contactor control connector output (AXMC) for addition
CAUTION
CAUTION