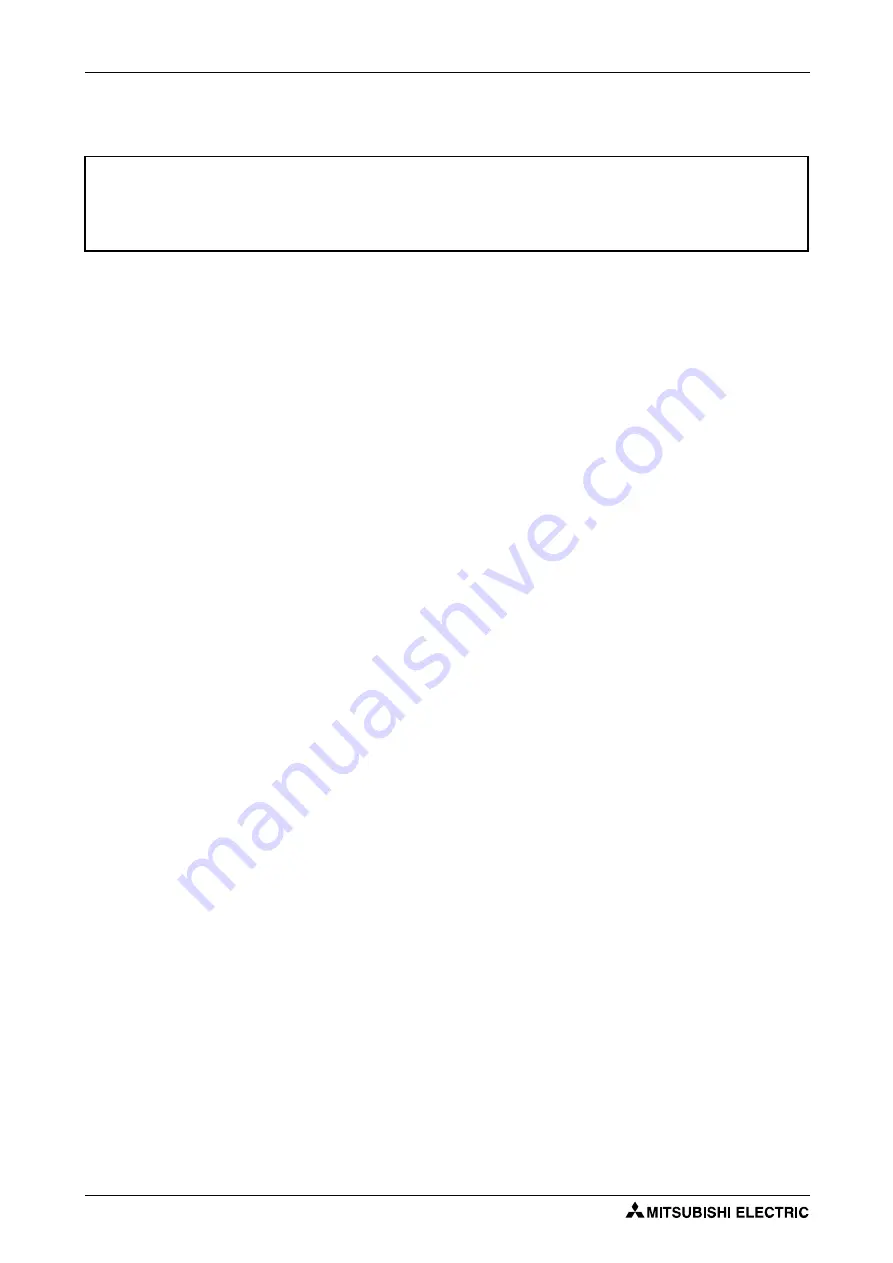
Instructions on maintenance
Troubleshooting and maintenance instructions
7 - 4
7.5 Instructions
on
maintenance
●
Use the "Maintenance Forecast" function of the RT ToolBox3 robot programming software to
determine the expected maintenance intervals.
●
Maintenance work should be carried on outside of the protective area when possible.
●
If the maintenance work has to be carried out from within the protective area then the power
supply must be switched off at the main switch and must be protected by a padlock against being
switched back on. However, switching off must never result in dangerous or hazardous states.
●
You must make sure that the daily and periodic inspections are carried out compliant to the
instructions in the technical manual. With regard to the robot system, the inspection and main-
tenance program of the manufacturer must be observed. If there is any special maintenance work
that can not be easily carried out by the user then you must contact the service providers of
MITSUBISHI ELECTRIC.
●
When carrying out maintenance work at the controller unit, also check the function of the cooling
fan, e.g. by making sure that there is an air current.
●
If the robot brakes are released then the robot arm (articulated arm robot) or the J3 axis (SCARA
robot) must be supported manually to ensure that they do not fall uncontrolled into the end stop.
You require the support of a second person for this.
●
Small amounts of grease may exit from the robot arm. If this can result in soiling or environmental
pollution then the robot should be checked regularly for loss of grease. If you determine that
grease is exiting at the robot then wipe it off from the surface with a cleaning cloth to ensure that
the floor and the vicinity around the robot are not soiled.
●
To be able to easily carry out maintenance work, make sure there is sufficient space and lighting.
●
The robot must not be retrofitted or changed using unauthorized parts. Only ever use original
spare parts and accessories. Parts and accessories not approved by the manufacturer must never
be used. Make sure that no safety functions can be modified.
●
Before switching back on the power supply, make sure that no dangerous or hazardous conditions
can be caused by this.
●
After completion of maintenance work, all safety equipment that has been temporarily deacti-
vated must be reactivated (e. g., door contact switch of the safety enclosure, etc).
●
Do not check the insulation resistor during maintenance work.
●
The batteries must not be shorted, charged, heated up, burnt or disassembled.
E
CAUTION:
All maintenance work on the robot must only be carried in full compliance to the following
safety directives!
Summary of Contents for MELFA RH-FRH-D
Page 2: ......
Page 4: ......
Page 6: ......
Page 16: ...Contents X ...
Page 22: ...Environmental conditions for operation Introduction 1 6 ...
Page 70: ...Grounding the robot system Installation 3 32 ...
Page 90: ...Teaching Box connection Connection 4 20 ...
Page 96: ...Switch on the robot system Startup 5 6 ...
Page 128: ...Dimensions Appendix A 18 ...
Page 130: ...A 20 Index Appendix ...
Page 131: ......
Page 132: ......
Page 133: ......
Page 134: ......
Page 135: ......
Page 136: ......
Page 137: ......
Page 138: ......
Page 139: ......
Page 140: ......
Page 141: ......
Page 142: ......
Page 143: ......
Page 144: ......
Page 145: ......
Page 146: ......
Page 147: ......
Page 148: ......
Page 149: ......
Page 150: ......
Page 151: ......
Page 152: ......
Page 153: ......
Page 154: ......
Page 155: ......
Page 156: ......
Page 157: ......
Page 158: ......
Page 159: ......
Page 160: ......
Page 161: ......
Page 162: ......
Page 163: ......
Page 164: ......
Page 165: ......