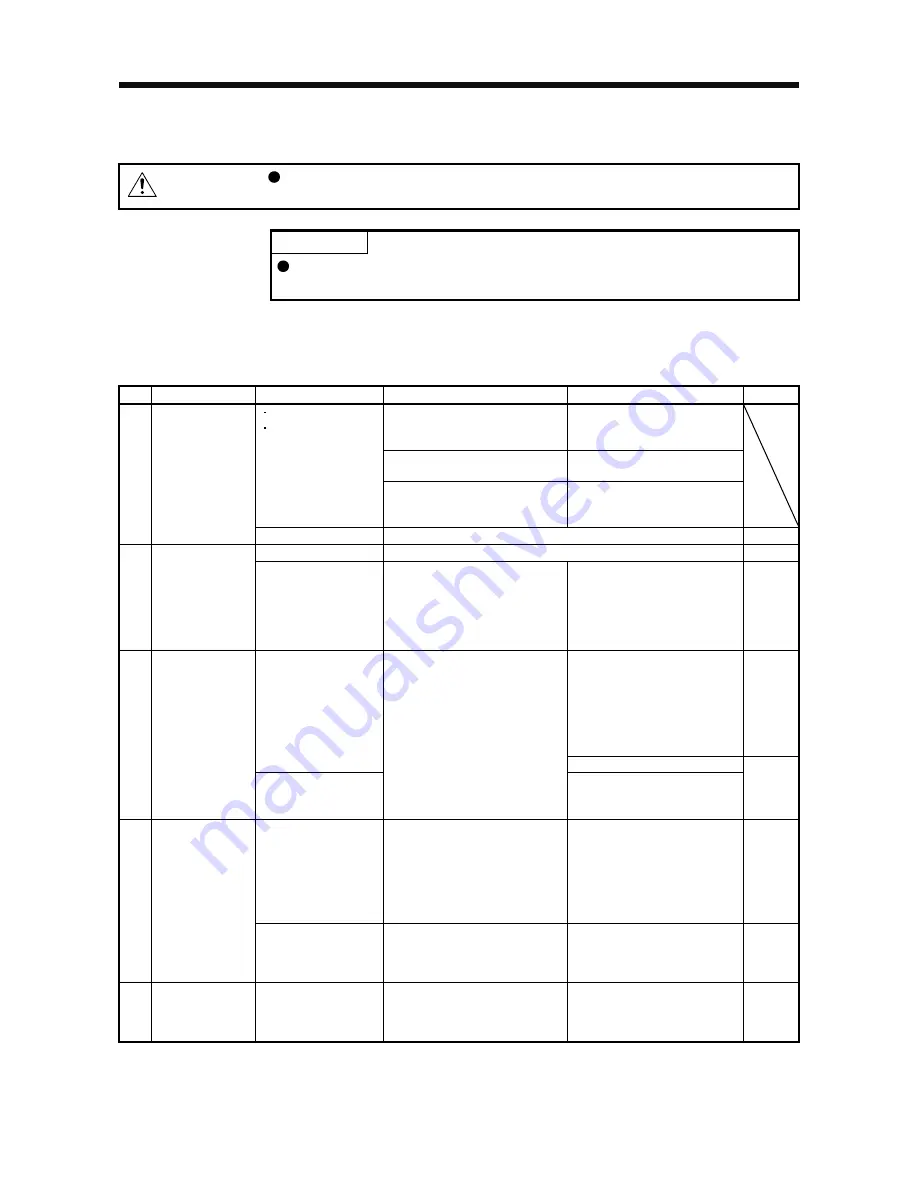
4. STARTUP
4 - 7
4.2.6 Trouble at start-up
CAUTION
Never make a drastic adjustment or change to the parameter values as doing so
will make the operation unstable.
POINT
Using the optional MR Configurator2, you can refer to reason for rotation failure,
etc.
The following faults may occur at start-up. If any of such faults occurs, take the corresponding action.
(1) Troubleshooting
No. Start-up sequence
Fault
Investigation
Possible cause
Reference
Not improved even if CN1 and
CN2 connectors are disconnected.
1. Power supply voltage fault
2. The servo amplifier is
malfunctioning.
Improved when CN1 connector is
disconnected.
Power supply of CN1 cabling is
shorted.
1
Power on
LED is not lit.
LED flickers.
Improved when CN2 connector is
disconnected.
1. Power supply of encoder
cabling is shorted.
2. Encoder is malfunctioning.
Alarm occurs.
Refer to chapter 8 and remove cause.
Chapter 8
2
Alarm occurs.
Refer to chapter 8 and remove cause.
Chapter 8
Switch on SON
(Servo-on).
Servo motor shaft is
not servo-locked.
(Servo motor shaft is
free.)
1. Check the display to see if the
servo amplifier is ready to
operate.
2. Check the external I/O signal
indication (section 4.5.7) to see
if SON (Servo-on) is on.
1. SON (Servo-on) is not input.
(wiring mistake)
2. 24 V DC power is not
supplied to DICOM.
Section
4.5.7
1. Wiring mistake
(a) For open collector pulse
train input, 24 V DC power
is not supplied to OPC.
(b) LSP and LSN are not on.
2. Pulse is not input from the
controller.
Section
4.5.3
Servo motor does not
rotate.
Mistake in setting of [Pr. PA13].
3
Input command
pulse (test
operation).
Servo motor run in
reverse direction.
Check the cumulative command
pulse on the status display
(section 4.5.3).
1. Mistake in wiring to controller.
2. Mistake in setting of [Pr.
PA14].
Chapter
5
Rotation ripples (speed
fluctuations) are large
at low speed.
Make gain adjustment in the
following procedure.
1. Increase the auto tuning
response level.
2. Repeat acceleration and
deceleration several times to
complete auto tuning.
Gain adjustment fault
Chapter
6
4
Gain adjustment
Large load inertia
moment causes the
servo motor shaft to
oscillate side to side.
If the servo motor may be driven
with safety, repeat acceleration
and deceleration several times to
complete auto tuning.
Gain adjustment fault
Chapter
6
5
Cyclic operation
Position shift occurs
Confirm the cumulative command
pulses, cumulative feedback
pulses and actual servo motor
position.
Pulse counting error, etc. due to
noise.
(2) of
this
section
Summary of Contents for MELSERVO-JE MR-JE-100A
Page 23: ...1 FUNCTIONS AND CONFIGURATION 1 12 MEMO ...
Page 29: ...2 INSTALLATION 2 6 MEMO ...
Page 91: ...3 SIGNALS AND WIRING 3 62 MEMO ...
Page 171: ...5 PARAMETERS 5 44 MEMO ...
Page 195: ...6 NORMAL GAIN ADJUSTMENT 6 24 MEMO ...
Page 221: ...7 SPECIAL ADJUSTMENT FUNCTIONS 7 26 MEMO ...
Page 249: ...8 TROUBLESHOOTING 8 28 MEMO ...
Page 255: ...9 DIMENSIONS 9 6 MEMO ...
Page 263: ...10 CHARACTERISTICS 10 8 MEMO ...
Page 293: ...11 OPTIONS AND PERIPHERAL EQUIPMENT 11 30 MEMO ...