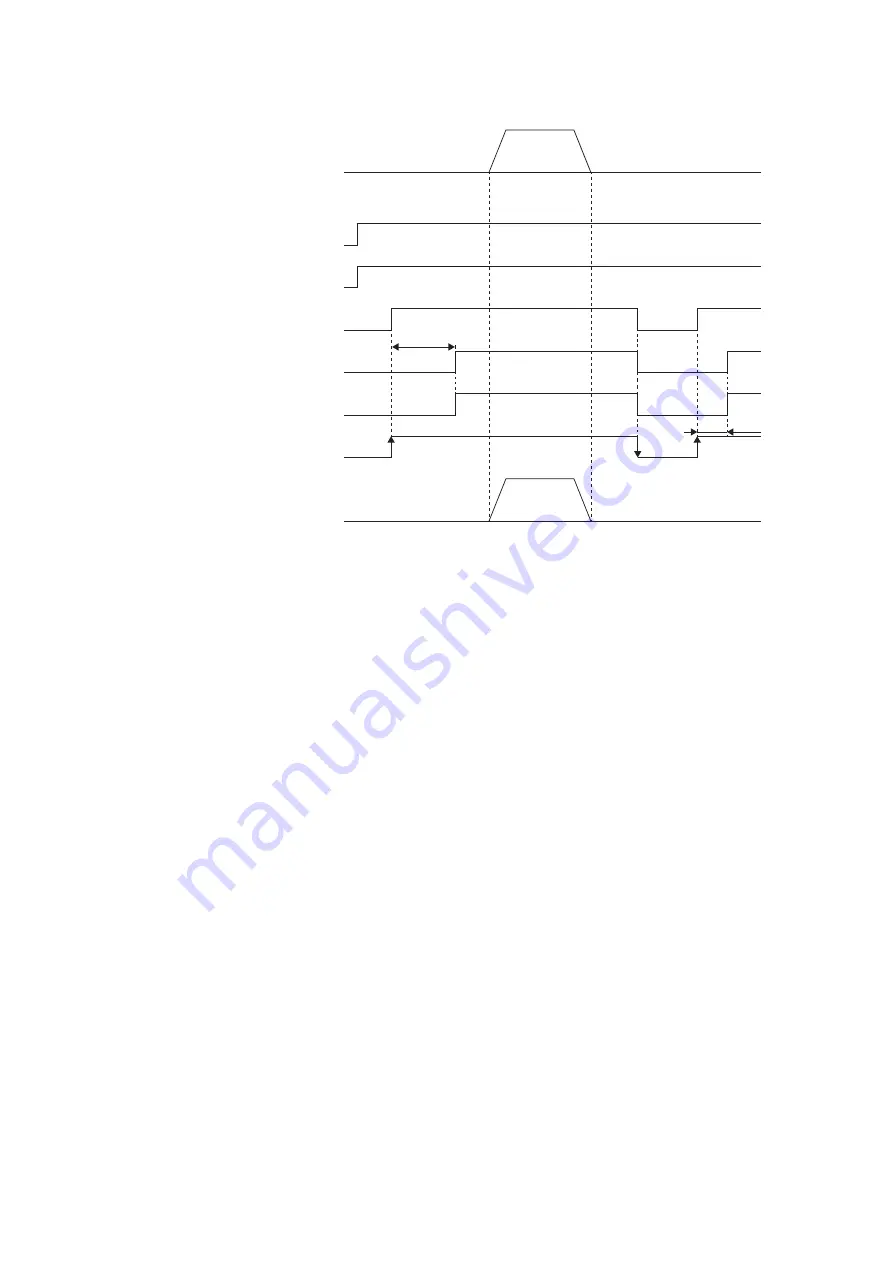
40
5 SIGNALS AND WIRING
5.2 Explanation of power supply system
• When the magnetic contactor drive output is enabled and returns to ready-off
When in ready-off, the magnetic contactor of the converter unit is turned off and the main circuit power supply is shut off.
*1 If an electromagnetic brake is installed externally, configure the circuit so that the electromagnetic brake operates with MBR as
described below.
ON: Electromagnetic brake is not activated
OFF: Electromagnetic brake is activated
*2 Give a position command after the externally-installed electromagnetic brake is released.
*3 When in the position control mode.
(3 s)
(3 s)
*2
OFF
ON
OFF
ON
OFF
ON
OFF
ON
OFF
ON
ON
OFF
0 r/min
0 r/min
Main circuit power supply
Base circuit
Drive unit
control circuit power supply
MBR
(Electromagnetic brake interlock)
*1
Position command
*3
Servo motor speed
Converter unit control circuit power supply
Servo-on command (From the controller)