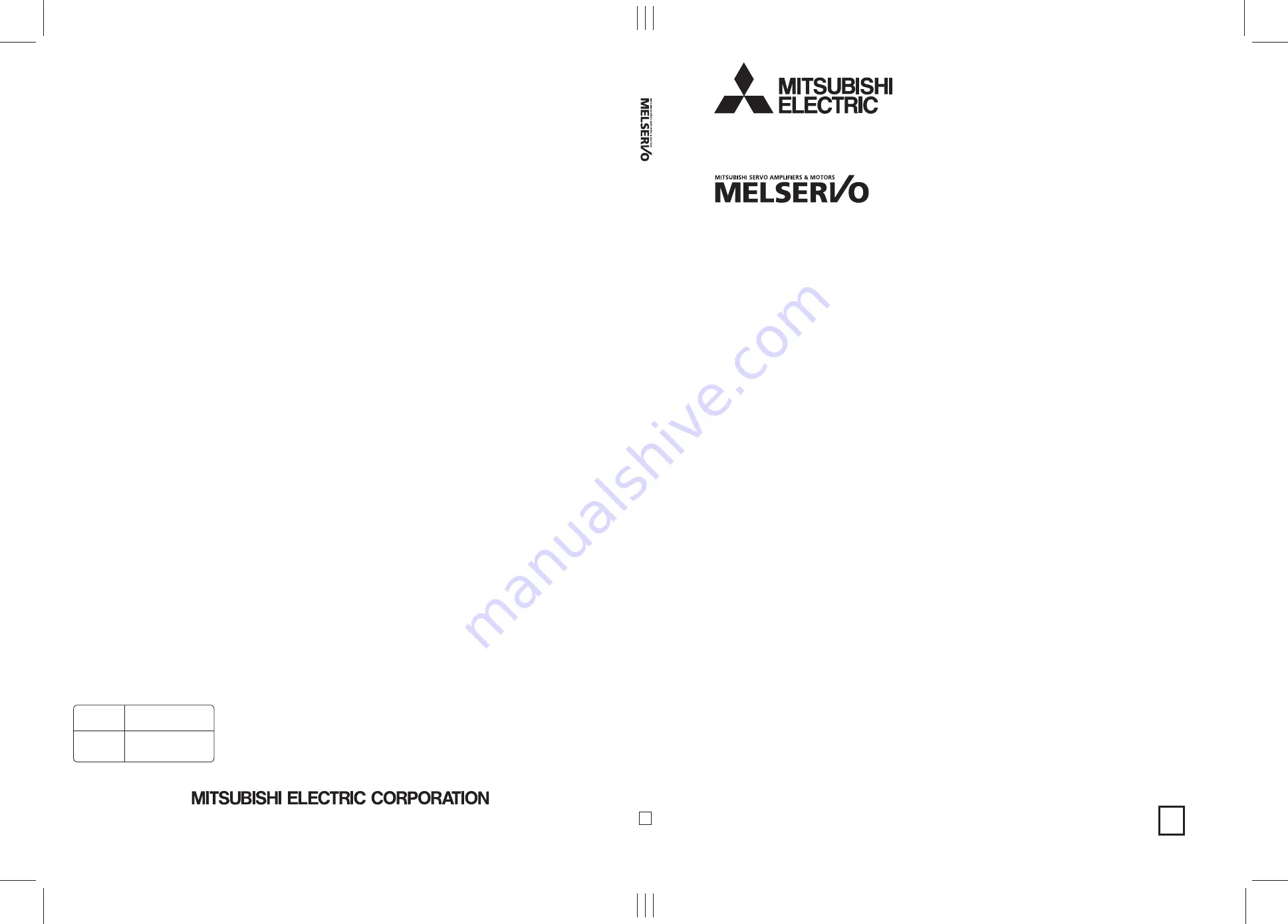
SH(NA)030132ENG-E(1805)MEE Printed in Japan
Specifications are subject to change without notice.
This Instruction Manual uses recycled paper.
MODEL
MODEL
CODE
General-Purpose AC Servo
MR-D30 INSTRUCTION MANUAL
HEAD OFFICE: TOKYO BLDG MARUNOUCHI TOKYO 100-8310
1CW817
MR-D30 INSTRUCTIONMANUAL
Functional safety unit
MODEL
MR-D30
INSTRUCTION MANUAL
E
E
Summary of Contents for MR-D30
Page 13: ...4 MEMO ...
Page 41: ...1 FUNCTIONS AND CONFIGURATION 1 28 MEMO ...
Page 141: ...6 DISPLAY 6 2 MEMO ...
Page 153: ...MEMO ...