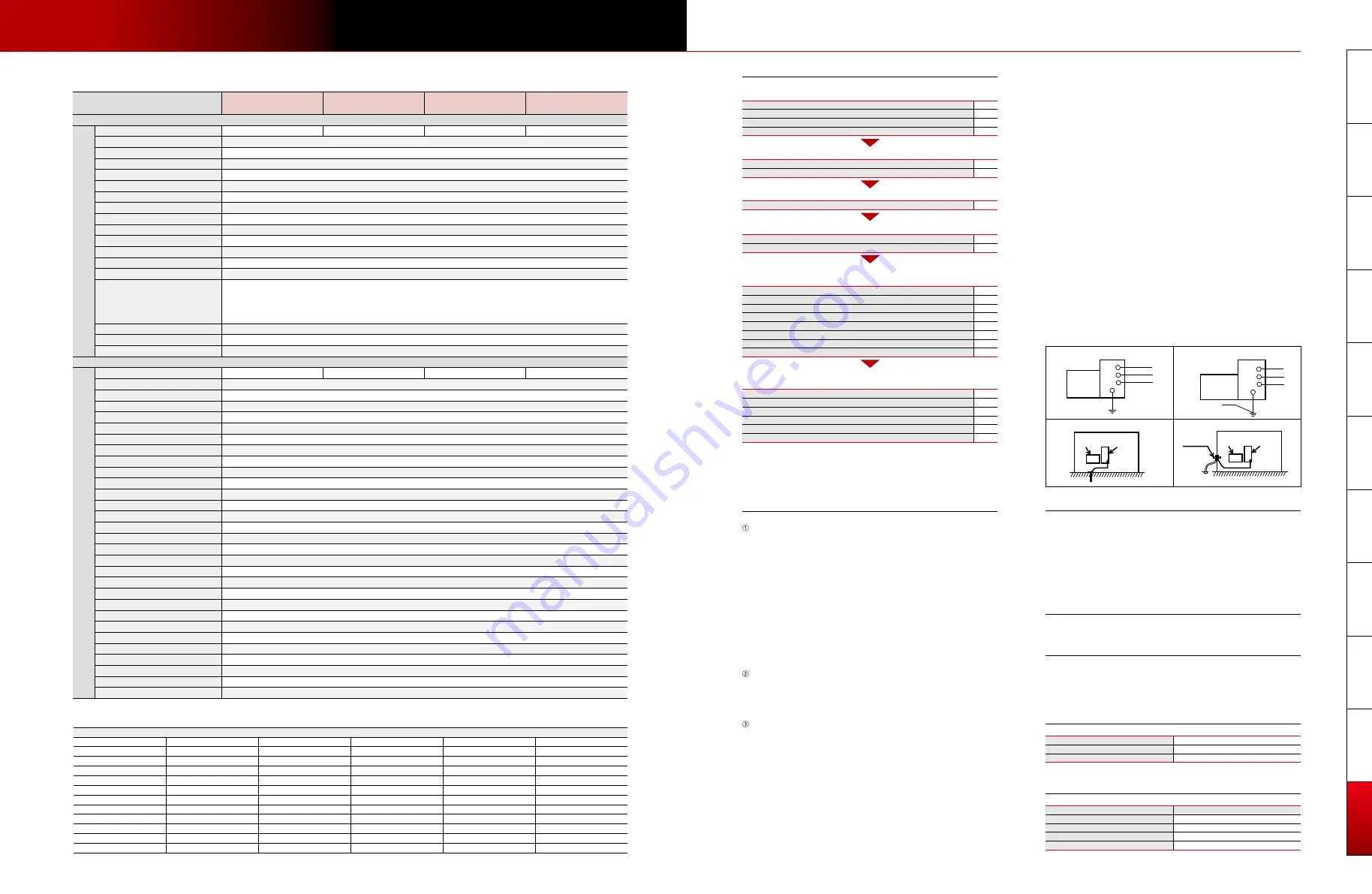
Power Supply, Control Specifications/Machine Installation
OB-PN
HBZ-U (N)
SBS-HN
Oki Electric Cable
Hitachi Cable
Sumiden Fine Conductors
Product Line-up
Functions and
F
eatures
Intelligent A
T
Opt Dr
iv
e System
Long Lif
e System
Pow
er Supply
, Control Specifications
Machine Installation
Machining Samples
Precise Finish Circuit
Natur
al User Interf
ace
AD
VANCE PLUS control
Options
23
24
Control unit functions
Power-supply/Control unit specifications
Year, month, date display
Overlap window function
Character string replacement function
Geometric function
Floating decimal point function
Control command
Corner R
Corner chamfer
Linear angle command
30-sec. short-circuit stop
Simultaneous 2-axis wire alignment
Workpiece inclination compensation
Reference block
Single block
Dry run
Automatic return
User macro
Automatic positioning (hole center, edge)
Automatic zero point return
Machining start hole return
Memory operation 1GB
Program edit
Coordinate rotation
Pattern rotation
Program no. designation
Expanded AT function
Graphics (drawing monitor)
Graphics (program check)
Graphics (automatic machining shape drawing)
Graphics (surface display)
Offset
Coordinate reading
Time reading
XY-axis independent scaling
Axis rotation
Automatic 2nd cut
Machining condition search
Block delete
USB flash memory
e-manual (electronic instruction manual)
Repeated positioning
Automatic power failure recovery
Workpiece coordinate system (106 items)
PM control
SL control
3D graphic check
Workpiece alignment
Axis exchange
Mirror image
Circumference calculation
Backlash compensation
Pitch error compensation
Soft limit (inside/outside prohibit)
Wire consumption estimate
CM3 control
OM control
3D viewer (Parasolid data display)
Sleep mode (MV-R)
Maintenance check
Automatic taper degree calculation
Status recording
Data variable operation
Alarm display
Machining time estimate
Built-in 2D-CAD/CAM
Built-in 3D-CAM
EM control
3D model compatible PM control (3D-PM)
Digital-AE
@
Control unit specifications
Compatible model
Power supply unit specifications
P
ow
er-supply unit
Control unit
Regenerative transistor pulse type
Completely sealed/Indirect cooling
All modes
50A
9 types : Anti-electrolysis power supply
16 types
440 types
32 types
10 types
20 types
7 types
5 types
2 types
3 notches (changeable with M code or screen)
• Workpiece material: Steel, tungsten, copper, aluminum
• Applicable only for rough-cut conditions
Built-in
600 × 650 × 1765
(23.6 × 25.6 × 69.5)
240
(529)
Model
Power-supply circuit
Cooling method
Anti-electrolytic power supply
Maximum output current
Power-supply mode
Machine voltage selection
Machining setting
OFF time
Stabilization circuit A
Stabilization circuit B
Stabilization circuit C
Stabilization circuit E
FM circuit (LA, LC)
PM control
AVR
Unit dimensions (mm)
(in)
Unit weight (kg)
(lb)
Keyboard, USB flash memory, Ethernet
Touch panel, mouse
15" color TFT
Alphanumeric characters
CNC closed loop
Max. 4 axes simultaneously
X, Y, U, V, Z … 1/0.1µm
50nm (0.000050mm
(0.000002")
)
±99999.999mm
Combined use of increment/absolute values
Linear, circular, and spiral
0.00001 ~ 99.999999 (G code) 0.001 ~ 9999.999 (S code)
Automatic selection of machining speed according to gap voltage sensing
Reverse path retrace during short-circuit
±99999.999mm Offset numbers: 1 to 900 (intersection point calculation)
5 types (file, setup, machining support, monitor, maintenance)
Interactive screen method
1 to 6999
1 to 99999999
Nesting level 30
1 to 99999
Input on screen
High-speed, medium-speed, low-speed, ultra-slow speed, inching (0.0001mm/0.0005mm/0.0001mm) Positioning function, AT function
XY plane, XY-XZ plane, solid, table scaling, 3D model display, background drawing, automatic machining path drawing
1GB
Management of consumable parts (time display)
SL, CM, EM, OM, PM, BM
494 × 175 × 346
(19.4 × 6.9 × 13.6)
(excluding keyboard and mouse pad)
20
(44)
Model
NC program input method
Pointing device
Display
Display characters
Control method
Number of control axes
Setting unit
Minimum driving unit (mm)
(in)
Max. command value
Position command format
Interpolation function
Scale magnification
Optimum feed control
Path-retrace control
Wire offset
Basic screen menu
Automatic 2nd cut
Machining condition (E-pack) storage
Program number command
Sub-program
Sequence numbers
Manual input positioning
Manual operation box
Graphics
User memory capacity
Maintenance function
Adaptive control
External dimensions (mm)
(in)
Weight (kg)
(lb)
W31 (Advance control unit) Control Unit Functions
* Air (compressed air) is used to operate the automatic wire feeder and work tank door, etc. Air
supplied from a normal compressor contains various impurities that could cause operation faults if
they get into the pneumatic devices such as the solenoid valve. Install an air filter with a drainage
discharge mechanism, etc., in the air source (primary source) piping to prevent impurities from
entering the pneumatic devices.
Machine Installation Checklist
Determining the machining details
Installation Conditions
1) Determine the workpiece
2) Determine the machining site
3) Determine the pre-processing site
4) Determine the post-processing site
Confirmation of foundation and power-supply work
If there is any possibility of radio disturbance, investigate it prior to starting work.
1) Confirmation of floor area
2) Confirmation of environment (constant pressure, dust-proof room, measure for radio disturbance, prevention of external noise)
3) Confirmation of foundation floor
4) Foundation work
5) Primary wiring for power lead-in
6) Grounding work
7) Construction of dielectric fluid (city water) supply/drainage facilities
8) Air piping work
Confirmation of delivery path
1) Traffic restrictions to factory
Road width
Entry road
2) Factory entrance and width of gate in factory
m
Factory building entrance dimensions (height × width)
m × m
3) Constant-temperature, dust-proof room entrance dimensions (height × width)
m × m
Preparation of installation fixtures
1) Plan the installation fixtures
2) Prepare or manufacture the fixtures
1) Select the programmers and operators
2) Apply for training seminars
Preparation of consumable parts
1) Purchase consumable parts such as wire electrodes
Training of programmers and operators
Cautions
The standard delivery entrance dimensions for standard shipment delivery are given on the product
introduction page. If the entrance is smaller than the standard delivery entrance, the machine shipped
may have different dimensions.
Contact a Mitsubishi Electric sales office for details (a separate estimate will be issued).
Note that delivery may not be possible in some cases depending on the dimensions.
Precautions for Selecting Earth Leakage Breaker
To prevent malfunctions caused by the external noise from control units, etc., a filter
is installed for the power-supply input. By grounding one end of this filter, an earth
leakage current of approx. 30mA to 40mA passes through the filter. A highly sensitive
earth leakage breaker (sensitivity current 30mA) could malfunction. Thus, a
medium-sensitivity earth leakage breaker (sensitivity current 100mA to 200mA) is
recommended for the EDM. Class C grounding (grounding resistance of 10
Ω
or less)
is recommended for the wire-cut EDM. Even if the sensitivity current is 200mA, the
contact voltage will be 2V or less, and no problems will occur in preventing electric
shock (application of tolerable contact current Class 2, 25V or less).
Harmonic Distortion
If there is harmonic distortion in the power supply, the machine operation could be
affected even if the voltage does not fluctuate. In addition, the harmonic current could
flow from the wire-cut EDM to the power system and adversely affect peripheral
devices. If the effect of the harmonic distortion causes problems, install a harmonic
suppression filter or take other measures.
Disposal
The dielectric fluid, dielectric fluid filter, ion exchange resin, wire, etc., are industrial
waste. These must be disposed of following national and local laws and ordinances.
1. Installation site
Constant-temperature, dust-proof room
· Recommended room temperature 20±1°C
(68°F±2)
· Usable temperature range 5 to 35°C
(44°F to 95°F)
Temperature fluctuation will directly affect machine accuracy. To maintain
performance accuracy, select a place with minimal temperature fluctuation.
Install the EDM in a constant-temperature room when performing high precision
machining, even when using skim cuts.
Note that an environment where the temperature fluctuates by 3°C
(5°F)
or more
within 24 hours, or 1°C
(2°F)
or more within one hour can adversely affect
machining accuracy. Make sure that the machine body is not subject to direct
wind from air-conditioners or to direct sunlight.
· Dust-free location is recommended.
Grinding dust can adversely affect the machine's linear scales and ball screws.
Pay special attention to installation location to avoid this hazard (separate from
grinding machine, or install in separate room, etc.).
· Humidity Within 30 to 75%RH (with no dew condensation).
· Temperature range during transportation and storage
-25 to 55°C
(13°F to 131°F)
(when power is not connected).
Tolerable vibration of floor
· Select an floor where vibration or impact will not be conveyed.
· As a reference, the vibration level should have a max. amplitude of 2µm or less at
a 10 to 20Hz frequency.
· Consult with the contractor or vibration measuring instrument maker for details on
the measuring method.
Foundation
· The floor should be concrete with a thickness of 400mm
(15.7")
or more so it can
sufficiently withstand the system’s weight.
· The floor inclination (step) must be within 6/1000 (floor inclination 6mm per 1m)
(MV2400 Series).
2. Machine heating
• Approx. 8,140W of heat is generated per machine, of which 1,512W is heat
generated by the dielectric fluid control unit.
• Take this into consideration when studying air-conditioning requirements.
3. Power-supply equipment
• Primary wiring 3-phase 200/220VAC±10% 50/60Hz±1Hz
• Power capacity
10.0kVA (during normal use) (when using
Ø
0.2
(.008")
mm wire electrode)
13.5kVA (when using the maximum)
* Use a 14mm
2
or thicker cable for the primary connection.
4. Grounding work
Wire-cut EDMs must always be grounded to prevent external noise, radio
disturbance and earth leakage.
Class C grounding (grounding resistance of 10
Ω
or less) as set forth in the
Electric Facility Standards is recommended for Mitsubishi Electric EDMs.
· Class C grounding (isolated) is recommended (Wire-cut EDM dedicated
grounding) (Fig. 1).
Note) Provide isolated grounding for each machine.
· Common grounding can be used if noise from other devices will not enter through
the common grounding; the grounding cable must be connected independently to
the grounding location (Fig. 2).
· Use a 14mm
2
grounding wire.
5. Primary air equipment
• Hose diameter : 1/4 hose (hose sleeve outer diameter: ø9.0
(0.35")
)
• Pressure : 0.5 to 0.7MPa
(70 to 100psi)
• Flow rate : 75L/min or more
(26cu.ft./min.)
6. Shield room
Install a shield room if a wire-cut EDM affects televisions or other communication
facilities in the area. Observe the following points when installing the wire-cut
EDM in the shield room.
1. Ground the EDM in the shield room (Fig. 3).
2. If the EDM cannot be grounded in the shield room, connect the wire-cut EDM's
grounding cable to the shield room's grounding terminal (through bolt) as shown
in Fig. 4.
3. Consult with with a Mitsubishi Electric representative for details on installing a
shield room.
Power-supply unit
Machine body R
S
T
E
Power-supply unit
Machine body
Grounding cable
for other device
R
S
T
E
Shield room
Machine
body
Power-supply
unit
Shield room
Through
bolt
Within 1m
Machine
body
Power-supply
unit
Fig. 1
Fig. 2
Fig. 3
Fig. 4
Check each item, and make sure that no item or order is overlooked.
Check the path inside and outside the factory to avoid any trouble during delivery.
Wire electrodes
*Wire electrodes above do not guarantee performances.
Recommended sliding surface lubricants
Maker
Exxon Mobil
Idemitsu Kosan
Showa Shell
JX Nippon Oil & Energy Corporation
Product name
Mobil DTE26
Super Hydro 68A
Terrace Oil 68
Super Mulpas DX68
Use the following wire electrodes
Use one of the following lubricants for sliding surface
As of February 2012
MV1200S
MV2400S
WMV(S)
MV1200R
WMV(R)
WMV(S)
MV2400R
WMV(R)
W31MV-2(S)
W31MV-2(R)
W31MV-2(S)
W31MV-2(R)