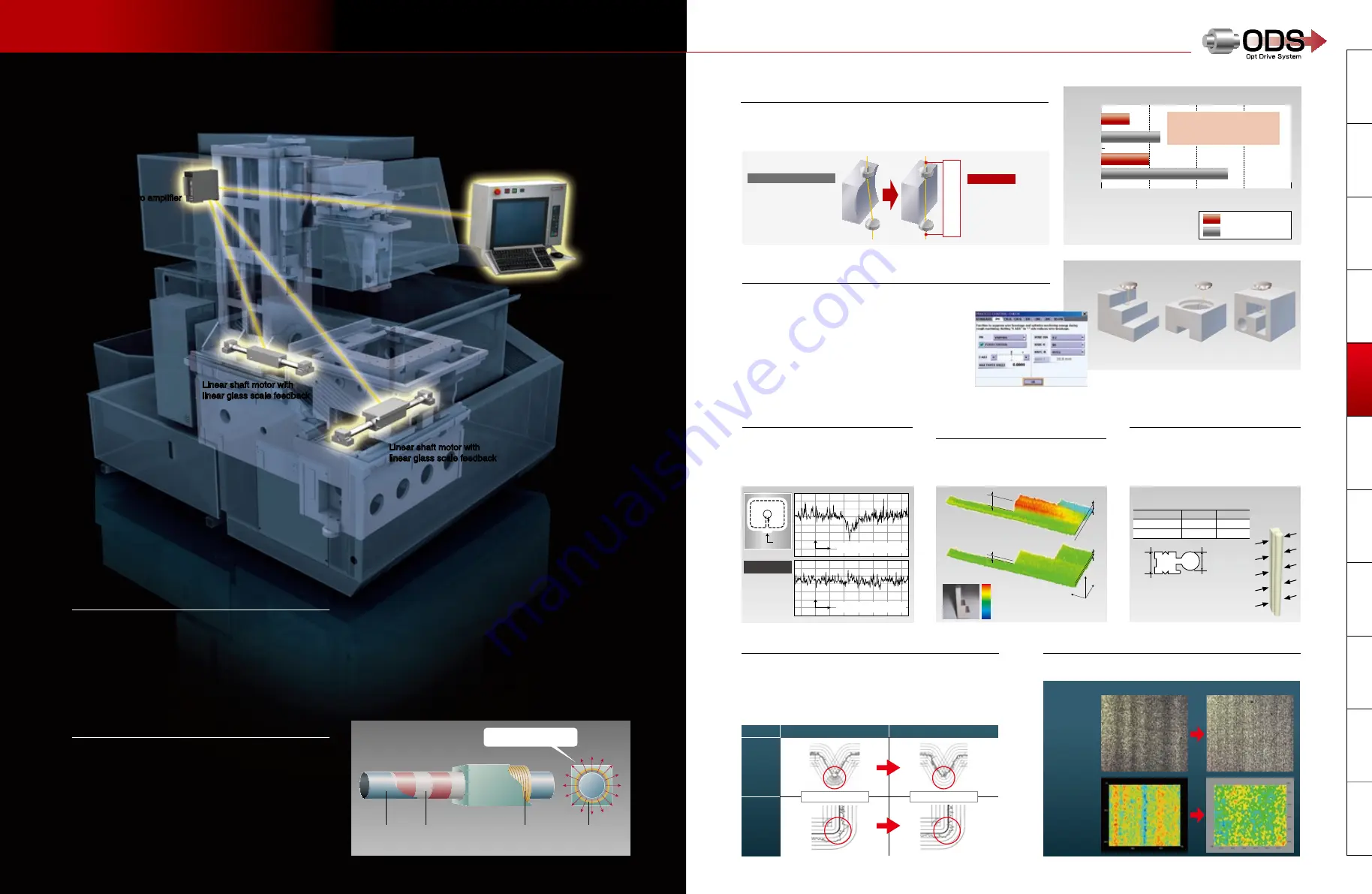
Opt Drive System
Improved machining accuracy
Corner machining control
(CM3 control: Corner Master3)
Optical Drive System
●
High-speed fiber-optic communications and a linear shaft
motor synergistically improve machining accuracy
●
A servo amplifier and control unit developed by Mitsubishi
Electric contribute to system optimization
Shape control power supply
(Digital-AE
@
)
●
Wire straightness is digitally controlled with the world's only
electrical-discharge position control
(As of Mar. '12)
●
Total machining time is reduced by improving straightness accuracy during
rough, intermediate and finishing processes
Next-generation drive system and refined power-supply control technology
Linear Shaft Motor
●
Power consumption is reduced by utilizing a full 360°
magnetic flux as the effective driving force
●
Highly accurate axis movement is possible without any
backlash
●
Non contact power transmission ensures stable and
accurate axis movement for many years
Magnet
Magnetic flux
N
S
N
N
N
S
Utilizes all magnetic flux
as an effective driving force.
Shaft
Magnet
Coil
Coil
Adaptive control setting screen
Product Line-up
Functions and
F
eatures
Intelligent A
T
Opt Dr
iv
e System
Long Lif
e System
Pow
er Supply
, Control Specifications
Machine Installation
Machining Samples
Precise Finish Circuit
Natur
al User Interf
ace
AD
VANCE PLUS control
Options
11
12
Servo amplifier
Servo amplifier
ADVANCE control unit
ADVANCE control unit
Linear shaft motor with
linear glass scale feedback
Linear shaft motor with
linear glass scale feedback
Linear shaft motor with
linear glass scale feedback
Linear shaft motor with
linear glass scale feedback
0
5
10
15
20
100mmt
200mmt
Straightness accuracy (both sides) µm
Workpiece: Steel
No. of cuts: 5
Electrode material: ø0.25mm
(.010")
Conventional model
Digital-AE
@
Comparison of straightness accuracy during finish machining
Conventional technology
Shape control po
w
er supply
Compared to conventional Mitsubishi Electric
Wire-cut EDM (FA Series)
Stepped shape
machining
Stepped shape
machining
Cross-cavity shape
machining
Examples of PM machining applications
Dimple
Example of corner
machining
Wire electrode :
ø0.2
(.008")
/BS
Workpiece :
Steel, t20mm
(.79")
Surface roughness :
Rz3.9µm
2µm
250µm
2µm
250µm
EM control: concave section depth
within surface roughness
No control: concave section depth
approx. 4µm
Conventional control:
Step, straightness -3µm to +7µm
(-.0001 to +.0003")
7µm
(.0003")
3µm
(.0001")
1µm
(.00004")
2µm
(.00008")
SL control:
Step, straig2µm
(+.00008")
or less
7.0µm
(.0003")
-7.0µm
(-.0003")
Wire electrode: ø0.2
(.008")
/BS
Workpiece: Steel(SKD11),t60mm
(2.4")
No. of cuts,
surface roughness: 6, Rz1.7µm
Comparison of straightness
B:4mm
(.16")
A:5mm
(.20")
Section A
Section B
3µm
(.0001")
3µm
(.0001")
3µm
(.0001")
5µm
(.0002")
Using OM control
Without OM control
(Both sides)
Under-cut (dimple) reduction control
(EM control: Entrance Master)
●
Reduces dimples at the approach section
●
Allows shape adjustment from convex to
concave
●
Greatly reduces polishing time
Machining surface step/
straightness control
(SL control: Stepless control)
●
Greatly improves the step finish and wall
straightness for workpieces with varying
thicknesses
●
Highly accurate finishing of complicated parts
Dimensional error control
(OM control: Orbit Master)
●
OM control is designed to attain a
uniform electrical-discharge gap
regardless of the corner shape
●
This improves the radial shape error and
greatly improves the total part accuracy
Fully-automatic rough machining control
(PM control: Power Master)
●
No need to set machining conditions or have knowledge of EDM machining
●
Automatically recognizes machining conditions and makes adjustments for
the optimum machining condition
<3D-PM>
●
Analyzes 3D data and recognizes shape characteristics
●
Eliminates transition lines which appear easily in
stepped machining areas
●
Improves machining speed with nozzle closing conditions
Die-shaped machining samples Comparison of corner accuracies
Conventional tension control
TS master
Conventional corner control
CM3
(R0.2mm)
(.008")
(R0.15mm)
(.006")
Shape error: 2 to 3µm
Shape error: 1µm
In-corner
60˚
In-corner
90˚
Machined surface
after polishing
Analysis of
machined surface
before polishing
●
Improves machining accuracy at extremely small in-corners
and out-corners
●
Realizes highly accurate shape machining even for
complicated geometries with several types and sizes of corners
●
Corner accuracy is easily controlled by the operator
Wire tension control
(TS Master)
●
Suppresses tension fluctuation for more stable machining
●
Suppresses lines on the machined surface after polishing
Digital-AE
@
Discharge rate relative to
workpiece thickness is
monitored by
electrical-discharge position
control
• Machining conditions are
optimized
• Number of cuts are increased
• Upper/lower dimension
difference is compensated
mechanically (taper angle)