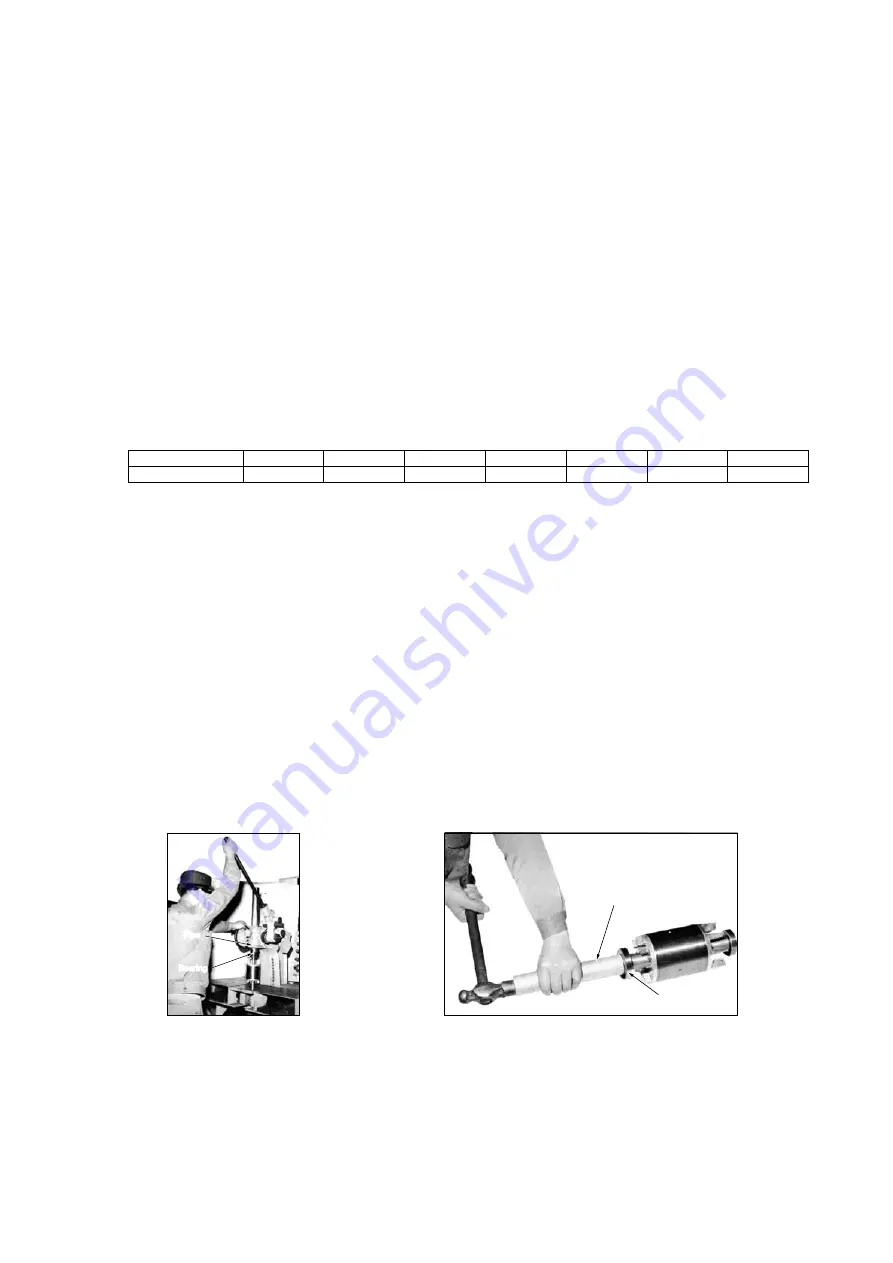
– 18 –
d. Outdoor type motor
(a) Before reassembling, apply a sealing agent (ThreeBond 1102D or the like) to the frame fitting surface of the
bracket.
(b) When the flinger, water flinger and V-ring will be fitted to the shaft through hole, apply a thin layer of
grease (Alvania S2 or the like) to the bracket surface. Take care not to stain the shaft with grease or oil.
The mounting dimensions of the flinger and water flinger shall be identical with those before disassembly.
(Normally, the gap between the flinger and bracket shall be 0.3 to 0.5mm, and that between the water flinger
and bracket shall be 1 to 1.5mm.) Bring the V-ring into slight contact with the bracket. After fitting them, turn
the shaft by hand, and check for abnormal noise and non-smooth rotation.
e. When open bearings are used
When installing the housing cover and bracket, check the grease port in the housing cover and the oil supply
and drain ports in the bracket, and ensure that they are located in the same positions as before disassembly.
f. Totally-enclosed fan-cooled motor
When installing the fan, apply grease (Alvania S2 or the like) to the shaft mounting surface. (So, the fan can be
removed easily next time.) Apply a screw locking agent (ThreeBond 1401B or the like) to the setscrews of the fan
before tightening.
g. Tightening of screws
Tighten the screws to the tightening torques shown in Table 15. To install the frame bracket of motor of frame
size 132 or below, fit the clamping bolts (through bolts) perpendicularly to the fitting surface.
Table 15 Screw tightening torque standard (iron)
Screw size
M4
M5
M6
M8
M10
M12
M16
Torque (N·m)
1.65
3.2
5.5
13.2
26.5
46
110
(Note) Except tapping screws
(2) Installation of bearings
When assembling the bearings onto the shaft, clean the fitting section of the bearings, remove any scratches and
protrusions, and hen fit with the following method.
a. Installation of a shielded ball bearing
(a) Apply oil on the bore diameter of the bearing and the fitting face of the shaft, and press the bearing squarely
onto the shaft by placing a suitable piece of pipe against the inner ring and carefully pressing with a press
as shown in Fig. 11. If a press is not available, tap the bearing lightly and slowly lower it as shown in Fig. 12.
In this case,
take not to pry the bearing or to contact the pipe against the bearing retainer seal or outer
ring section.
(b) When heating the bearing with a heater or oven before insertion, heat the bearing to approx. 90°C (
take care
not to exceed 100°C), and then fit it onto the shaft. When mounting onto the shaft, always wear protective
equipment to prevent burns, etc.
(c) After fitting the bearing onto the shaft, check visually and with a thickness gauge that there is no gap between
the shaft and bearing.
(d) If the lock nut is tightened or the bearing is mounted on the bracket before the bearing cools down, the
bearing may be wrenched. Reassemble after the bearing sufficiently cools down.
Pipe
Bearing
(Nagoya Works B750058-1)
Fig. 12 Installation of the bearing with a hammer
Pipe
Bearing
(Nagoya Works B750058-3)
Fig. 11 Installation of the bearing with a press