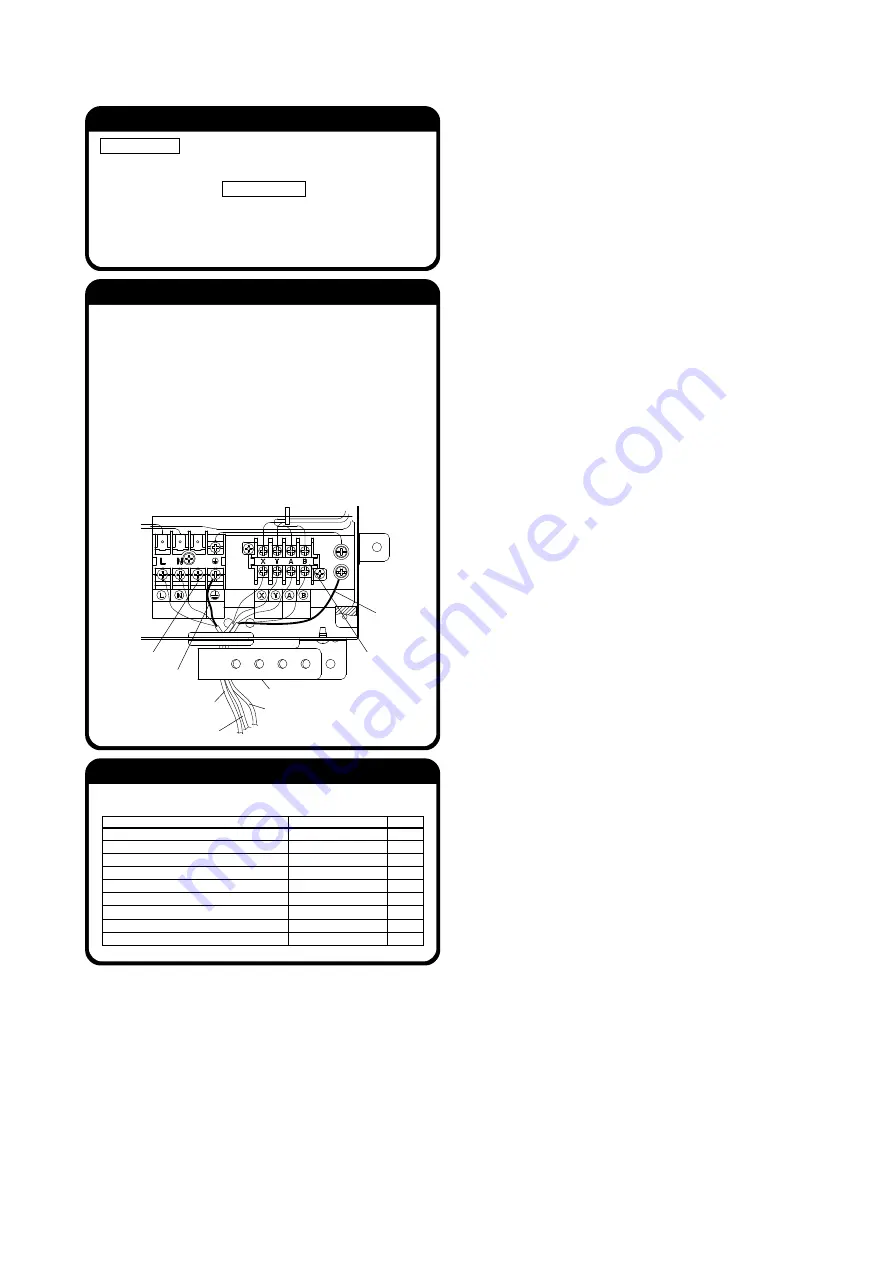
-
159
-
PJC012D013
⑤
Duck Work (continued)
⑦
Drain pipe (continued)
⑥
Refrigerant pipe
⑦
Drain pipe
Caution
●
Use the new refrigerant pipe.
When re-using the existing pipe system for R22 or R407C, pay attention to the following items.
・
Change the flare nuts with the attached ones (JIS category 2), and reprocess the flare parts.
・
Do not use thin-walled pipes.
●
Use phosphorus deoxidized copper alloy seamless pipe (C1220T specified in JIS H3300) for refrigeration pipe installation.
In addition, make sure there is no damage both inside and outside of the pipe, and no harmful
substances such as sulfur, oxide, dust or a contaminant stuck on the pipes.
●
Do not use any refrigerant other than R410A.
Using other refrigerant except R410A (R22 etc.) may degrade inside refrigeration oil. And air
getting into refrigeration circuit may cause over-pressure and resultant it may result in bursting, etc.
●
Store the copper pipes indoors and seal the both end of them until they are brazed in order to avoid any dust, dirt or
water getting into pipe. Otherwise it will cause degradation of refrigeration oil and compressor breakdown, etc.
●
Use special tools for R410 refrigerant.
Work procedure
1. Remove the flare nut and blind flanges on the pipe of the indoor unit.
※
Make sure to loosen the flare nut with holding the nut on pipe side with a spanner and giving torque
to the nut with another spanner in order to avoid unexpected stress to the copper pipe, and then
remove them.
(Gas may come out at this time, but it is not abnormal.)
●
Pay attention whether the flare nut pops out. (as the indoor unit is sometimes pressured.)
2. Make a flare on liquid pipe and gas pipe, and connect the refrigeration pipes on the indoor unit.
※
Bend the pipe with as big radius as possible and do not bend the pipe repeatedly. In
addition, do not twist and crush the pipes.
※
Do a flare connection as follows:
●
Make sure to loosen the flare nut with holding the nut on pipe side with a spanner and giving
torque to the nut with another spanner in order to avoid unexpected stress to the copper
pipe, and then remove them.
●
When fastening the flare nut, align the refrigeration pipe with the center of flare nut, screw
the nut for 3-4 times by hand and then tighten it by spanner with the specified torque
mentioned in the table below. Make sure to hold the pipe on the indoor unit securely by a
spanner when tightening the nut in order to avoid unexpected stress on the copper pipe.
3. Cover the flare connection part of the indoor unit with attached insulation material after a gas
leakage inspection, and tighten both ends with attached straps.
●
Make sure to insulate both gas pipes and liquid pipes completely.
※
Incomplete insulation may cause dew condensation or water dropping.
4. Refrigerant is charged in the outdoor unit.
As for the additional refrigerant charge for the indoor unit and piping, refer to the installation
manual attached to the outdoor unit.
Caution
●
Install the drain pipe according to the installation manual in order to drain properly.
Imperfection in draining may cause flood indoors and wetting the household goods, etc.
●
Do not put the drain pipe directly into the ditch where toxic gas such as sulfur, the other harmful and
inflammable gas is generated. Toxic gas would flow into the room and it would cause serious
damage to user’s health and safety (some poisoning or deficiency of oxygen). In addition, it may
cause corrosion of heat exchanger and bad smell.
●
Connect the pipe securely to avoid water leakage from the joint.
●
Insulate the pipe properly to avoid condensation drop.
●
Check if the water can flow out properly from both the drain outlet on the indoor unit and the end
of the drain pipe after installation.
●
Make sure to make descending slope of greater than 1/100 and do not make up-down bend and/or trap
in the midway. In addition, do not put air vent on the drain pipe. Check if water is drained out properly
from the pipe during commissioning. Also, keep sufficient space for inspection and maintenance.
Pipe diameter
Tightening torque N·m
• •
6.35
• •
9.52
• •
12.7
14 ~ 18
34 ~ 42
49 ~ 61
Strap (Accessory)
Pipe cover (Accessory)
The thickness of insulation should be 20mm or more.
Work procedure
1. Insert the supplied drain hose (the end made of soft PVC) to the step of the drain socket on the indoor unit
and fix it securely with the clamp.
Attach the hose clamp to the drain hose around 10mm from the end.
●
Do not apply adhesives on this end.
●
Do not use acetone-based adhesives to connect the drain socket.
2. Prepare a joint for connecting VP-20 pipe, adhere and connect the joint to the drain hose
(the end made of rigid PVC), and adhere and connect VP-20 pipe (prepare on site).
※
As for drain pipe, apply VP-20 made of rigid PVC which is on the market.
●
Make sure that the adhesive will not get into the supplied drain hose.
It may cause the flexible part broken after the adhesive is dried up and gets rigid.
●
The flexible drain hose is intended to absorb a small difference at the unit or installation
of drain pipes. Intentional bending, expanding may cause the flexible hose broken and
water leakage.
3. Make sure to make descending slope of greater than 1/100 and do not make up-down bend
and/or trap in the midway.
●
Pay attention not to give stress on the pipe on the indoor unit side, and support and fix
the pipe as close place to the unit as possible when connecting the drain pipe.
●
Do not set up air vent.
●
When sharing a drain pipe for more than
one unit, lay the main pipe 100mm
below the drain outlet of the unit. In
addition, select VP-30 or bigger size for
main drain pipe.
⑦
Drain pipe (continued)
⑧
Wiring-out position and wiring connection
⑨
Check list after installation
Drain pump operation
○
In case electrical wiring work finished
Drain pump can be operated by remote controller (wired).
For the operation method, refer to Operation for drain pump in the installation manual for wiring
work.
○
In case electrical wiring work not finished
Drain pump will run continuously when the dip switch“SW7-1” on the indoor unit PCB is turned ON, the Connec-
tor CNB is disconnected, and then the power supply (230VAC on the terminal block
①
and
②
) is turned ON.
Make sure to turn OFF “SW7-1” and reconnect the Connector CNB after the test.
●
Electrical installation work must be performed according to the installation manual by an
electrical installation service provider qualified by a power provider of the country, and be
executed according to the technical standards and other regulations applicable to electrical
installation in the country.
Be sure to use an exclusive circuit.
●
Use specified cord, fasten the wiring to the terminal securely, and hold the cord securely in
order not to apply unexpected stress on the terminal.
●
Do not put both power source line and signal line on the same route. It may cause miscommu-
nication and malfunction.
●
Be sure to do D type grounding work.
●
For the details of electrical wiring work, see attached instruction manual for electrical wiring
work.
1. Remove a lid of the control box (3 screws) and the wiring cover (2 screws).
2. Hold each wiring inside the unit and fasten them to terminal block securely.
3. Fix the wiring with clamps.
4. Install the removed parts back to original place.
Power source side
terminal block
Earth
Earth
(Shielded cord)
Indoor power source line
Signal line (Shielded cord)
Power source line clamp
Signal side terminal block
Remote controller line
3. The air conditioning unit main body is not equipped with air filters. Incorporate air filters in
an air intake grille, which will facilitate the cleaning of air filters.
4. In the case of a rear-intake type with duct and a rear-intake ceiling-return type installation,
be sure to provide a 350 mm x 1300 mm inspection opening right beneath the unit's fan side
bottom plate to permit servicing of the unit as illustrated in installation geometries. In the case of
an underside-intake type with duct and underside-intake ceiling-return type, provide an intake
opening right beneath the unit's fan side bottom plate so that it will serve as an inspection
opening as well. Also see to its dimensions so that the intake opening will be made to 350 mm x
1300 mm.
5. Take care to install a duct horizontally in connecting the unit with a diffuser.
6. When a canvas duct is used for either intake or outlet duct, install it with care so that it may
not get flattened.
7. Select a desirable diffuser position and diffuser form to ensure the distribution of winds
throughout the room and use a diffuser employing a structure that provides the capability to
regulate winds.
8. Install the air conditioning unit main body via vibration-isolating rubbers to prevent vibrations
from propagating directly from the air conditioning unit main body to the ceiling and slab.
9. Secure at least 0.15m
2
for the opening of an air intake.
10. Never fail to heat-insulate the ducts to prevent condensation on their surfaces.
Drain socket
Stage difflernce part
Drain hose
Unit
Pipe cover (large) (For insulation)
(Accessory)
Pipe cover (small)
(For insulation) (Accessory)
VP20 joint (Prepare on site)
Drain hose
(Accessory)
VP20 (Prepare on site)
Drain socket
Pipe cover (For insulation)
(Prepare on site)
Clamp (Accessory)
Adhesion
290~325mm
Drain hose
Maximum local drain up dimension
600
Joint for VP20 (Prepare on site)
Right overhead
Unit
Pour water in the drain pan with a siphon.
Attached drain
hose clamp
Drain
piping
Drain situation can be checked with
transparent socket.
Pour water into a
convex joint
If the electrical work has not been completed, connect a convex
joint in the drain pipe connection to provide a water inlet.
Then, check if water leaks from the piping system and that
drain flows through the drain pipe normally.
Drain pan
Pouring water hose
Remove this pipe bracket from the unit.
A
Over 20mm
Fasten the screw securely
Hose clamp Drain hose
Drain socket
Metal plate
10mm
Supporting fixture
Supporting metal
Air vent
No bump
No trap
Not touching
the water
Trapped air will
generate noises.
Insulation material
1.5m~2m
Descending slope greater than 1/100
Descending slope greater than 1/100
VP-30 or bigger
As wide as possible
(about100mm)
4. Insulate the drain pipe.
●
Be sure to insulate the drain socket and rigid PVC pipe installed indoors otherwise it may
cause dew condensation and water leakage.
※
After drainage test implementation, cover the drain socket part with pipe cover (small size), then
use the pipe cover (big size) to cover the pipe cover (small size), clamps and part of the drain
hose, and fix and wrap it with tapes to wrap and make joint part gapless.
Drain up
●
The position for drain pipe outlet can be raised up to 600mm above the ceiling. Use elbows for
installation to avoid obstacles inside ceiling. If the horizontal drain pipe is too long before vertical pipe,
the backflow of water will increase when the unit is stopped, and it may cause overflow of water from
the drain pan on the indoor unit. In order to avoid overflow, keep the horizontal pipe length and offset of
the pipe within the limit shown in the figure below.
Drain test
1. Conduct a drainage test after completion of the electrical work.
2. During the trial, make sure that drain flows properly through the piping and that no water
leaks from connections.
3. In case of a new building, conduct the test before it is furnished with the ceiling.
4. Be sure to conduct this test even when the unit is installed in the heating season.
Procedures
1. Supply about 1000 cc of water to the unit through the air outlet by using a feed water pump.
2. Check the drain while cooling operation.
●
Check the following items after all installation work completed.
Check if
Expected trouble
Check
The indoor and outdoor units are fixed securely?
Falling, vibration, noise
Inspection for leakage is done?
Insufficient capacity
Insulation work is properly done?
Water leakage
Water is drained properly?
Water leakage
Supply voltage is same as mentioned in the model name plate?
PCB burnt out, not working at all
There is mis-wiring or mis-connection of piping?
PCB burnt out, not working at all
Earth wiring is connected properly?
Electric shock
Cable size comply with specified size?
PCB burnt out, not working at all
Any obstacle blocks airflow on air inlet and outlet?
Insufficient capacity
Summary of Contents for 112KXE6
Page 105: ... 101 Model FDC335KXE6 A PCB003Z035 shows local wining ...
Page 134: ... 130 PJF012D003 ...
Page 135: ... 131 ...
Page 139: ... 135 PJA012D751 b ...
Page 140: ... 136 ...
Page 206: ... 202 2 model type DIS model type HEAD ...
Page 207: ... 203 2 2 ...
Page 208: ... 204 2 2 2 2 2 ...