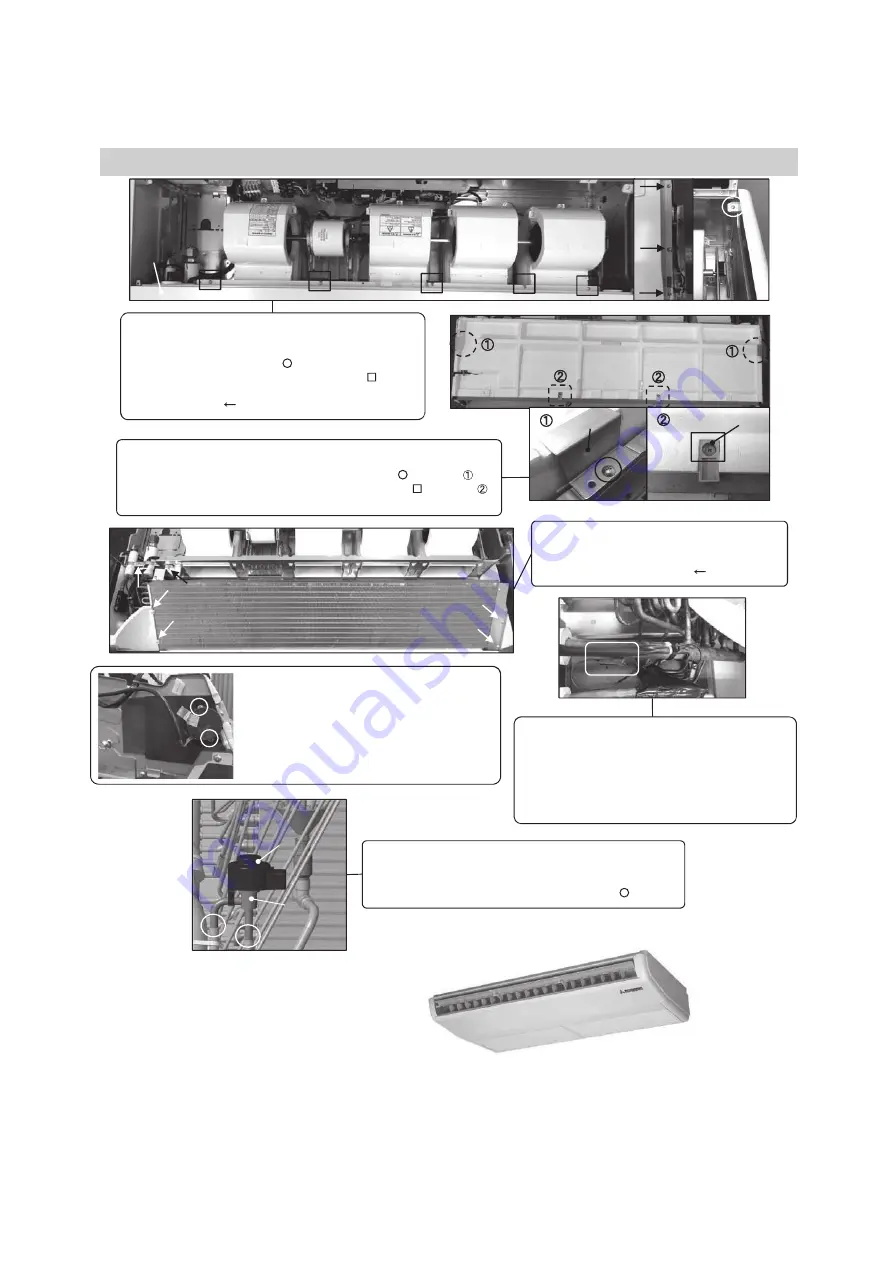
–
163
–
‘19 • KX-SM-318
6. To remove side panel and bo
tt
om panel
(1) Remove air inlet grille.(See No.1)
(2) Remove the right and le
ft
side panel
fi
screws and remove it.( mark)
(3) Remove 5 bo
ttom p
a
nel fixin
g screws.( mark)
Remove 6 bo
ttom p
a
nel fixin
g screws and
remove it. ( mark, le
ft
and right side)
7. To remove drain pan
(1) Remove side panel and bo
tt
om panel.(See No.5)
(2) Remove 2 plate
fixin
g screws and remove it.( mark, Pic. )
(3) Remove 2 support
fi
xing screws and remove it.( mark, Pic. )
(4) Pull out the drain pan.
8. To remove the heat exchanger assembly
(1) Remove the drain pan.(See No.6)
(2) Remove 6 heat exchanger assy
fi
screws and remove it.( mark)
9. To remove the louver motor (LM)
(1) Remove the lid of control box.(See No.1)
(2) Disconnect the louver motor connector
(CNJ) on PCB in control box.
10. To remove the temperature sensors (example"Thi-R3")
(3) Remove side panel.(See No.5)
(1) Remove the lid of control box.(See No.1)
(4) Remove 2 louver mot
or fi
xing screws
(2) Disconnect the Tho-R3 connector(CNNx)
.
x
o
b
l
o
r
t
n
o
c
n
i
B
C
P
n
o
.t
i
e
v
o
m
e
r
d
n
a
(3) Remove the drain pan.(See No.3)
(4) Pull out the temperature sensor "Thi-R1"
from the sensor holder.
11. To remove the Electronic Expansion Valve (EEV)
(1) Remove the heat exchanger assembly.(See No.9)
(2) Remove the coil of EEV by pull out on the top.
(3) Remove welded part of EEV by welding.( mark)
PROCEDURE & PICTURES
Bo
tt
om panel
Plate
Support
EEV
Coil of EEV
General view
Summary of Contents for FDC121KXZEN1
Page 159: ... 158 19 KX SM 318 ...
Page 161: ... 160 19 KX SM 318 ...
Page 162: ... 161 19 KX SM 318 ...