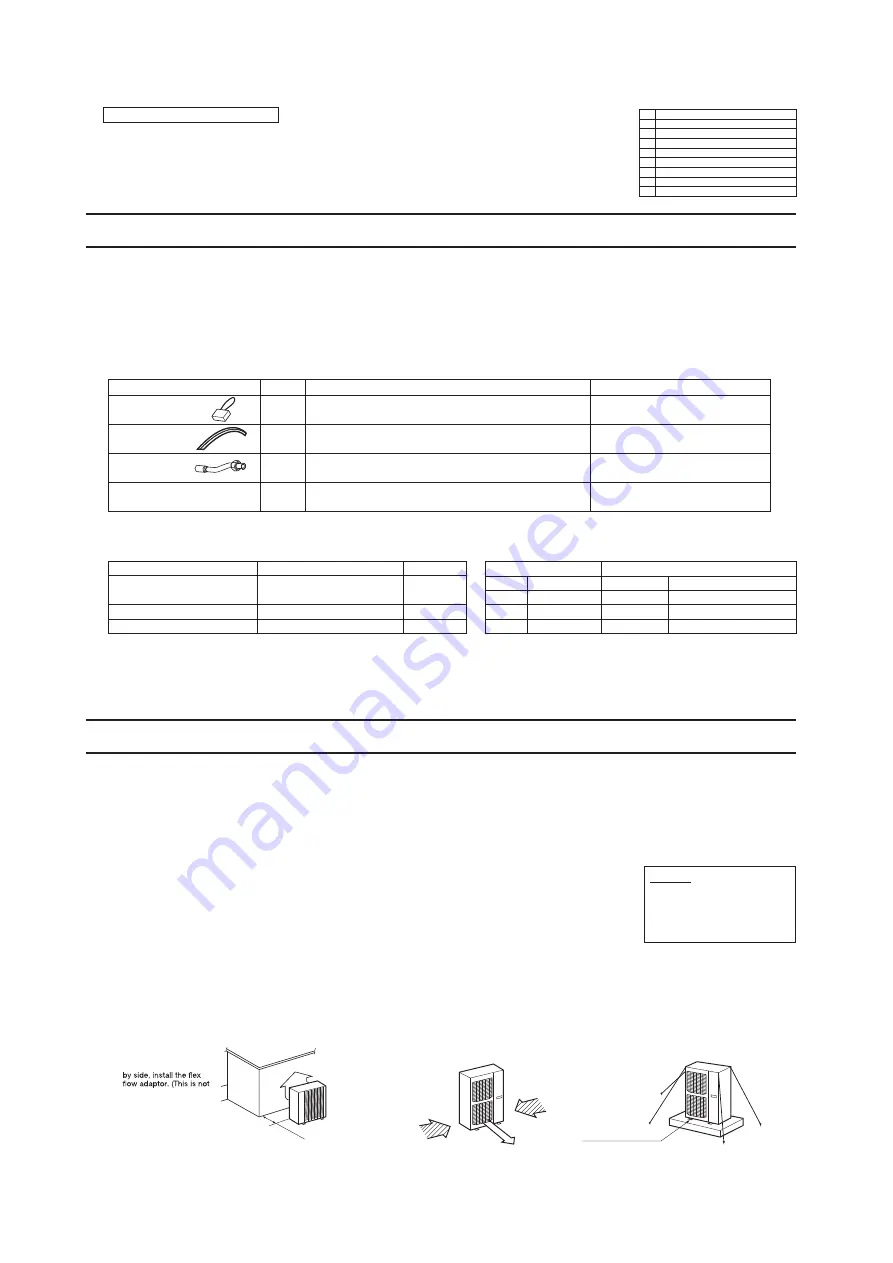
–
128
–
'18 • KX-SM-292
20
Out door unit
Height difference
between indoor
units: 18 m thicker
Height difference
50 m
Actual length
160 m
Equivalent length
185 m
Total piping length 510 m
Indoor unit
Suction
Blowout
195
195
690
Foundation bolt position
(4 places)
20
520
20
●
The protrusion of an anchor bolt on the front side must be
kept within 15 mm.
●
Securely install the unit so that it does not fall over during
earthquakes or strong winds, etc.
●
Refer to the above illustrations for information regarding
concrete foundations.
●
Install the unit in a level area. (With a gradient of 5 mm or
less.)
Improper installation can result in a compressor failure, broken
piping within the unit and abnormal noise generation.
Wooden base
Wear plate
fig
1
Indoor unit
Indoor unit
Outdoor unit
Branch pipe set for indoor unit side
Model: DIS
Branch pipe set for indoor unit side
Model: DIS
Header set for indoor unit side
Model: HEAD
A
B
B
C
C
B
B
C
C
C
C
C
C
Accessory
Caution
●
Be sure to read this manual before installation to follow the proper installation methods.
●
When installing the indoor unit, read the installation manual of indoor unit.
●
Option distribution parts are required for the piping (Branch pipe set, header set). For details, refer to the catalog, etc.
●
Make sure to install the earth leakage breaker. (Select a product compatible with high frequency.)
●
There is risk of damaging the compressor if the unit is operated while the discharge pipe temperature sensor, suction pipe temperature sensor, pressure sensor, etc. are removed.
Never attempt to operation in such condition.
●
With this air-conditioning system, room temperature may rise, depending on installation conditions, while indoor units are stopped, because small quantity of refrigerant flows into
the stopped indoor units if heating operation is conducted on the system.
Combination pattern
●
Combination pattern of outdoor units, number of indoor units connected and capacity of connection are as show in the table at right.
●
It can be used in combination with the following indoor unit.
Name
Wire
Quantity
2
1
1
1
Location of use
Insert this in CnG on the outdoor unit PCB when using the silencing mode or
forced cooling mode
Secured in the control box with adhesive tape.
It is attached to the bracket with an adhesive tape
in the proximity of the service valve.
Attached on the base below the service valve.
Attached on the base below the service valve.
1. BEFORE BEGINNING INSTALLATION
(Check that the models, power source specifications, piping, wiring are correct.)
3-1. Delivery
2. INSTALLATION LOCATION
(Obtain approval from the customer when selecting the installation area.)
2-1. Selecting the installation location
●
Deliver the unit in the packing to the specified installation place.
●
To hoist the unit, attach a pair of textile ropes with cushion materials attached to protect it.
Request
Put cushion materials between the unit and the ropes to avoid damages.
Attach the ropes on the unit and carry it in avoiding displacement of gravity center.
Improper slinging may cause the unit to lose balance and fall.
4. REFRIGERANT PIPING
3. Unit delivery and installation
(1) Limitation on use of pipes
(3) Pipe size selection
Caution
●
When arranging pipes, observe the restrictions on use concerning the longest distance of (1), total piping length,
allowable pipe length from initial branching and allowable difference of height (difference between heads).
●
●
Maximum length (To the furthest indoor unit) … Actual length Less than 160 m (Actual length less
than 185 m)
It is required to change the pipe diameter when the actual length exceeds 90 m.
Determine the size of main pipe, referring to the table of main pipe selection table of (3) (a).
●
Total piping length ………………………………………………………… 510 m or less
●
Length of main pipe ……………………………………………………… 130 m or less
●
Allowable pipe length from initial branching …………………………… 90 m or less
Difference in pipe lengths between indoor units, however, is 40 m or less.
●
Allowable difference in height (Difference of heads)
(a) When an indoor unit is positioned at a higher place ……………… 50 m or less
(b) When an outdoor unit is positioned at a lower place ……………… 40 m or less
(c) Difference of heights between indoor units in a system …………… 18 m or less
(d) Difference of heights between initial branching and indoor unit … 18 m or less
(2) Selection of pipe material
●
Use pipes with the inside clean and free from any harmful sulfur, oxides, dirt, chips & oil, or moisture
(contamination).
●
Use following refrigerant pipes.
Material … Phosphate deoxidation treated seamless pipe (C1220T-O, 1/2H, JIS H 3300)
C1220T-1/2H for O.D. ø19.05 or more, or C1220T-O for ø15.8 or less
●
Wall thickness and size - Select according to the guide for pipe size selection
(This product uses R410A. Since, in case of pipes in the size of ø19.05 or more, materials of -O
thickness larger than the minimum thickness.)
●
When a pipe is branched, make sure to use our branching set or header set.
●
When setting branching pipes, take care of the mounting direction and consult carefully with the
instruction manual.
●
Regarding the handling of service valve, refer to 4-3 (1) Operating method of service valve.
●
Make sure to lock the fixing legs of outdoor unit with 4 pieces of anchor bolt (M10). Best margin of protrusion for bolt above the
floor is 20 mm.
●
When installing the unit, make sure to lock its legs with the following bolts.
3-2. Cautions for installation
CAUTION
Make sure to install within the range of limitation. Otherwise, resulting
malfunction of compressor may not be warranted. Observe always the
limitation of use during installation.
Over 500 mm
Fasten with anchor bolts
Edging
Attached
wire
Instruction manual
Use it for protection of a knock-out hole.
Use this when connecting gas pipe.
When the installation work is completed,
give instructions to the customer and ask him/her to keep it.
4-1
. Determination of piping specifications
(Please select from the following matrix according to indoor unit specifications and installation site conditions.)
Lock with bolt (M10-12)
Suction
Blowout
Use a long block to extend the width.
Use a thicker
block to anchor
deeper.
PSC012D119
◎
This installation manual deals with outdoor units and general installation specifications only. For indoor units, please refer to the respective installation manuals supplied with your units.
◎
Please read this manual carefully before you set to installation work and carry it out according to the instructions contained in this manual.
Outdoor unit capacity
FDC224
-
335
Notabilia as a unit designed for R410A
a
)
b
)
c
)
d
)
e
)
f
)
g
)
h
)
Gauge manifold
Charge hose
Electronic scale for refrigerant charging
Torque wrench
Flare tool
Protrusion control copper pipe gauge
Vacuum pump adapter
Gas leak detector
Dedicated R410A tools
●
Do not use any refrigerant other than R410A. R410A will rise to pressure about 1.6 times higher than that of a conventional refrigerant.
●
A unit designed for R410A has adopted a different size outdoor unit service valve charge port and a different size check joint provided in the unit to
prevent the charging of a wrong refrigerant by mistake. The processed dimension of the flared part of a refrigerant pipe and a flare nut's parallel side
measurement have also been altered to raise strength against pressure. Accordingly, you are required to arrange dedicated R410A tools listed in the
table on the right before installing or servicing this unit.
●
Do not use a charge cylinder. The use of a charge cylinder will cause the refrigerant composition to change, which results in performance degradation.
●
In charging refrigerant, always take it out from a cylinder in the liquid phase.
●
All indoor units must be models designed exclusively for R410A. Please check connectable indoor unit models in a catalog, etc.
(A wrong indoor unit, if connected into the system, will impair proper system operation)
Sample
Size
L
1
L
2
L
3
L
4
Ⅰ
Open
300
300
250 (5)
Ⅱ
Open
5
300
250 (5)
Ⅲ
1500 (500)
Open
300
250 (5)
Air
inlet
Air
inlet
Air
outlet
Service
space
L
3
L
2
L
4
L
1
(Unit : mm)
a) Minimum installation space
(Please select an installation point with due attention to the direction of installation of the refrigerant pipe)
(If the installation conditions shown in this drawing are not satisfied, please consult with your dealer
or the manufacturer.)
b) When two or more units are installed in a line, secure a service space of minimum 250 mm between
each pair of neighboring units. The units can be operated, however, if they are separated by more
than 10 mm each other. Where this minimum space is not available, it may be adapted by moving
one of the units, for example, during the service work.
c) Don’t install at a place where it will be surrounded with walls in four directions.
Even when it is not surrounded with walls in four directions and it is met the installation conditions
as shown by this figure, if there is risk of short-circuit, install the flex flow adaptor to prevent the
short-circuit.
d) There must be a 1-meter or larger space in the above.
e) A barrier wall placed in front of the exhaust diffuser must not be higher than the unit.
2-2. Installation space (Ex. servicing space)
Floor surface
Floor surface
Floor surface
Liquid side
Horizontal
Floor surface
Floor surface
Gas side
Floor surface
Branching at
downstream
side
Important
In case that the unit operates in cooling mode, when the outdoor temperature is –5°C or lower,
please equip a flex flow adapter and a snow guard hood (option) on the unit.
[Items sold separately]
Refrigerant pipe distribution parts, which are not contained in the package, will be required for installation.
As for refrigerant pipe distribution parts, we offer branching pipe sets (Model type: DIS) and header sets (Model type: HEAD) as parts used on the indoor side of piping.
Please select one suiting your application. In selecting distribution parts, please also refer to “4. REFRIGERANT PIPING.”
If you are not sure which parts to select, please consult with your dealer or the manufacture.
Use refrigerant branching pipe sets and header sets designed exclusively for R410A without fail.
①
Place the unit outlet pipe perpendicular
to the wind direction.
②
Please install so the direction of the air from the blowing
outlet will be perpendicular to the direction of the wind.
③
When the foundation is not level, use wires
to tie down the unit.
〇
Where air is not trapped.
〇
Where the installation fittings can be firmly installed.
〇
Where any object does not prevent inlet or outlet air.
〇
Out of the heat range of other heat sources.
〇
Where strong winds will not blow against the outlet air.
〇
A place where stringent regulation of electric noises is applicable.
〇
Where it is safe for the drain water to be discharged.
〇
Where noise and hot air will not bother neighboring residents.
〇
Where snow will not accumulate.
〇
A place where no TV set or radio receiver is placed within 5m.
(If electrical interference is caused, seek a place less likely to cause the problem)
〇
Do not install the unit in places which exposed to sea breeze (e.g. coastal area) or calcium
chloride (e.g. snow melting agent), exposed to ammonia substance (e.g. organic fertilizer).
Please note
a) If there is a possibility of a short-circuit, then install a flex flow adapter.
b) When installing multiple units, provide sufficient intake space so that a short-circuit does not occur.
c) In areas where there is snowfall, install the unit in a frame or under a snow hood to prevent snow from accumulating on it.
(Inhibition of collective drain discharge in a snowy country)
d) Do not install the equipment in areas where there is a danger for potential explosive atmosphere.
e) Install the equipment in a location that can sufficiently support the weight of the equipment.
f)
If a unit is installed into a special environment as shown below, there will be a danger that the corrosion of the outdoor unit or its
malfunctioning is caused. If this is the case, please consult with the distributor from whom you have purchased the unit.
・
Where corrosive gas is generated (such as a hot-spring resort area).
・
Where the unit is subject to sea breezes (coastal area).
・
Where the unit is subject to oil mists.
・
Where equipment generating electromagnetic waves exists in the vicinity.
g) When strong winds occur
●
Where it is likely that the unit is subjected to strong winds, provide wind guards according to the following guidelines.
Strong winds can cause performance degradation, an accidental stop due to a rise of high pressure and a broken fan.
CAUTION
Please leave sufficient clearance
around the unit without fail.
Otherwise, a risk of compressor
and/or electric component failure
may arise.
When installing units side
required if a distance of
1,500 mm may be
secured between the
blowing outlet and the
wall.)
Wind direction
Wind direction
Outdoor unit
224
280
335
Gas pipe
ø19.5×t1.0
ø22.22×t1.0
ø25.4(ø22.22)×t1.0
Liquid pipe
ø9.52×t0.8
ø12.7×t0.8
Gas pipe
ø22.22×t1.0
ø25.4(ø22.22)×t1.0
Liquid pipe
ø12.7×t0.80
Main pipe size (Ordinary)
Pipe size for actual length longer than 90 m
For ø19.05 or larger, use C1220T-1/2H material.
Make sure to use the attached pipes
in the length as shown at left.
For ø19.05 or larger, use C1220T-1/2H material.
*1: When connecting indoor units of 280 at the downstream and the main gas pipe is of ø22.22 or larger, use the pipe of ø22.22x t1
(a) Main pipe (Between branch at outdoor unit side - initial branch at indoor unit side): Section A in Fig. 1
When the maximum length (to the furthest indoor unit from outdoor unit) is 90 m or more (actual length), change the size of main pipe as shown
by the following table.
(b) Between initial branch at indoor unit side- indoor unit side: Section B in Fig. 1
Select from following table based on the total capacity of indoor units connected at the downstream side. However, it should never exceed the
size of main pipe (Section A in Fig. 1).
Total capacity of indoor units
Less than 70
70 - 180
180 - 371
371 - 540
Gas pipe
ø12.7 ×t1.0
ø15.88×t1.0
ø19.05×t1.0 *
1
ø25.4(ø22.22)×t1.0
Liquid pipe
ø 9.52×t0.8
ø12.7×t0.8
ø15.88×t1.0
For ø19.05 or larger, use C1220T-1/2H material.
Total capacity at downstream
Less than 180
180 - 371
371 - 540
Branch pipe set
DIS-22-1G
DIS-180-1G
DIS-371-1G
(c) Between branching at indoor unit side - indoor unit side: Section C in Fig. 1
According to the table of pipe size for indoor unit. However, it should never exceed the size of main pipe (Section A in Fig. 1).
(4) Selection of the branch set for indoor unit side
(a) Selection of the branch pipe set
●
Size of branch pipe varies depending on the capacity of connected indoor units (total capacity at
downstream). Select it from the table at right.
Request
●
Adjust the indoor unit and the size of branch pipe at the indoor unit side according to the size of
pipe connected to indoor unit.
●
“Vertical branching”.
(b) Selection of the header set
●
depending on he number of units connected.
●
For the size of plugged pipe, refer to the header set (option item).
Request
●
Adjust the header and indoor unit pipes to the size of pipes for connected indoor units.
●
branch is provided at the downstream side.
●
Header is not allowed to receive indoor units of 224 or 280.
Capacity
22
,
28
36
,
45
,
56
71
,
80
,
90
,
112
,
140
,
160
224
280
Gas pipe
ø 9.52×t0.8
ø 12.7×t0.8
ø15.88×t1.0
ø19.05×t1.0
ø22.22×t1.0
Liquid pipe
ø6.35×t0.8
ø9.52×t0.8
Indoor unit
Vertical
Floor surface
Floor surface
Floor surface
Floor surface
Horizontal
Total capacity at downstream
Less than 180
180 - 371
371 - 540
Header set model
HEAD4-22-1G
HEAD6-180-1G
HEAD8-371-2
Number of branches
Max. 4 branches
Max. 6 branches
Max. 6 branches
adaptor is installed.
SAFETY PRECAUTIONS
●
We recommend you to read this "SAFETY PRECAUTIONS" carefully before the installation work in order to gain full advantage of the functions of the unit and to avoid malfunction due to mishandling.
●
The precautions described below are divided into and . The matters with possibilities leading to serious consequences such as death or serious personal
injury due to erroneous handling are listed in the and the matters with possibilities leading to personal injury or damage of the unit due to erroneous handling including
probability leading to serious consequences in some cases are listed in .
These are very important precautions for safety. Be sure to observe all of them without fail.
●
The meaning of"Marks"used here are as shown on the right.
●
Be sure to confirm no anomaly on the equipment by commissioning after completed installation and explain the operating methods as well as the maintenance methods of this equipment to
the user according to the owner's manual.
●
Keep the installation manual together with owner's manual at a place where any user can read at any time. Moreover if necessary, ask to hand them to a new user
●
This unit complies with EN61000-3-3.
For outdoor unit, EN61000-3-2 is not applicable as consent by the utility company or notification to the utility company is given before usage. (Only 224, 280)
For outdoor unit, EN61000-3-12 is not applicable as consent by the utility company or notification to the utility company is given before usage. (Only 335)
Never do it under any circumstance.
Always do it according to the instruction.
WARNINGS
WARNINGS
CAUTIONS
CAUTIONS
WARNING
CAUTION
●
Installation must be carried out by the qualified installer.
If you install the system by yourself, it may cause serious trouble such as water leaks, electric shocks, fire and personal injury ,
as a result of a system malfunction.
●
Install the system in full accordance with the instruction manual.
Incorrect installation may cause bursts, personal injury, water leaks, electric shocks and fire.
●
Use the original accessories and the specified components for installation.
If parts other than those prescribed by us are used, It may cause fall of the unit, water leaks, electric shocks, fire, refrigerant leak,
substandard performance, contrl failure and personal injury.
●
When installing in small rooms, take prevention measures not to exceed the density limit of refrigerant in the event of leakage
accordance with ISO5149.
Consult the expert about prevention measures. If the density of refrigerant exceeds the limit in the event of leakage, lack of
oxygen can occur, which can cause serious accidents.
●
Ventilate the working area well in the event of refrigerant leakage during installation.
If the refrigerant comes into contact with naked flames, poisonous gas is produced.
●
After completed installation, check that no refrigerant leaks from the system.
If refrigerant leaks into the room and comes into contact with an oven or other hot surface, poisonous gas is produced.
●
Hang up the unit at the specified points with ropes which can support the weight in lifting for portage. And to avoid jolting out of
alignment, be sure to hang up the unit at 4-point support.
An improper manner of portage such as 3-point support can cause death or serious personal injury due to falling of the unit.
●
Install the unit in a location with good support.
Unsuitable installation locations can cause the unit to fall and cause material damage and personal injury.
●
Ensure the unit is stable when installed, so that it can withstand earthquakes and strong winds.
Unsuitable installation locations can cause the unit to fall and cause material damage and personal injury.
●
The electrical installation must be carried out by the qualified electrician in accordance with "the norm for electrical work" and
"national wiring regulation", and the system must be connected to the dedicated circuit.
Power source with insufficient capacity and incorrect function done by improper work can cause electric shocks and fire.
●
Be sure to shut off the power before starting electrical work.
Failure to shut off the power can cause electric shocks, unit failure or incorrect function of equipment.
●
Be sure to use the cables conformed to safety standard and cable ampacity for power distribution work.
Unconformable cables can cause electric leak, anomalous heat production or fire.
●
Use the prescribed cables for electrical connection, tighten the cables securely in terminal block and relieve the cables correctly
to prevent overloading the terminal blocks.
Loose connections or cable mountings can cause anomalous heat production or fire.
●
Arrange the wiring in the control box so that it cannot be pushed up further into the box. Install the service panel correctly.
Incorrect installation may result in overheating and fire.
●
In connecting the power cable, make sure that no anomakies such as dust deposits, socket clogging or wobble are found and
insert the plug securely.
Accumulation of dust, clogging on the socket, or looseness of plugging can cause electric shocks and fire.
●
Be sure not to reuse existing refrigerant pipes
Conventional refrigerant oil or chlorine contained in the conventional refrigerant which is remaining in the existing refrigerant
pipes can cause deterioration of refrigerant oil of new unit. And 1.6 times higher pressure of R410A refrigerant than conventional
one can cause burst of existing pipe, personal injury or serious accident.
●
Do not perform brazing work in the airtight room
It can cause lack of oxygen.
●
Use the prescribed pipes, flare nuts and tools for R410A.
Using existing parts (for R22 or R407C) can cause the unit failure and serious accidents due to burst of the refrigerant circuit.
●
Tighten the flare nut by using double spanners and torque wrench according to prescribed method. Be sure not to tighten the
flare nut too much.
Loose flare connection or damage on the flare part by tightening with excess torque can cause burst or refrigerant leaks which
may result in lack of oxygen.
●
Do not open the service valves for liquid line and gas line until completed refrigerant piping work, air tightness test and evacuation.
If the compressor is operated in state of opening service valves before completed connection of refrigerant piping work, you may
incur frost bite or injury from an abrupt refrigerant outflow and air can be sucked into refrigerant circuit, which can cause burst or
personal injury due to anomalously high pressure in the refrigerant.
●
Do not put the drainage pipe directly into drainage channels where poisonous gases such as sulphide gas can occur.
Poisonous gases will flow into the room through drainage pipe and seriously affect the user's health and safety. It can also cause
the corrosion of the indoor unit and resultant unit failure or refrigerant leak.
●
Only use prescribed option parts. The installation must be carried out by the qualified installer.
If you install the system by yourself, it can cause serious trouble such as water leaks, electric shocks, fire.
●
Do not perform any change of protective device itself or its setup condition
The forced operation by short-circuiting protective device of pressure switch and temperature control or the use of non
specified component can cause fire or burst.
●
Be sure to switch off the power source in the event of installation, inspection or servicing.
If the power source is not shut off, there is a risk of electric shocks, unit failure or personal injury due to the unexpected start of fan.
●
Consult the dealer or an expert regarding removal of the unit.
Incorrect installation can cause water leaks, electric shocks or fire.
●
Stop the compressor before closing valve and disconnecting refrigerant pipes in case of pump down operation.
If disconnecting refrigerant pipes in state of opening service valves before compressor stopping, you may incur frost bite or injury
from an abrupt refrigerant outflow and air can be sucked, which can cause burst or personal injury due to anomalously high
pressure in the refrigerant circuit.
●
Ensure that no air enters in the refrigerant circuit when the unit is installed and removed.
If air enters in the refrigerant circuit, the pressure in the refrigerant circuit becomes too high, which can cause burst and
personal injury.
●
Do not run the unit with removed panels or protections
Touching rotating equipments, hot surfaces or high voltage parts can cause personal injury due to entrapment, burn or electric shocks.
●
Be sure to fix up the service panels.
Incorrect fixing can cause electric shocks or fire due to intrusion of dust or water.
●
Do not perform any repairs or modifications by yourself. Consult the dealer if the unit requires repair.
If you repair or modify the unit, it can cause water leaks, electric shocks or fire.
●
Use the circuit breaker for all pole with correct capacity.
Using the incorrect circuit breaker, it can cause the unit malfunction and fire.
●
Take care when carrying the unit by hand.
If the unit weights more than 20kg, it must be carried by two or more persons. Do not carry by the plastic straps, always use the carry handle
when carrying the unit by hand. Use gloves to minimize the risk of cuts by the aluminum fins.
●
Dispose of any packing materials correctly.
Any remaining packing materials can cause personal injury as it contains nails and wood. And to avoid danger of suffocation,
be sure to keep the plastic wrapper away from children and to dispose after tear it up.
●
Pay attention not to damage the drain pan by weld spatter when welding work is done near the indoor unit.
If weld spatter entered into the indoor unit during welding work, it can cause pin-hole in drain pan and result in water
leakage. To prevent such damage, keep the indoor unit in its packing or cover it.
●
Be sure to insulate the refrigerant pipes so as not to condense the ambient air moisture on them.
Insufficient insulation can cause condensation, which can lead to moisture damage on the ceiling, floor, furniture and any
other valuables.
●
Be sure to perform air tightness test by pressurizing with nitrogen gas after completed refrigerant piping work.
If the density of refrigerant exceeds the limit in the event of refrigerant leakage in the small room, lack of oxygen can occur,
which can cause serious accidents.
●
Perform installation work properly according to this installation manual.
Improper installation can cause abnormal vibrations or increased noise generation.
●
Carry out the electrical work for ground lead with care.
Do not connect the ground lead to the gas line, water line, lightning conductor or telephone line's ground lead. Incorrect
grounding can cause unit faults such as electric shocks due to short-circuiting.
Never connect the grounding wire to a
gas pipe because if gas leaks, it could cause explosion or ignition.
●
Earth leakage breaker must be installed
If the earth leakage breaker is not installed, it can cause fire or electric shocks.
●
Do not use any materials other than a fuse with the correct rating in the location where fuses are to be used.
Connecting the circuit with copper wire or other metal thread can cause unit failure and fire.
●
Do not install the unit near the location where leakage of combustible gases can occur.
If leaked gases accumulate around the unit, it can cause fire.
●
Do not install the unit where corrosive gas (such as sulfurous acid gas etc.) or combustible gas (such as thinner and petroleum
gases) can accumulate or collect, or where volatile combustible substances are handled.
Corrosive gas can cause corrosion of heat exchanger, breakage of plastic parts and etc. And combustible gas can cause fire.
●
Secure a space for installation, inspection and maintenance specified in the manual.
Insufficient space can result in accident such as personal injury due to falling from the installation place.
●
When the outdoor unit is installed on a roof or a high place, provide permanent ladders and handrails along the access
route and fences and handrails around the outdoor unit.
If safety facilities are not provided, it can cause personal injury due to falling from the installation place.
●
Do not install nor use the system close to the equipment that generates electromagnetic fields or high frequency harmonics
Equipment such as inverters, standby generators, medical high frequency equipments and telecommunication equipments can
affect the system, and cause malfunctions and breakdowns. The system can also affect medical equipment and
telecommunication equipment, and obstruct its function or cause jamming.
●
Do not install the outdoor unit in a location where insects and small animals can inhabit.
Insects and small animals can enter the electric parts and cause damage or fire. Instruct the user to keep the surroundings clean.
●
Do not use the base flame for outdoor unit which is corroded or damaged due to long periods of operation.
Using an old and damage base flame can cause the unit falling down and cause personal injury.
●
Do not install the unit in the locations listed below
•
Locations where carbon fiber, metal powder or any powder is floating.
•
Locations where any substances that can affect the unit such as sulphide gas, chloride gas, acid and alkaline can occur.
•
Vehicles and ships
•
Locations where cosmetic or special sprays are often used.
•
Locations with direct exposure of oil mist and steam such as kitchen and machine plant.
•
Locations where any machines which generate high frequency harmonics are used.
•
Locations with salty atmospheres such as coastlines
•
Locations with heavy snow (If installed, be sure to provide base flame and snow hood mentioned in the manual)
•
Locations where the unit is exposed to chimney smoke
•
Locations at high altitude (more than 1000m high)
•
Locations with ammonic atmospheres (e.g. organic fertilizer).
•
Locations with calcium chloride (e.g. snow melting agent).
•
Locations where heat radiation from other heat source can affect the unit
•
Locations without good air circulation.
•
Locations with any obstacles which can prevent inlet and outlet air of the unit
•
Locations where short circuit of air can occur (in case of multiple units installation)
•
Locations where strong air blows against the air outlet of outdoor unit
It can cause remarkable decrease in performance, corrosion and damage of components, malfunction and fire.
●
Do not install the outdoor unit in the locations listed below.
•
Locations where discharged hot air or operating sound of the outdoor unit can bother neighborhood.
•
Locations where outlet air of the outdoor unit blows directly to an animal or plants. The outlet air can affect adversely to
the plant etc.
•
Locations where vibration can be amplified and transmitted due to insufficient strength of structure.
•
Locations where vibration and operation sound generated by the outdoor unit can affect seriously.
(on the wall or at the place near bed room)
•
Locations where an equipment affected by high harmonics is placed. (TV set or radio receiver is placed within 5m)
•
Locations where drainage cannot run off safely.
It can affect surrounding environment and cause a claim
●
Do not use the unit for special purposes such as storing foods, cooling precision instruments and preservation of animals,
plants or art.
It can cause the damage of the items.
●
Do not touch any buttons with wet hands
It can cause electric shocks
●
Do not shut off the power source immediately after stopping the operation.
Wait at least 5 minutes, otherwise there is a risk of water leakage or breakdown.
●
Do not control the system with main power switch.
It can cause fire or water leakage. In addition, the fan can start unexpectedly, which can cause personal injury.
●
Do not touch any refrigerant pipes with your hands when the system is in operation.
During operation the refrigerant pipes become extremely hot or extremely cold depending the operating condition, and it
can cause burn injury or frost injury.
●
Do not operate the outdoor unit with any article placed on it.
You may incur property damage or personal injure from a fall of the article.
●
Do not step onto the outdoor unit.
You may incur injury from a drop or fall.
When install the unit, be sure to check whether the selection of installation place, power source specifications, usage limitation (piping length, height differences between
indoor and outdoor units, power source voltage and etc.) and installation spaces.
Application data
*1
*1
secured 250 mm for the dimension L4 when replacing the compressor.
Establish this for example by moving the unit during the work.
*2
*2
*2
*2
Capacity
224
280
335
Combination pattern
Single
Single
Single
Number of units connected (unit)
1
-
22
1
-
24
1
-
24
Range of total capacity of connected indoor units
112
-
336
140
-
420
167
-
502
Outdoor unit
Indoor unit
Indoor unit
Remote control
Connection OK/NO
FD
○△△
KXE6, KXZ
FD
○
A
△△
KXE4R, KXE4BR, KXE5R
FD
○
A
△△
KXE4, KXE4(A), KXE4A
RC-E3 (2 cores), RC-E4 (2 cores),
RC-E5 (2 cores), RC-EX1A (2 cores)
RC-E1R (3 cores)
RC-E1 (3 cores)
OK
NO
NO
Summary of Contents for FDC224KXZME1
Page 169: ... 168 18 KX SM 292 PHA012D402 ...
Page 170: ... 169 18 KX SM 292 Screw ...
Page 171: ... 170 18 KX SM 292 ...
Page 172: ... 171 18 KX SM 292 ...