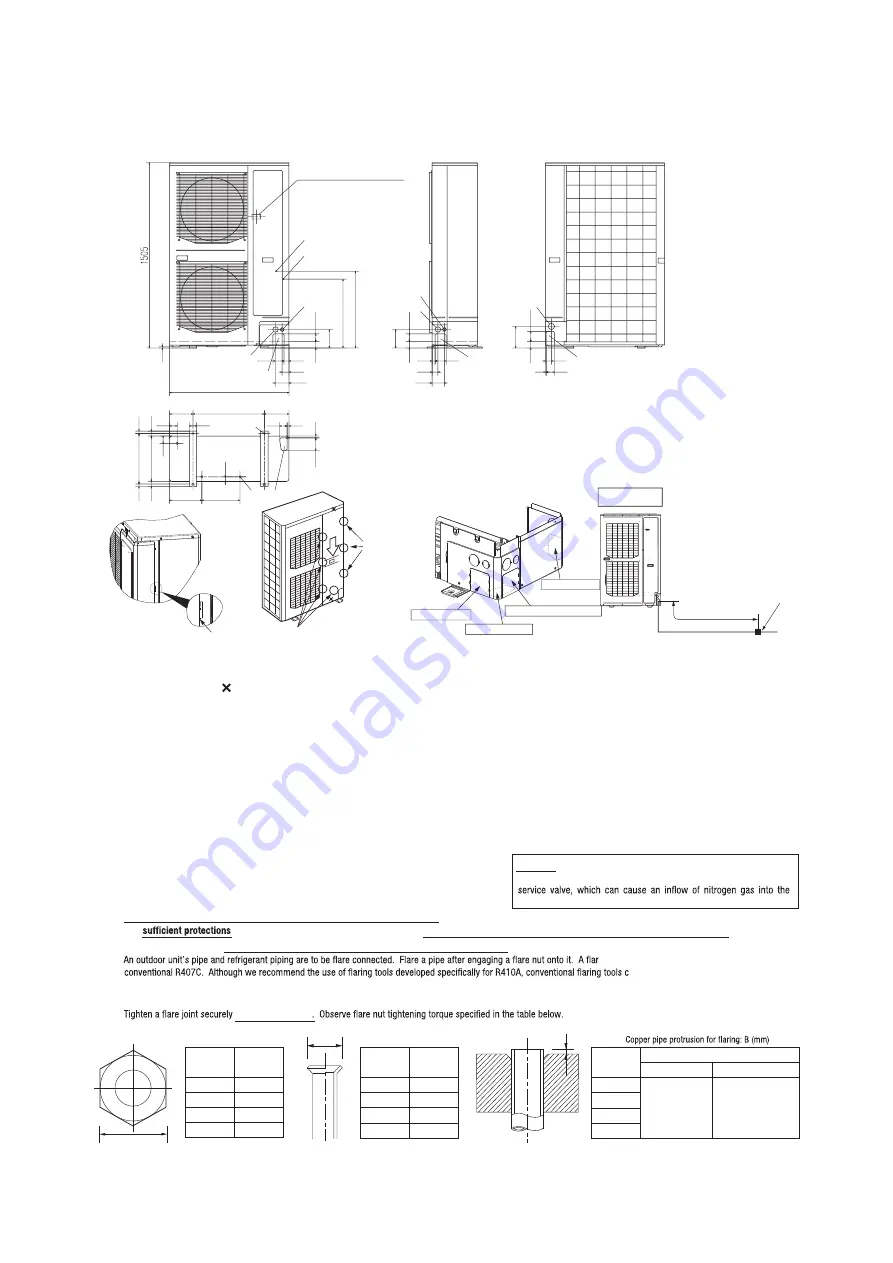
–
131
–
'14 • KX-SM-221
E
C
C
D
F
H
F
G
A
B
F
D
F
69
8
90
65
65
150
150
50
624
560
50 25
47
100
50
50
175
85
40
55
10
110
90
970
580
190
200
15
15
103
60
60
310
262
62
20
40
38
60
410
370
20
40
●
First remove the two screws ( mark) of the service panel and push it down into the direction of the arrow mark and then remove it by pulling it toward you.
●
There are hook right side panel which used in order to prevent a fall the panel.
Lift it a few after pushing it down and then remore it by pulling it towoard you.
●
The pipe can be laid in any of the following directions: side right, front, rear and downward.
●
Remove a knock-out plate provided on the pipe penetration to open a minimum necessary area and attach an edging material supplied as an accessory by cutting it to an appropriate
length before laying a pipe.
●
In laying pipes on the installation site, cut off the casing’s half blank that covers a hole for pipe penetration with nippers.
●
If there is a risk of small animals entering from the pipe penetration part, close the part with some sealing material (to be arranged on site).
●
I
n the case of an installation using a collective drain system, use a port other than the bottom one to take out cables and pipes. If the bottom port is used, seal it thoroughly so
that drain water may not spill out.
●
Use an elbow (to be arranged on site) to connect control valves to the piping.
●
In anchoring piping on the installation site, give 1.5m or a longer distance between an outdoor unit and an anchoring point where the piping is secured as illustrated below. (A
failure to observe this instruction may result in a pipe fracture depending on a method of isolating vibrations employed.)
●
The pipe should be anchored every 1.5m or less to isolate the vibration.
H
Flare nut parallel side
measurement: H (mm)
φ
6.35
φ
9.52
φ
12.7
φ
15.88
Copper
pipe outer
diameter
H
17
22
26
29
A
B
Flared pipe end: A (mm)
φ
6.35
φ
9.52
φ
12.7
φ
15.88
Copper
pipe outer
diameter
0
-0.4
A
9.1
13.2
16.6
19.7
φ
6.35
φ
9.52
φ
12.7
φ
15.88
Copper
pipe outer
diameter
In the case of a rigid (clutch) type
With an R410A tool
With a conventional tool
0
〜
0.5
0.7
〜
1.3
CAUTION
If you tighten it without using double spanners, you may deform the
outdoor unit.
●
Take care so that installed pipes may not touch components within a unit.
●
During the pipe installation at site, keep the service valves shut all the time
.
●
Give
(compressed and brazed or by an adhesive tape)
to pipe ends so that any water or foreign matters may not enter the pipes
.
●
In bending a pipe, bend it
to the largest possible radius (at least four times the pipe diameter)
. Do not bend a pipe repeatedly to correct its form.
●
e size for R410A is different from that for
an also be used by adjusting the
measurement of protrusion B with a protrusion control gauge.
●
Be sure to use the accessory pipe for connection to the gas operation valve. For details, refer to the installation manual of the accessory pipe.
●
with two spanners
Use a torque wrench. If a torque wrench is not available,
further, using the left table as a guide.
Do not hold the valve cap area with a spanner.
●
●
failure
from capillary tube or expansion valve clogging.
●
Brazing of the service valve and the pipes should be performed while cooling the valve body with a wet towel.
●
Plug the end of the pipe with tape, or other
Only use nitrogen gas (N
2
)
Taping
<
N
2
>
Nitrogen
Brazing
Brazing
Flatten
Adhesive tape
Station valve
Primary side
Secondary side
0.02MPa
Hand
Relief valve
Nitrogen
gas
Operation procedure
①
During the pipe installation at site, keep the service valves shut all the time
.
②
. Without nitrogen gas, a large
tube or expansion valve clogging.
③
Give
(compressed and brazed or with an adhesive tape)
so that water or foreign matters may not enter the piping
.
④
Nitrogen
gas
①
Although an outdoor unit itself has been tested for air tightness at the factory, check the connected pipes and indoor units for air tightness from the check joint of the
service valve on the outdoor unit side. While conducting a test,
keep the service valve shut all the time
.
②
Since refrigerant piping is pressurized to the design pressure of a unit with nitrogen gas for testing air tightness, connect instruments according the drawing below.
Under no circumstances should chlorine-based refrigerant, oxygen or any other combustible gas be used to pressurize a system.
Keep the service valve shut all the time
. Do not open it under any circumstances.
Be sure to pressurize all of the liquid, gas pipes
.
③
a)
to see if the pressure drops.
b)
to see if the pressure drops.
d)
If no pressure drop is observed with an installation pressurized to
and left for about one day
,
it is acceptable
. When the ambient temperature
changes 1
℃
, the pressure also changes approximately 0.01 MPa. The pressure, if changed, should be compensated for.
After repair, conduct an air-tightness test again.
④
Always pull air from the pipes after the airtightness test.
To indoor unit
Gauge manifold
Lo
Lo knob
Hi
Hi knob
Service point
(check joint)
Operation valve
Liquid pipe
Gas pipe
Outdoor unit
CAUTION
Applying excessive pressure can cause an
①
Dress refrigerant pipes (both gas and liquid pipes) for heat insulation and prevention of dew condensation.
Improper heat insulation/anti-dew dressing can result in a water leak or dripping causing damage to household effects, etc.
②
Use a heat insulating material that can withstand 120
℃
or a higher temperature. Poor heat insulating capacity can cause heat
insulation problems or cable deterioration.
a) The gas pipe can cause dew condensation during a cooling operation, which will become drain water causing a possible
water-leak accident, or reach as high a temperature as 60
℃
to 110
℃
during a heating operation, posing a risk of burns,
when touched accidentally. So, do not fail to dress it with a heat insulation material.
c) Give heat insulation to both gas and liquid side pipes. Bundle a heat insulating material and a pipe tightly together so that no
gaps may be left between them and wrap them together with a connecting cable by a dressing tape.
d)
Both gas and liquid pipes need to be dressed with 20 mm or thicker heat insulation materials above the ceiling
where relative humidity exceeds 70%.
When the ambient dew point temperature becomes 28
℃
or higher, or the relative humidity becomes 80% or higher, add
further 10 to 20 mm thickness heat insulation material.
Wires for connecting indoor
and outdoor units
Exterior tape
Gas piping
Insulation
Liquid piping
Band (accessory)
Pipe cover (accessory)
Electrical installation work must be executed according to the technical standards and other regulations applicable to electrical installations in the country.
Install an earth leakage breaker without fail
(Since this unit employs inverter control,
use an impulse withstanding type
to prevent an earth leakage breaker’s false actuation.)
220/240V
〜
50Hz
220V
〜
60Hz
CAUTION
If the earth leakage breaker is exclusively for ground fault protection,
then you will need to install a circuit breaker for wiring work.
Round crimp
contact terminal
Crimp
contact terminal
Diameter of a cable:thin
Diameter of a cable:thick
Wire
Block terminal for power souce
(L1, L2, L3, N, )
(1) Method of leading out cables
●
As shown on the drawing in Section 4-2, cables can be laid through the front, right, rear or bottom casing.
●
In wiring on the installation site, cut off a half-blank covering a penetration of the casing with nippers.
●
In the case of an installation using a collective drain system, use a port other than the bottom one to take out cables and pipes. If the bottom port is used, seal it thoroughly so that drain water may
not spill out.
(2) Notabilia in connecting power cables
●
Connect the ground wire before you connect the power cable. When you connect a grounding wire to a terminal block, use a
grounding wire longer than the power cable so that it may not be subject to tension.
●
Do not turn on power until installation work is completed. Turn off power to the unit before you service the unit.
●
Ensure that the unit is properly grounded.
●
of operation valve.
●
To connect a cable to the power terminal block, use a round crimp contact terminal.
If two cables are to be connected to one terminal, arrange cables in such a manner that you put their crimp contact terminals
together back to back. Further, put the thinner cable above the thicker one in arranging cables for such connection.
●
●
In fastening a screw of a terminal block, use a correct-size driver.
Fastening a screw of a terminal block with excessive force can break the screw.
●
When electrical installation work is completed, make sure that all electrical components within the electrical component box are free
of loose connector coupling or terminal connection.
Terminal block
380/415V 3N
〜
50Hz
380V 3N
〜
60Hz
Note
a) Use only copper wires.
- braided cord (code designation 60245 IEC 51), if allowed in the relevant part 2;
- ordinary tough rubber sheathed cord (code designation 60245 IEC 53);
- ordinary polyvinyl chloride sheathed cord (code designation 60227 IEC 53).
b)
Use separate power sources for the indoor and outdoor units
.
c) A grounding wire must be connected before connecting the power cable. Provide a grounding wire longer than the power cable.
d)
The power sources for indoor units in the same system should turn on and off simultaneously
.
e) Ground the unit. Do not connect the grounding wire to a gas pipe, water pipe, lightning rod or telephone grounding wire.
If improperly grounded, an electric shock or malfunction may result.
Never connect the grounding wire to a gas pipe because if gas leaks, it could cause explosion or ignition.
f)
The installation of an impulse withstanding type earth leakage breaker is necessary
turn on the power until the electrical work is completed. Be sure to turn off the power when servicing.
g) Do not use a condensive capacitor for power factor improvement under any circumstances. (It does not improve power factor, while it can cause an abnormal overheat accident)
h) For power source cables, use conduits.
i)
Do not lay electronic control cables (remote control and signaling wires) and other high current cables together outside the unit
. Laying them together can result in malfunctioning or a failure of
the unit due to electric noises.
j) Power cables and signaling wires must always be connected to the power cable terminal block and secured by cable fastening clamps provided in the unit.
k) Fasten cables so that they may not touch the piping, etc.
l)
When cables are connected, make sure that all electrical components within the electrical component box are free of loose connector coupling or terminal connection
and then attach the
cover securely. (Improper cover attachment can result in malfunctioning or a failure of the unit, if water penetrates into the box.)
breaker should isolate all poles under over current.
n) Install isolator or disconnect switch on the power supply wiring in accordance with the local codes and regulations. The isolator should be locked in OFF state in accordance with EN60204-1.
o) After maintenance, all wiring, wiring ties and the like, should be returned to their original state and wiring route, and the necessary clearance from all metal parts should be secured.
Block terminal for signal line
(A1, B1, A2, B2)
Attached on the front service panel.
Refrigerant quantity label
CAUTION
Charge additional refrigerant
in the liquid state.
Be sure to measure the quantity
with a scale in adding refrigerant.
If you cannot charge all refrigerant with the outdoor unit lying idle, charge it with the unit running in the test run mode. (For the test run method, refer to Section 8)
during operation, complete the job within 30min.)
This unit contains
8.9 kg of refrigerant
.
Calculate necessary quantity of additional charge with the following formula, and record the quantity of additionally charged refrigerant on the refrigerant quantity list provided
on the front of service panel.
●
Charge the additional refrigerant depending on the size and length of liquid pipe. Determine the quantity of additional charge by rounding the second place after decimal point,
which means in the unit of 0.1 kg.
(2) Field piping work
Important
Securely tighten the cap and the blind nut after the adjustment.
Avoid applying any excessive force when operating the shaft or when
tightening the cap or blind nut. Otherwise, it could cause malfunction or
leakage from the shaft, cap or blind nut.
(2) Vacuuming
Pull the air
from the check joints of the operation valves on both liquid and gas sides.
L1: Total length of ø9.52 pipes (m), L2: Total length of ø6.35 pipes (m)
●
Request
Record the refrigerant quantity calculated based
on the piping length in the refrigerant quantity
label provided on the front of service panel.
4-5. Heating and condensation prevention
Refrigerant pipe size
Additional charge quantity(kg/m
)
ø9.52
0.054
ø6.35
0.022
Remark
6-2. Power source connection
6-1. Wiring system drawing
6. Electric wiring
5. DRAIN PIPING WORK
Operation valve size
(mm)
Tightening angle
(° )
Tightening torque
(N
・
m)
Recommended length of tool handle
(mm)
ø
6.35
(
1/4"
)
14
〜
18
45
〜
60
150
ø
9.52
(
3/8"
)
34
〜
42
30
〜
45
200
ø
12.7
(
1/2"
)
49
〜
61
30
〜
45
250
ø
15.8 8
(
5/8"
)
68
〜
82
15
〜
20
300
ø
19.05 (3/4"
)
100
〜
120
15
〜
20
450
Operation valve size
(mm)
Cap tightening torque
(N
・
m)
Shaft tightening torque
(N
・
m)
Check joint blind nut
tightening torque
(N
・
m)
ø
9.52
(
3/8"
)
6
〜
8
20
〜
30
10
〜
12
ø
12.7
(
1/2"
)
14
〜
16
25
〜
35
10
〜
12
ø
19.05 (3/4"
)
3
30
〜
35
12
〜
14
4-2. Piping work
Standard torque at sections on operation valve
Allen wrench
(M4)
Fluid/gas operation valve
Open
・
Open the valve stem till it hits the stopper. No need to apply
force more than that.
・
After the adjustment, replace the blind nut as it was.
・
After the adjustment, replace the cap as it
was.
Remove the cap and adjust as shown below
State at shipping (closed)
State of open
Pin type
▲
Allen wrench type
▲
Stopper
Pin
(1) Pipe connecting position and pipe outgoing direction
〈Ⅰ〉
Power source (outdoor unit side)
Outdoor unit
Power source (indoor unit side)
Grounding work
Grounding work
Earth leakage
breaker
Circuit breaker
for cabling
Earth leakage
breaker
Circuit breaker
for cabling
Indoor unit
Remote control wire
〈Ⅱ〉
X・Y
X・Y
X・Y
X・Y
X・Y
X・Y
A・B
A・B
L1・L2・L3・N
1
・
2
1
・
2
Signal wire (between indoor units)
Remote
control
〈Ⅷ〉
A・B
1
・
2
・・・
・・・
・・・
・・・
A1・B1
Signal wire (between outdoor - indoor units
〈Ⅰ〉
)
4-3. Air tightness test and vacuuming
(1) Air tightness test
Additional charge quantity for piping P (kg)
=
(L1×0.054
)+
(L2×0.022
)
<If P
≦
1.6kg>
Important
Total additional charge quantity = P (kg)
<If P
>
1.6kg>
Total additional charge quantity = P (kg) + 1.0 (kg)
Charge quantity for the refrigerant piping
Legend A Attached pipe connecting outlet at refrigerant gas side (
φ
19.05 Flare)
B Pipe connection outlet at liquid refrigerant side (
φ
9.52 Flare)
C Power cable outlet (Front side, Right side)(
φ
30 2places)
D Power cable outlet (Front side, Right side)(
φ
45 2places)
E Power cable outlet (Back side)(
φ
50)
F Refrigerant pipe and Power cable outle (4 places)
G Drain outlet (
φ
20 3places)
H Anchor bolt position (M10 4places)
The hook used in order to
prevent a fall the panel.
Hock (Left)
Hock (Right)
Front connection
Pipe fastening positon
Over 1.5m
Bottom connection
Right-hand side connection
Rear connection
Outdoor unit
Block terminal for power cable
SSA011H003
gases covered by the Kyoto Protocol.
Ce produit contient des gaz à effets de serre
Treibhausgase,
die unter das Kyoto-Protokoll fallen.
serra trattati nei Protocollo di Kyoto.
invernadero incluidos en el Protocolo de Kyoto.
die vallen onder de voorschriften van het Kyoto Protocol.
de estufa, abrangidos pelo protocolo de Quioto.
Refrigerant - Réfrigérant - Kältemittel - Refrigerante -
Refrigerante - Koudemiddel - Frigorigéneo -
Additional Charge - Charge complémentaire -
Zusätzllche Füllmenge - Quantità aggiuntiva -
Carga adicional - Aanvullende lading -
Carga Adicional -
Total Charge (
① ②
) - Charge totale (
① ②
) -
Gesamte Füllmenge (
① ②
) -
Quantità totale (
① ②
) - Carga total (
① ②
) -
Totale lading (
① ②
) - Carga Total (
① ②
) -
(
① ②
)
Factory Charge (See Model Name Label)-
Charge en usine (Voir la plaque signalétlque de l'appareil)-
Werkseitige Füllmenge (Siehe Modell-Typenschild)-
Quantità caricata in fabbrica (Si prega di vedere
la targhetta del nome del modello)-
Carga de fàbrica (Consulte la etiqueta de nombre del modelo)-
Fabriekslading (Zie ook het typeplaatje met het modelnummer)-
Carga da Fábrica (Ver a etiqueta de caracteristicas)-
(EN)
(FR)
(DE)
(IT)
(ES)
(NL)
(PT)
(GR)
R410A
kg
kg
①
②
●
When condensed water needs to be led to a drain,
blocks. (prepared on site)
Then, secure space for the drain elbow and the
drain hose.
●
Execute drain piping by using a drain elbow and drain grommets
supplied separately as optional parts, where water drained from
the outdoor unit is a problem.
●
Water may drip where there is a larger amount of drain water. Seal
around the drain elbow and drain grommets with putty or
adequate caulking material.
●
connected pipes.
●
Where you are likely to have several days of sub-zero
temperatures in a row, do not use a drain elbow and drain
grommets. (There is a risk of drain water freezing inside and
blocking the drain.)
●
Do not use drain elbow and grommet made of plastic for drain
piping when base heater for outdoor unit is used. Plastic grommet
and elbow will be damaged and burnt in worst case.
●
Prepare another drain tray made of metallic material for collecting
drain when base heater is used.
Drain elbow
Grommet
Grommet
Drain hose
To be procured on
the installer's part
Clearance
Pay attention to the following points in addition to the above for the R410A and compatible machines.
○
To prevent a different oil from entering, assign dedicated tools, etc. to each refrigerant type. Under no circumstances must a gauge manifold and a charge
hose in particular be shared with other refrigerant types (R22, R407C, etc.).
○
Airtighteness test completed
Fill refrigerant
Vacuum gauge check
Vacuuming completed
Vacuuming begins
Run the vacuum pump for at least one hour after the vacuum gauge shows
-101kPa or lower. (-755mmHg or lower)
left for one hour or more.
When the system has remaining moisture
inside or a leaky point, the vacuum gauge
indicator will rise.
Check the system for a leaky point and
then draw air to create a vacuum again.
4-4. Additional charge of refrigerant
Pay attention to the following points in addition to the above for the R410A and compatible machines.
●
According the amount of P, the total additional charge quantity can be calculated.
When the total additional charge quantity is over 9.1kg, separate the refrigerant line.
○
To prevent a different oil from entering, assign dedicated tools, etc. to each refrigerant type. Under no circumstances must a gauge manifold and a charge hose in particular be
shared with other refrigerant types (R22, R407C, etc.).
○
○
Do not use a charge cylinder under any circumstances. There is a danger that the composition of the refrigerant will change when R410A is transferred to a cylinder.
○
When charging refrigerant, use liquid refrigerant from a cylinder. If refrigerant is charged in a gas form, the composition may change considerably.
Be sure to record the refrigerant volume, because the information is
necessary to perform the installation’s maintenance service.